Pyrolysis, while a promising technology for sustainable development and waste management, faces several significant challenges that hinder its widespread adoption and efficiency. These challenges include the variability of feedstock materials, the need for advanced monitoring and control systems, and the technical difficulties associated with reactor design and energy efficiency. Additionally, the accumulation of metals and ash in reactor beds, the production of toxic by-products, and the high demands on process equipment further complicate the implementation of pyrolysis. These issues collectively make it difficult to scale up and apply pyrolysis technology in real-world conditions, requiring further research and development to overcome.
Key Points Explained:
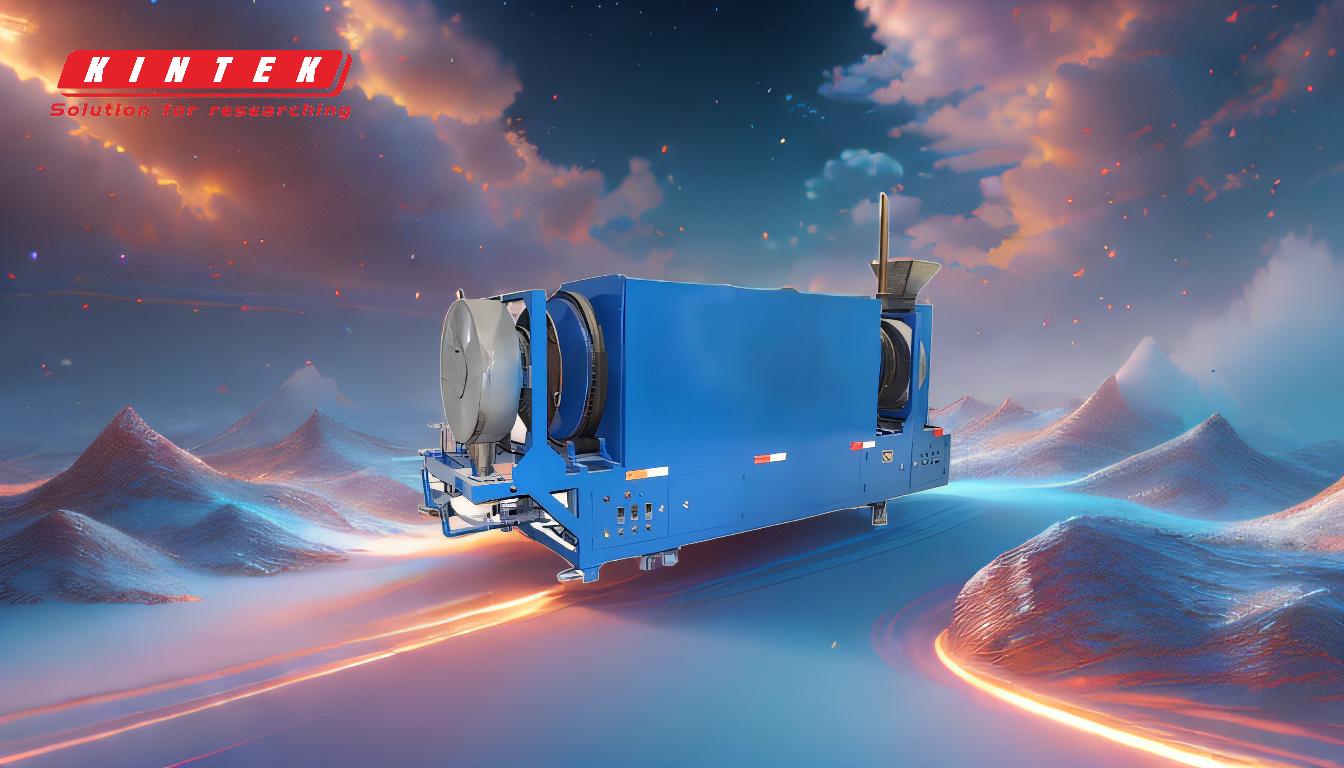
-
Variability of Feedstock Materials:
- Challenge: Pyrolysis processes often struggle with the treatment of variable feed materials, such as municipal solid waste (MSW). These materials can vary widely in composition, moisture content, and contamination levels, making it difficult to achieve consistent pyrolysis conditions and product yields.
- Impact: Inconsistent feedstock quality can lead to inefficiencies in the pyrolysis process, resulting in lower bio-oil yields and increased operational costs. This variability also complicates the design and optimization of pyrolysis reactors, as they must be able to handle a wide range of input materials.
-
Sophisticated Monitoring and Auto-Adjusting Systems:
- Challenge: Effective pyrolysis requires precise control over process parameters such as temperature, heating rate, and residence time. This necessitates the use of sophisticated monitoring and auto-adjusting systems to maintain optimal conditions.
- Impact: The need for advanced control systems increases the complexity and cost of pyrolysis plants. Additionally, these systems must be highly reliable to prevent process deviations that could lead to suboptimal product quality or even equipment damage.
-
Limited Global Adoption:
- Challenge: Despite its potential, pyrolysis technology has seen limited global adoption. This is partly due to the high initial investment costs, lack of standardized regulations, and insufficient awareness of the technology's benefits.
- Impact: Limited adoption slows down the accumulation of operational experience and technological advancements, making it harder to refine and scale up pyrolysis processes. This also limits the availability of trained personnel and specialized equipment, further hindering the technology's growth.
-
Technical Challenges in Reactor Design and Energy Efficiency:
- Challenge: Reducing parasitic energy losses, improving reactor designs, and enhancing feedstock logistics are critical technical challenges. Additionally, increasing the biomass heating rate is essential for improving the efficiency of the pyrolysis process.
- Impact: Inefficient reactor designs and high energy losses can significantly reduce the overall efficiency of the pyrolysis process, leading to higher operational costs and lower profitability. Improving these aspects is crucial for making pyrolysis a more viable and sustainable option.
-
Accumulation of Metal and Ash in Reactor Bed Materials:
- Challenge: The accumulation of metal and ash in reactor bed materials can impede the pyrolysis process and reduce bio-oil yields. These contaminants can also cause wear and tear on reactor components, leading to increased maintenance costs and downtime.
- Impact: The presence of metals and ash can degrade the quality of the bio-oil produced, making it less suitable for further processing or use. This also necessitates more frequent cleaning and maintenance of the reactor, increasing operational costs.
-
Production of Toxic By-Products:
- Challenge: High-temperature pyrolysis can produce many toxic by-products, including dioxins and furans. These by-products pose significant environmental and health risks, requiring careful management and disposal.
- Impact: The production of toxic by-products complicates the pyrolysis process, as additional steps are needed to capture and neutralize these substances. This increases the complexity and cost of the process, making it less attractive for widespread adoption.
-
High Demands on Process Equipment:
- Challenge: The equipment and parameter settings required for recovering useful decomposition products are highly demanding. This includes the need for high-temperature reactors, advanced filtration systems, and precise control mechanisms.
- Impact: The high demands on process equipment increase the capital and operational costs of pyrolysis plants. This makes it more challenging to achieve a favorable return on investment, particularly for smaller-scale operations.
-
Need for Further Research and Development:
- Challenge: Despite its potential, pyrolysis technology still requires further improvement to overcome existing challenges and fully realize its benefits. This includes research into more efficient reactor designs, better feedstock preparation methods, and improved control systems.
- Impact: Ongoing research and development are essential for advancing pyrolysis technology and making it more competitive with other waste management and energy production methods. This will require significant investment and collaboration between industry, academia, and government agencies.
In conclusion, while pyrolysis offers a promising pathway for sustainable waste management and energy production, it faces several significant challenges that must be addressed to achieve its full potential. These challenges include feedstock variability, the need for advanced control systems, technical difficulties in reactor design, and the production of toxic by-products. Overcoming these challenges will require continued research, development, and investment to refine the technology and make it more viable for widespread adoption.
Summary Table:
Challenge | Impact |
---|---|
Variability of Feedstock Materials | Inconsistent quality lowers bio-oil yields and increases operational costs. |
Advanced Monitoring Systems | Increases complexity and cost of pyrolysis plants. |
Limited Global Adoption | Slows technological advancements and availability of trained personnel. |
Reactor Design & Energy Efficiency | High energy losses reduce overall process efficiency. |
Metal & Ash Accumulation | Degrades bio-oil quality and increases maintenance costs. |
Toxic By-Products | Requires additional steps to manage, increasing process complexity. |
High Equipment Demands | Raises capital and operational costs, impacting ROI. |
Need for R&D | Essential for refining technology and improving competitiveness. |
Ready to tackle pyrolysis challenges? Contact our experts today to explore innovative solutions!