The Physical Vapor Deposition (PVD) method is a versatile and widely used technique in various industries due to its ability to produce high-quality, durable, and functional coatings. PVD involves the deposition of thin films of material onto a substrate through the physical process of vaporization and condensation. This method is particularly valued for its applications in enhancing surface properties such as hardness, wear resistance, and corrosion resistance. Key industries utilizing PVD include electronics, automotive, aerospace, medical devices, and decorative coatings. Additionally, PVD is instrumental in the development of advanced materials and nanotechnology, where precise control over film properties is crucial. The integration of PVD with other deposition techniques, such as microwave plasma chemical vapor deposition, further expands its capabilities, enabling the creation of complex multi-layer structures and tailored material properties.
Key Points Explained:
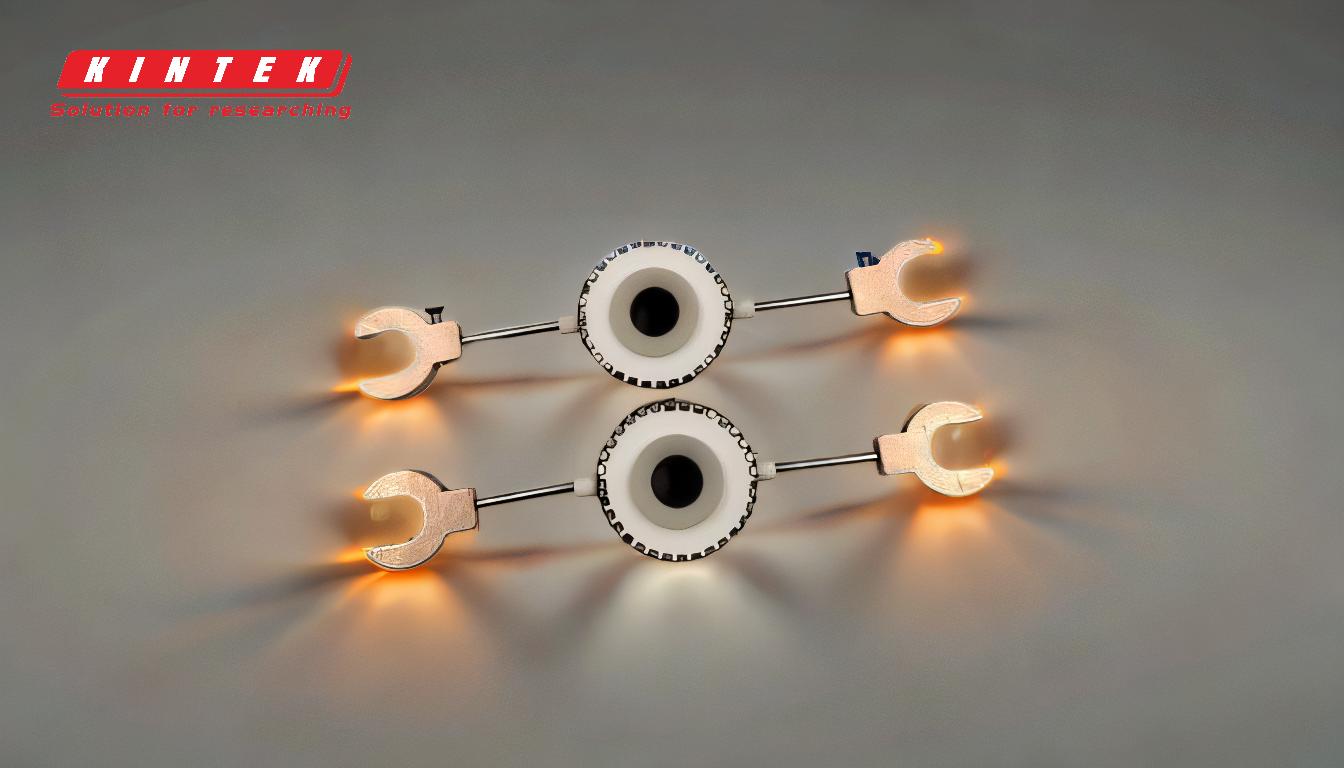
-
Electronics Industry:
- Semiconductor Manufacturing: PVD is extensively used in the production of semiconductors, where it deposits thin films of metals and dielectrics onto silicon wafers. These films are critical for the fabrication of integrated circuits, transistors, and other electronic components.
- Magnetic Storage: PVD is employed in the production of magnetic thin films used in hard disk drives and other data storage devices. The method ensures high precision and uniformity, which are essential for the performance of these storage media.
- Optoelectronics: In the field of optoelectronics, PVD is used to deposit thin films that are integral to the functioning of devices such as LEDs, solar cells, and photodetectors. The ability to control film thickness and composition is crucial for optimizing the optical and electrical properties of these devices.
-
Automotive and Aerospace:
- Wear and Corrosion Resistance: PVD coatings are applied to various automotive and aerospace components to enhance their durability and resistance to wear and corrosion. For example, PVD-coated tools and engine parts exhibit extended lifespans and improved performance under harsh operating conditions.
- Decorative Coatings: PVD is also used to apply decorative coatings on automotive trim and aerospace interiors. These coatings provide a combination of aesthetic appeal and functional benefits, such as scratch resistance and color stability.
-
Medical Devices:
- Biocompatible Coatings: PVD is utilized to deposit biocompatible coatings on medical implants and devices. These coatings improve the compatibility of implants with biological tissues, reducing the risk of rejection and enhancing the longevity of the devices.
- Antimicrobial Surfaces: PVD can be used to create antimicrobial surfaces on medical instruments and equipment. These surfaces help to prevent the spread of infections in healthcare settings.
-
Decorative Applications:
- Jewelry and Watches: PVD is widely used in the jewelry and watchmaking industries to apply durable and aesthetically pleasing coatings. These coatings can mimic the appearance of precious metals while offering superior resistance to tarnishing and wear.
- Architectural Glass: PVD coatings are applied to architectural glass to enhance its properties, such as thermal insulation, solar control, and self-cleaning capabilities. These coatings contribute to energy efficiency and sustainability in building design.
-
Advanced Materials and Nanotechnology:
- Thin Film Deposition: PVD is a key technique in the development of advanced materials, including thin films with tailored electrical, optical, and mechanical properties. These materials are used in a wide range of applications, from sensors and actuators to energy storage devices.
- Nanostructured Coatings: PVD enables the creation of nanostructured coatings with unique properties, such as superhydrophobicity, self-healing, and enhanced catalytic activity. These coatings are used in various high-tech applications, including microelectronics, photovoltaics, and biomedical devices.
-
Integration with Other Deposition Techniques:
- Hybrid Deposition Methods: PVD is often combined with other deposition techniques, such as microwave plasma chemical vapor deposition, to create complex multi-layer structures and composite materials. This integration allows for the precise control of film properties and the development of novel materials with enhanced performance characteristics.
- Enhanced Film Properties: The combination of PVD with other methods can result in films with improved adhesion, density, and uniformity. This is particularly important for applications requiring high-performance coatings, such as in the aerospace and defense industries.
In summary, the PVD method is a cornerstone technology in modern materials science and engineering, offering a wide range of applications across multiple industries. Its ability to produce high-quality, durable, and functional coatings makes it indispensable in the development of advanced materials and nanotechnology. The integration of PVD with other deposition techniques, such as microwave plasma chemical vapor deposition, further enhances its capabilities, enabling the creation of innovative materials and devices with tailored properties.
Summary Table:
Industry | Applications |
---|---|
Electronics | Semiconductor manufacturing, magnetic storage, optoelectronics |
Automotive/Aerospace | Wear and corrosion resistance, decorative coatings |
Medical Devices | Biocompatible coatings, antimicrobial surfaces |
Decorative | Jewelry, watches, architectural glass |
Advanced Materials | Thin film deposition, nanostructured coatings |
Integration | Hybrid deposition methods with enhanced film properties |
Unlock the potential of PVD for your industry—contact our experts today to learn more!