Silicon carbide (SiC) is a versatile material with a wide range of applications across various industries due to its exceptional properties, such as high thermal conductivity, chemical resistance, and mechanical strength. Its uses span from traditional applications like abrasives and metallurgy to advanced applications in electronics, aerospace, and energy. SiC is employed in components like turbine parts, bearings, and heat exchangers, as well as in cutting-edge technologies such as semiconductor substrates for LEDs and protective coatings in nuclear reactors. Its ability to withstand extreme environments makes it indispensable in industries requiring high-performance materials.
Key Points Explained:
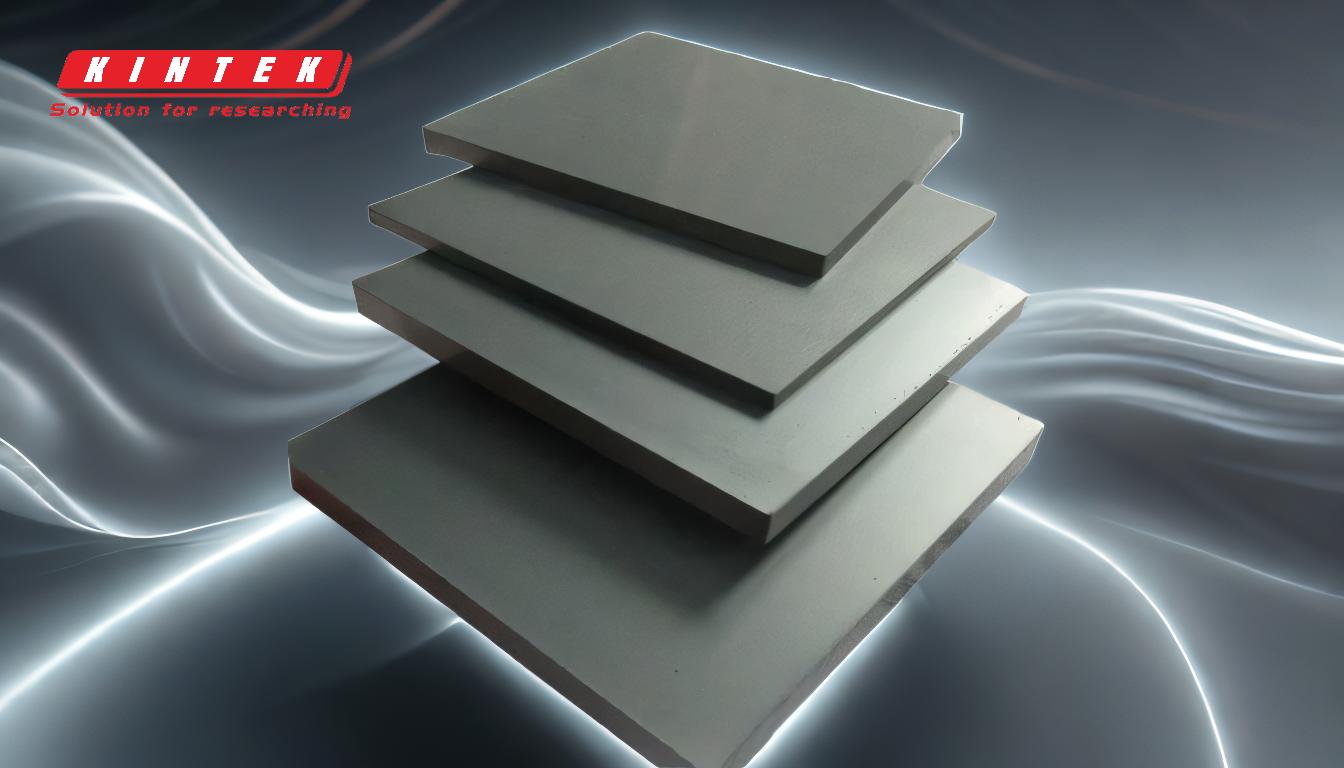
-
Abrasive and Metallurgical Applications
- Abrasives: Silicon carbide has been used for over a century as an abrasive material. It is commonly found in grinding wheels, sandpapers, and other abrasive products due to its hardness and durability.
- Metallurgy: SiC is used in both ferrous and non-ferrous metallurgy. It serves as a refractory material in furnaces and as a deoxidizing agent in steel production, enhancing the quality and efficiency of metal processing.
-
Industrial and Mechanical Components
- Turbine Components: SiC is utilized in fixed and moving turbine components, where its high thermal conductivity and resistance to wear make it ideal for high-temperature and high-stress environments.
- Bearings and Seals: Its low friction and high wear resistance make SiC suitable for bearings, seals, and ball valve parts, particularly in harsh operating conditions.
- Pumps and Rocket Engines: SiC is increasingly used in pump parts and rocket engines due to its ability to withstand extreme pressures and temperatures.
-
Thermal and Chemical Applications
- Heat Exchangers: SiC's excellent thermal conductivity and resistance to thermal shock make it a preferred material for heat exchangers in industries requiring efficient heat transfer.
- Industrial Furnaces: SiC is used in heating elements for industrial furnaces, where its ability to operate at high temperatures without degradation is critical.
- Chemical Resistance: SiC is employed in environments with corrosive chemicals, such as in chemical processing equipment, due to its high chemical inertness.
-
Electronics and Semiconductors
- Semiconductor Substrates: SiC is a key material in the production of semiconductors, particularly for light-emitting diodes (LEDs). Its wide bandgap and high thermal conductivity make it ideal for high-power and high-frequency electronic devices.
- Radio Engineering: SiC-based materials are used in radio engineering and electronics for components that require high thermal and electrical performance.
-
Advanced and Niche Applications
- Protective Coatings: SiC is used as a protective coating for nuclear fuel particles, providing a barrier against radiation and high temperatures.
- Aerospace and Defense: SiC's properties make it suitable for aerospace applications, including rocket engines and other components that require materials capable of withstanding extreme conditions.
-
Energy and Environmental Applications
- Nuclear Industry: SiC is used in the nuclear industry for its radiation resistance and thermal stability, making it a reliable material for protective coatings and structural components.
- Energy Efficiency: The use of SiC in heating elements and heat exchangers contributes to energy efficiency in industrial processes, reducing energy consumption and environmental impact.
In summary, silicon carbide's unique combination of properties—high thermal conductivity, chemical resistance, mechanical strength, and electrical conductivity—makes it a critical material in a wide array of industries. From traditional uses in abrasives and metallurgy to advanced applications in electronics and aerospace, SiC continues to play a vital role in enabling technological advancements and improving industrial processes.
Summary Table:
Application | Key Uses |
---|---|
Abrasives & Metallurgy | Grinding wheels, sandpapers, refractory materials, deoxidizing agents |
Industrial Components | Turbine parts, bearings, seals, pumps, rocket engines |
Thermal & Chemical Uses | Heat exchangers, industrial furnaces, chemical processing equipment |
Electronics & Semiconductors | LED substrates, high-power devices, radio engineering components |
Advanced Applications | Protective coatings, aerospace components, nuclear industry materials |
Energy Efficiency | Heating elements, energy-efficient industrial processes |
Discover how silicon carbide can transform your industry—contact our experts today for tailored solutions!