Thin films have become an integral part of modern engineering, offering unique properties and enabling advancements across a wide range of industries. They are used to create materials with enhanced optical, electrical, mechanical, and thermal properties, making them indispensable in applications such as semiconductors, solar cells, optical coatings, protective layers, and advanced electronics. Their versatility allows for lightweight, flexible, and efficient solutions in fields like aerospace, automotive, consumer electronics, and biomedical devices. Thin films are also crucial in developing energy-efficient technologies, such as photovoltaic cells and thin-film batteries, as well as in improving durability and performance in industrial tools and equipment. Their applications continue to expand, driven by ongoing research and innovation.
Key Points Explained:
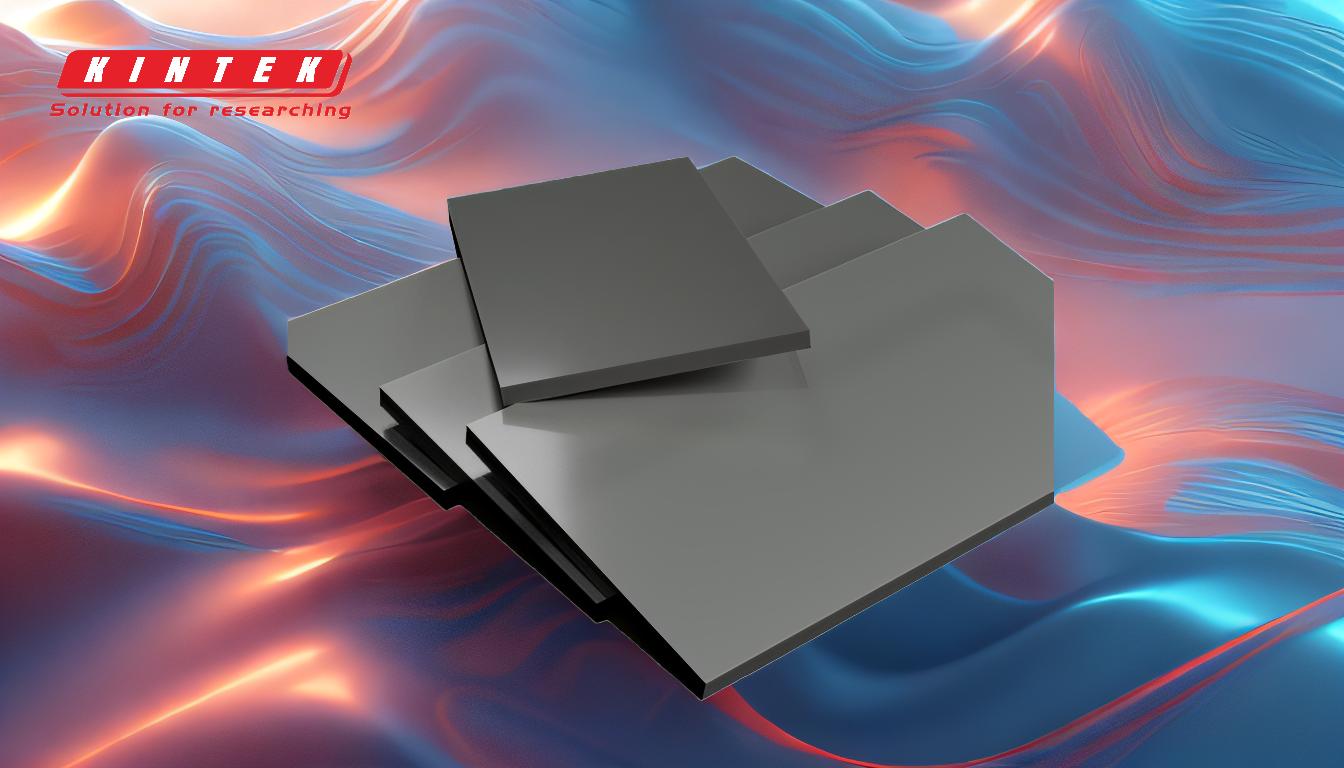
-
Semiconductors and Electronics:
- Thin films are essential in the production of semiconductors, including micro-electromechanical systems (MEMS) and thin-film transistors (TFTs).
- They enable the miniaturization of electronic components, improving performance and reducing space requirements.
- Applications include LED displays, OLED televisions, foldable smartphones, and smartwatches.
-
Optical Coatings:
- Thin films are used to create optical multilayer coatings, such as antireflective coatings, distributed Bragg reflectors, and narrow-bandpass filters.
- These coatings enhance the performance of lenses, mirrors, and displays by controlling light reflection and transmission.
- Examples include ophthalmic lenses, head-up displays in the automotive industry, and reflector lamp mirrors.
-
Energy Applications:
- Thin-film photovoltaic cells are a cost-efficient and lightweight alternative to traditional solar panels, making them ideal for renewable energy systems.
- Thin-film batteries are used in portable electronics and electric vehicles due to their compact size and flexibility.
- They also play a role in improving the efficiency of energy storage and conversion systems.
-
Protective and Decorative Coatings:
- Thin films provide wear protection and corrosion resistance for industrial tools, automotive parts, and architectural glass.
- Decorative applications include coatings on jewelry, bathroom fittings, and packaging foils for freshness preservation.
- Examples include chromium films for automobile parts and TiN coatings for cutting tools.
-
Aerospace and Military:
- Thin films are used in thermal barriers and lightweight materials for aerospace applications, reducing weight and improving fuel efficiency.
- They are also employed in military equipment for stealth technology, such as absorptive coatings that bend radiation in the electromagnetic spectrum.
-
Biomedical and Biosensors:
- Thin films are used in medical devices, biosensors, and plasmonic devices for diagnostics and monitoring.
- Their flexibility and biocompatibility make them suitable for wearable health monitors and implantable devices.
-
Emerging Applications:
- Thin films are being explored for new applications in flexible electronics, self-cleaning glass, and advanced communication devices.
- Their ability to reduce structure size to atomic dimensions opens possibilities for nanotechnology and quantum computing.
Thin films are a cornerstone of modern engineering, enabling innovations across diverse fields. Their unique properties and versatility make them indispensable for developing advanced technologies that improve efficiency, durability, and functionality. As research continues, their applications are expected to grow, further revolutionizing industries and everyday life.
Summary Table:
Application | Key Uses |
---|---|
Semiconductors & Electronics | MEMS, TFTs, LED displays, OLED TVs, foldable smartphones, smartwatches |
Optical Coatings | Antireflective coatings, Bragg reflectors, narrow-bandpass filters |
Energy Applications | Thin-film PV cells, thin-film batteries, energy storage systems |
Protective & Decorative | Wear protection, corrosion resistance, decorative coatings |
Aerospace & Military | Thermal barriers, lightweight materials, stealth technology |
Biomedical & Biosensors | Medical devices, biosensors, wearable health monitors |
Emerging Applications | Flexible electronics, self-cleaning glass, nanotechnology, quantum computing |
Ready to explore how thin films can transform your industry? Contact us today to learn more!