Physical Vapor Deposition (PVD) is a versatile and widely used technology for applying thin films to various substrates, enhancing their mechanical, optical, chemical, or electronic properties. Its applications span multiple industries, including semiconductor manufacturing, aerospace, biomedical, and decorative coatings. PVD is particularly valued for its ability to improve wear resistance, corrosion resistance, and optical performance, making it indispensable in modern manufacturing and advanced material science. Below, we explore the key applications of PVD in detail.
Key Points Explained:
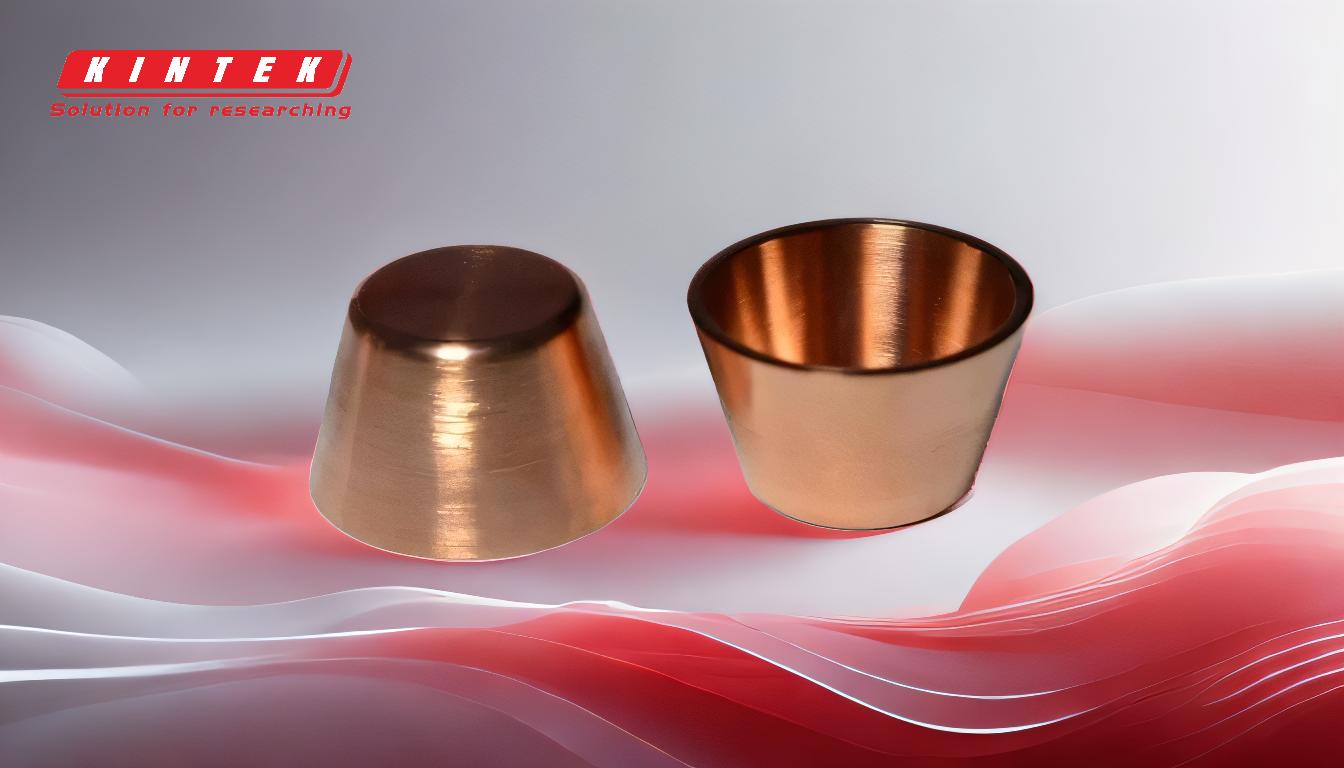
-
Semiconductor Device Manufacturing
- PVD is extensively used in the semiconductor industry to deposit thin films that provide semiconductor properties to substrates. These films are critical for the fabrication of microelectronic components, integrated circuits, and thin-film solar panels.
- Examples include metallic coatings for conductive layers and magnetic film coatings for data storage devices.
- The ability to create precise, uniform, and high-quality thin films makes PVD a cornerstone of semiconductor technology.
-
Cutting Tools and Mechanical Components
- PVD coatings, such as titanium nitride (TiN), are applied to cutting tools and mechanical components to enhance their hardness, wear resistance, and corrosion resistance.
- These coatings extend the lifespan of tools used in metalworking, machining, and other high-stress applications.
- The process also improves the performance of tools in extreme environments, such as high temperatures or corrosive conditions.
-
Decorative Coatings
- PVD is widely used in the jewelry and luxury goods industries to create durable and aesthetically pleasing decorative coatings.
- Common applications include gold, rose gold, and black coatings on watches, bracelets, and other accessories.
- These coatings are not only visually appealing but also resistant to tarnishing and scratching, making them ideal for high-end products.
-
Optical and Reflective Coatings
- PVD is employed to produce highly reflective and optically functional coatings for applications such as solar glasses, mirrors, and optical film stacks.
- These coatings act as barriers to reflect or transmit specific wavelengths of light, making them essential for solar energy systems, telescopes, and other optical devices.
- The precision of PVD ensures consistent optical performance across large surface areas.
-
Aerospace Industry
- In aerospace, PVD coatings are used to enhance the performance and durability of components exposed to extreme conditions, such as high temperatures, friction, and corrosion.
- Examples include coatings on turbine blades, engine components, and structural parts.
- The lightweight and high-strength properties of PVD coatings contribute to fuel efficiency and safety in aerospace applications.
-
Biomedical Applications
- PVD is utilized in the biomedical field to create biocompatible coatings on implants and surgical tools.
- These coatings improve wear resistance, reduce friction, and prevent corrosion, ensuring the longevity and safety of medical devices.
- Examples include coatings on orthopedic implants, dental instruments, and cardiovascular stents.
-
Conductive Layers for Electron Microscopy
- PVD is used to deposit conductive layers on samples for electron microscopy, enabling high-resolution imaging and analysis.
- These coatings ensure that non-conductive samples can be effectively examined without charging artifacts.
- The process is critical for research and development in materials science, biology, and nanotechnology.
-
Food Packaging and Balloons
- PVD is applied to aluminized PET films used in food packaging and balloons.
- These coatings provide a barrier to oxygen and moisture, extending the shelf life of packaged goods.
- The lightweight and flexible nature of PVD-coated films make them ideal for applications requiring both durability and functionality.
-
Environmental and Industrial Benefits
- PVD is an environmentally friendly process that minimizes waste and reduces the need for hazardous chemicals.
- Its ability to enhance the chemical and wear resistance of materials like stainless steel and titanium makes it a sustainable choice for industrial applications.
- The process is also energy-efficient, contributing to its widespread adoption across industries.
In summary, PVD is a critical technology with diverse applications across industries. Its ability to create thin, durable, and functional coatings makes it indispensable in modern manufacturing, from semiconductor devices and cutting tools to decorative jewelry and biomedical implants. The precision, versatility, and environmental benefits of PVD ensure its continued relevance in advancing material science and industrial innovation.
Summary Table:
Industry | Applications |
---|---|
Semiconductor Manufacturing | Thin films for microelectronics, conductive layers, and data storage devices |
Cutting Tools | Titanium nitride (TiN) coatings for wear and corrosion resistance |
Decorative Coatings | Durable gold, rose gold, and black coatings for jewelry and luxury goods |
Optical Coatings | Reflective coatings for solar glasses, mirrors, and optical devices |
Aerospace | Coatings for turbine blades, engine components, and structural parts |
Biomedical | Biocompatible coatings for implants, surgical tools, and medical devices |
Electron Microscopy | Conductive layers for high-resolution imaging and analysis |
Food Packaging | Aluminized PET films for oxygen and moisture barriers in packaging |
Environmental Benefits | Eco-friendly process enhancing wear and chemical resistance of materials |
Unlock the potential of PVD for your industry—contact our experts today to learn more!