Aluminum brazing is a versatile joining process widely used across various industries due to its ability to create strong, leak-proof, and corrosion-resistant joints. It is particularly favored for applications where lightweight materials with high thermal and electrical conductivity are required. The process involves joining aluminum parts using a filler metal that melts at a lower temperature than the base metal, ensuring minimal distortion and maintaining the integrity of the components. Below, we explore the key applications of aluminum brazing in detail.
Key Points Explained:
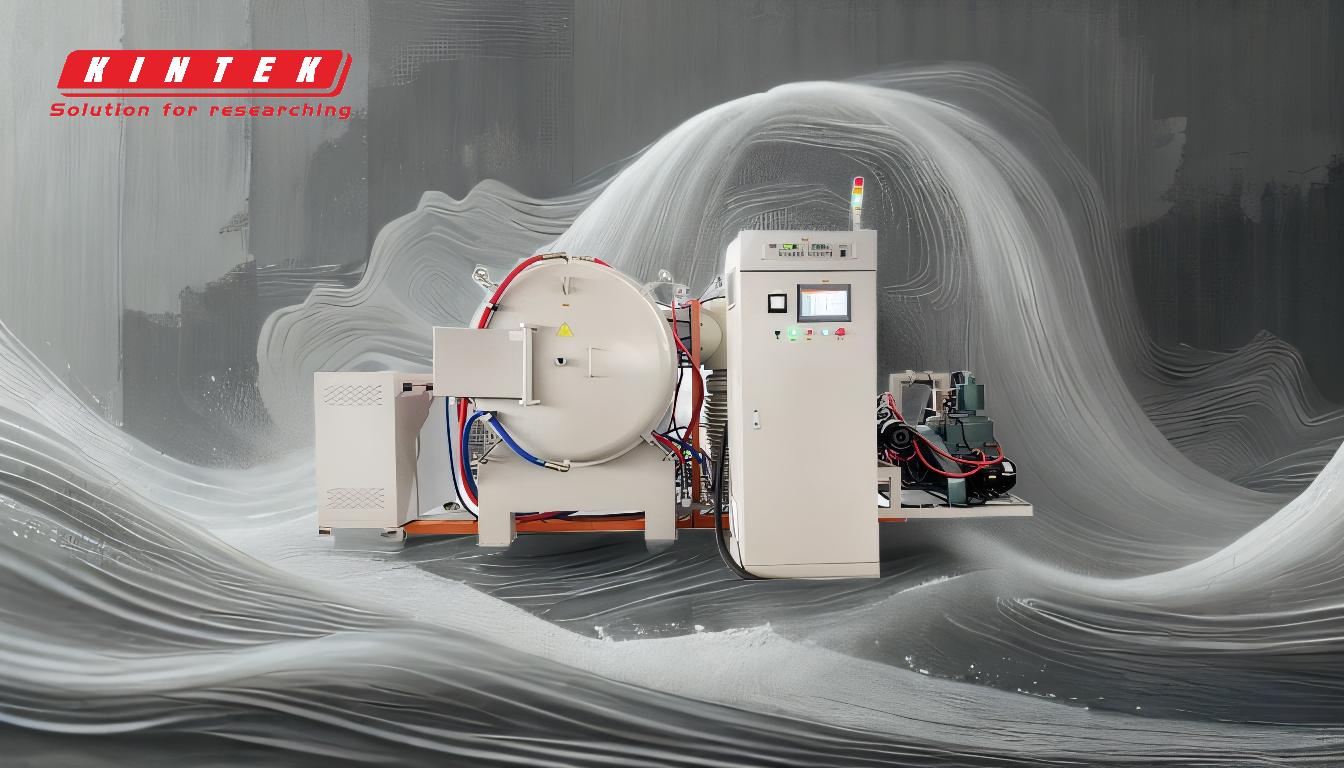
-
Aerospace Industry
- Aluminum brazing is extensively used in the aerospace sector for manufacturing lightweight and durable components such as heat exchangers, fuel systems, and structural parts.
- The process ensures high strength-to-weight ratios, which is critical for aircraft performance and fuel efficiency.
- Components like air-cooled heat exchangers and evaporators are often brazed to withstand extreme temperatures and pressures encountered during flight.
-
Defense Sector
- In defense applications, aluminum brazing is employed to produce components that require high reliability and resistance to harsh environments.
- Examples include radar systems, missile components, and armored vehicle parts.
- The corrosion resistance of brazed aluminum joints makes them ideal for use in marine and field environments.
-
Power Generation
- Aluminum brazing is used in the power generation industry to create heat exchangers, condensers, and cooling systems for power plants.
- These components must efficiently transfer heat while resisting corrosion from cooling fluids and environmental exposure.
- The lightweight nature of aluminum also simplifies installation and maintenance.
-
Commercial Applications
- In commercial settings, aluminum brazing is used to produce HVAC systems, refrigeration units, and heat exchangers for industrial machinery.
- The process ensures leak-proof joints, which are essential for systems handling refrigerants or other fluids.
- Aluminum's thermal conductivity makes it ideal for applications requiring efficient heat transfer.
-
Automotive Industry
- The automotive sector relies on aluminum brazing for manufacturing components such as radiators, air conditioning systems, and transmission coolers.
- Brazed aluminum parts contribute to vehicle weight reduction, improving fuel efficiency and reducing emissions.
- The process also supports the production of complex geometries, such as intricate hydraulic fittings and machined assemblies.
-
Medical and Scientific Industries
- Aluminum brazing is used to create precision components for medical devices and scientific equipment.
- Examples include MRI machines, laboratory instruments, and surgical tools.
- The process ensures clean, contamination-free joints, which are critical for maintaining hygiene and accuracy in these applications.
-
Advantages of Aluminum Brazing
- Lightweight: Aluminum is significantly lighter than other metals, making it ideal for applications where weight reduction is crucial.
- Corrosion Resistance: Brazed aluminum joints are highly resistant to corrosion, ensuring longevity in harsh environments.
- Thermal and Electrical Conductivity: Aluminum's excellent conductivity makes it suitable for heat exchangers and electrical components.
- Cost-Effectiveness: The process is relatively low-cost compared to other joining methods, especially for large-scale production.
In summary, aluminum brazing is a critical process across multiple industries, offering a combination of strength, durability, and efficiency. Its applications range from aerospace and defense to automotive and medical sectors, making it an indispensable technique in modern manufacturing.
Summary Table:
Industry | Applications |
---|---|
Aerospace | Heat exchangers, fuel systems, structural parts |
Defense | Radar systems, missile components, armored vehicle parts |
Power Generation | Heat exchangers, condensers, cooling systems |
Commercial | HVAC systems, refrigeration units, industrial machinery |
Automotive | Radiators, air conditioning systems, transmission coolers |
Medical & Scientific | MRI machines, laboratory instruments, surgical tools |
Interested in leveraging aluminum brazing for your industry? Contact us today to learn more!