Controlled atmosphere brazing furnaces offer numerous benefits, making them a preferred choice for high-quality brazing processes. These furnaces provide precise control over temperature, time, pressure, and other parameters, ensuring optimal conditions for brazing, particularly for materials like aluminum. The controlled environment prevents oxide formation, enhances filler metal flow, and minimizes the need for flux, resulting in strong and reliable joints. Additionally, these furnaces are energy-efficient, environmentally friendly, and safe, making them suitable for a wide range of applications. Their ability to handle parts of various shapes and sizes, combined with advanced safety features and accurate controls, further underscores their advantages in modern manufacturing.
Key Points Explained:
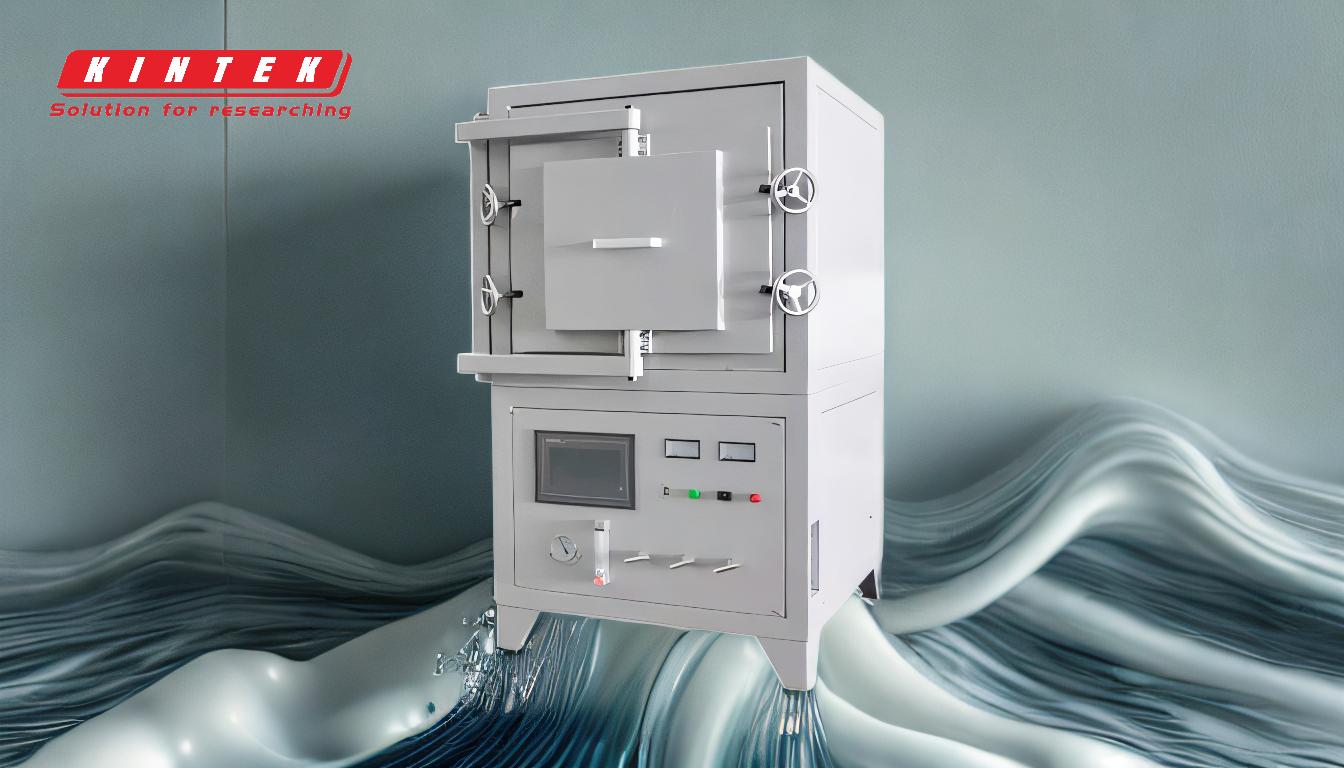
-
Precise Control of Brazing Parameters:
- Controlled atmosphere brazing furnaces allow for easy adjustment of temperature, time, pressure, and other critical parameters. This precision ensures optimal conditions for brazing, particularly for materials like aluminum, which require specific environmental conditions to achieve high-quality joints.
-
Prevention of Oxide Formation:
- A key benefit of using a controlled atmosphere furnace is its ability to prevent the formation of oxides on the surface of base metals. Oxides can hinder the wetting and flow of filler metals, leading to weak joints. The controlled atmosphere also helps remove existing oxides, ensuring proper filler metal flow and robust joint formation.
-
Reduced Flux Dependency:
- In traditional brazing processes, flux is often required to remove oxides and promote filler metal flow. However, with a controlled atmosphere, the need for flux is minimized or even eliminated. This not only reduces material costs but also simplifies the cleaning process post-brazing.
-
Energy Efficiency and Environmental Friendliness:
- Controlled atmosphere brazing furnaces are designed to be energy-efficient, reducing overall energy consumption. This efficiency translates to lower operating costs and a smaller environmental footprint, making them a sustainable choice for modern manufacturing.
-
Versatility in Application:
- These furnaces are highly versatile and can accommodate parts of various shapes and sizes. This flexibility makes them suitable for a wide range of industries, from automotive to aerospace, where complex and diverse components are common.
-
High Performance and Thermal Homogeneity:
- The furnaces offer high performance with consistent thermal homogeneity, ensuring uniform heating and cooling across the entire workpiece. This consistency is crucial for achieving high-quality brazed joints with minimal defects.
-
Advanced Safety Features:
- Safety is a paramount concern in any industrial process. Controlled atmosphere brazing furnaces come equipped with advanced safety devices that ensure safe operation, protecting both the equipment and the operators.
-
Differentiated Finish:
- The controlled environment in these furnaces allows for a differentiated finish on the brazed components. This is particularly important in industries where the aesthetic and functional quality of the final product is critical.
-
Alternative to Tube Furnaces:
- For applications where larger chamber volumes are needed and deep vacuum is not essential, controlled atmosphere furnaces serve as a perfect alternative to tube furnaces. This makes them suitable for a broader range of industrial applications.
-
Precise Temperature Control and Sealed Environment:
- The tightly sealed environment of a controlled atmosphere lab furnace ensures precise temperature control, which is critical for successful material processing. The ability to create protective or reactive atmospheres further enhances the quality of the brazing process, ensuring desired material properties are achieved during heating and cooling.
In summary, the benefits of using a controlled atmosphere brazing furnace are manifold, ranging from precise control and oxide prevention to energy efficiency and safety. These advantages make them an indispensable tool in modern manufacturing, particularly for industries requiring high-quality brazed joints.
Summary Table:
Benefit | Description |
---|---|
Precise Control of Brazing Parameters | Adjust temperature, time, and pressure for optimal brazing conditions. |
Prevention of Oxide Formation | Eliminates oxides, ensuring strong and reliable joints. |
Reduced Flux Dependency | Minimizes or eliminates the need for flux, reducing costs and cleaning efforts. |
Energy Efficiency | Lowers energy consumption and operating costs. |
Versatility in Application | Handles parts of various shapes and sizes for diverse industries. |
High Performance | Ensures uniform heating and cooling for defect-free joints. |
Advanced Safety Features | Equipped with safety devices for secure operation. |
Differentiated Finish | Delivers high-quality aesthetic and functional finishes. |
Alternative to Tube Furnaces | Ideal for larger chamber volumes without deep vacuum requirements. |
Precise Temperature Control | Maintains a tightly sealed environment for accurate material processing. |
Ready to enhance your brazing process? Contact us today to learn more about controlled atmosphere brazing furnaces!