Heat generation in hydraulic systems is a common issue that can lead to inefficiencies, component wear, and even system failure if not properly managed. The primary causes of heat generation in hydraulic systems include fluid friction, mechanical friction, and inefficiencies in the system's components. Understanding these causes is crucial for maintaining the system's performance and longevity.
Key Points Explained:
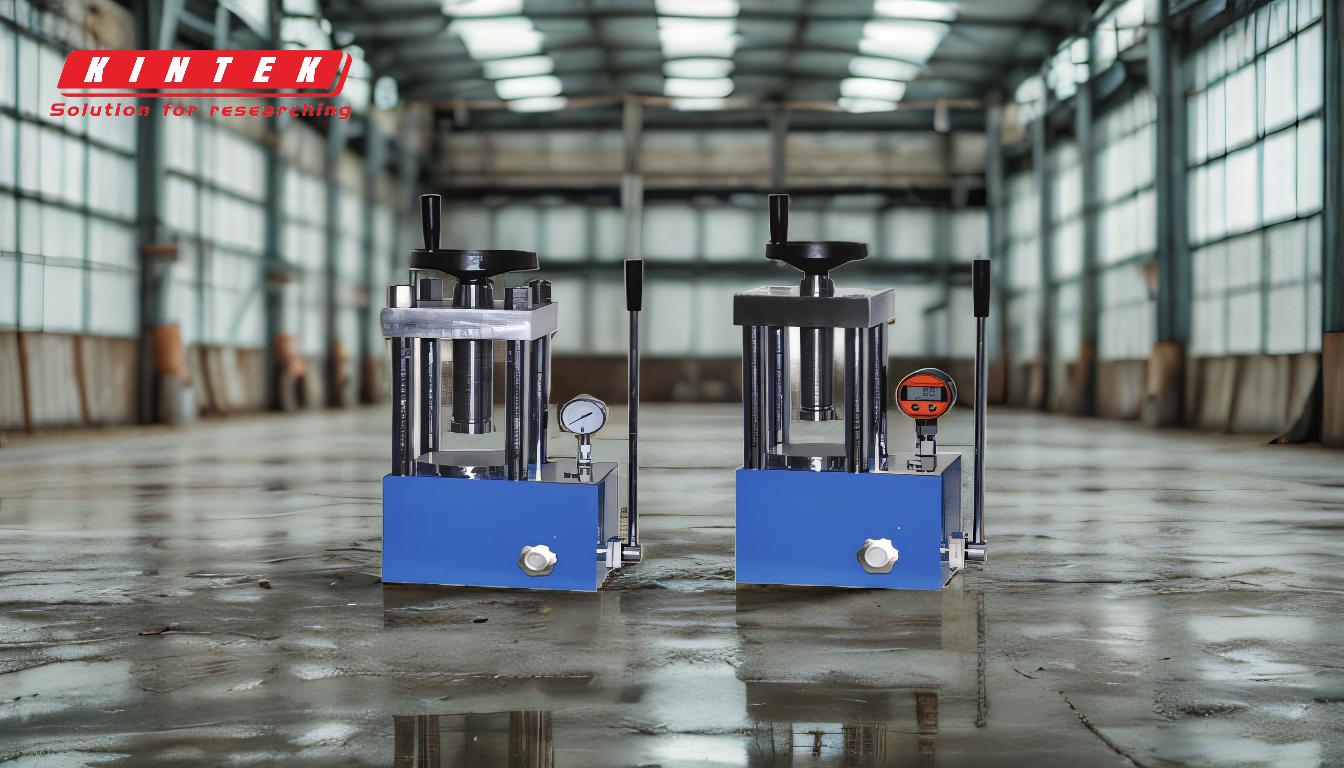
-
Fluid Friction:
- Description: Fluid friction occurs when hydraulic fluid moves through the system's components, such as pipes, valves, and cylinders. The resistance encountered by the fluid as it flows generates heat.
- Impact: High fluid friction can lead to increased temperatures, which may degrade the hydraulic fluid and reduce its lubricating properties. This can cause increased wear and tear on system components.
- Mitigation: Using hydraulic fluids with appropriate viscosity and ensuring smooth internal surfaces of components can help reduce fluid friction.
-
Mechanical Friction:
- Description: Mechanical friction is the resistance encountered when moving parts within the hydraulic system come into contact. This includes components like pumps, motors, and actuators.
- Impact: Excessive mechanical friction can lead to overheating, which may cause components to expand and seize, leading to system failure.
- Mitigation: Regular maintenance, proper lubrication, and using high-quality components can minimize mechanical friction.
-
Inefficiencies in Components:
- Description: Inefficiencies in hydraulic components such as pumps, valves, and actuators can lead to energy losses, which are converted into heat.
- Impact: These inefficiencies can result in higher energy consumption and increased operating temperatures, reducing the overall efficiency of the system.
- Mitigation: Selecting components with high efficiency ratings and ensuring they are correctly sized and installed can help reduce these inefficiencies.
-
External Heat Sources:
- Description: External heat sources, such as high ambient temperatures or nearby machinery, can contribute to the overall heat load in a hydraulic system.
- Impact: External heat can exacerbate the internal heat generation, leading to even higher system temperatures.
- Mitigation: Implementing cooling systems, such as heat exchangers or fans, and insulating components can help manage external heat sources.
-
System Design and Configuration:
- Description: Poor system design or configuration, such as undersized components, long hydraulic lines, or inadequate cooling, can lead to excessive heat generation.
- Impact: Inefficient design can cause the system to operate at higher temperatures, leading to reduced performance and potential failure.
- Mitigation: Proper system design, including the selection of appropriate components and the use of efficient hydraulic circuits, can help minimize heat generation.
-
Operational Conditions:
- Description: The operating conditions of the hydraulic system, such as high loads, rapid cycling, or continuous operation, can contribute to heat generation.
- Impact: Operating under extreme conditions can lead to increased heat production, which may exceed the system's cooling capacity.
- Mitigation: Monitoring and controlling operational conditions, such as load and cycle rates, can help manage heat generation.
By understanding and addressing these key points, it is possible to effectively manage heat generation in hydraulic systems, ensuring their efficient and reliable operation. Regular maintenance, proper component selection, and system design are essential strategies for mitigating the effects of heat generation.
Summary Table:
Cause | Description | Impact | Mitigation |
---|---|---|---|
Fluid Friction | Resistance from hydraulic fluid flowing through components like pipes and valves. | Increased temperatures, fluid degradation, and component wear. | Use appropriate viscosity fluids and ensure smooth internal surfaces. |
Mechanical Friction | Resistance from moving parts like pumps, motors, and actuators. | Overheating, component expansion, and potential system failure. | Regular maintenance, proper lubrication, and high-quality components. |
Inefficiencies in Components | Energy losses in pumps, valves, and actuators. | Higher energy consumption and reduced system efficiency. | Select high-efficiency components and ensure proper sizing and installation. |
External Heat Sources | Heat from high ambient temperatures or nearby machinery. | Increased system temperatures due to external heat. | Implement cooling systems like heat exchangers and insulate components. |
System Design | Poor design, such as undersized components or inadequate cooling. | Higher operating temperatures and reduced performance. | Optimize system design with efficient components and hydraulic circuits. |
Operational Conditions | High loads, rapid cycling, or continuous operation. | Increased heat production exceeding cooling capacity. | Monitor and control load and cycle rates. |
Need help managing heat in your hydraulic system? Contact our experts today for tailored solutions!