Diamond-like carbon (DLC) coatings are a class of amorphous carbon materials that combine the hardness of diamond with the lubricity of graphite. These coatings are characterized by their unique blend of properties, including high hardness, low coefficient of friction, excellent wear resistance, chemical inertness, and biocompatibility. They are widely used in various industries, including automotive, machinery, optical, biomedical, and watchmaking, due to their ability to enhance sliding properties, protect surfaces, and improve performance in harsh environments. DLC coatings can be deposited at relatively low temperatures and are adaptable to a wide range of substrates, making them versatile for numerous applications.
Key Points Explained:
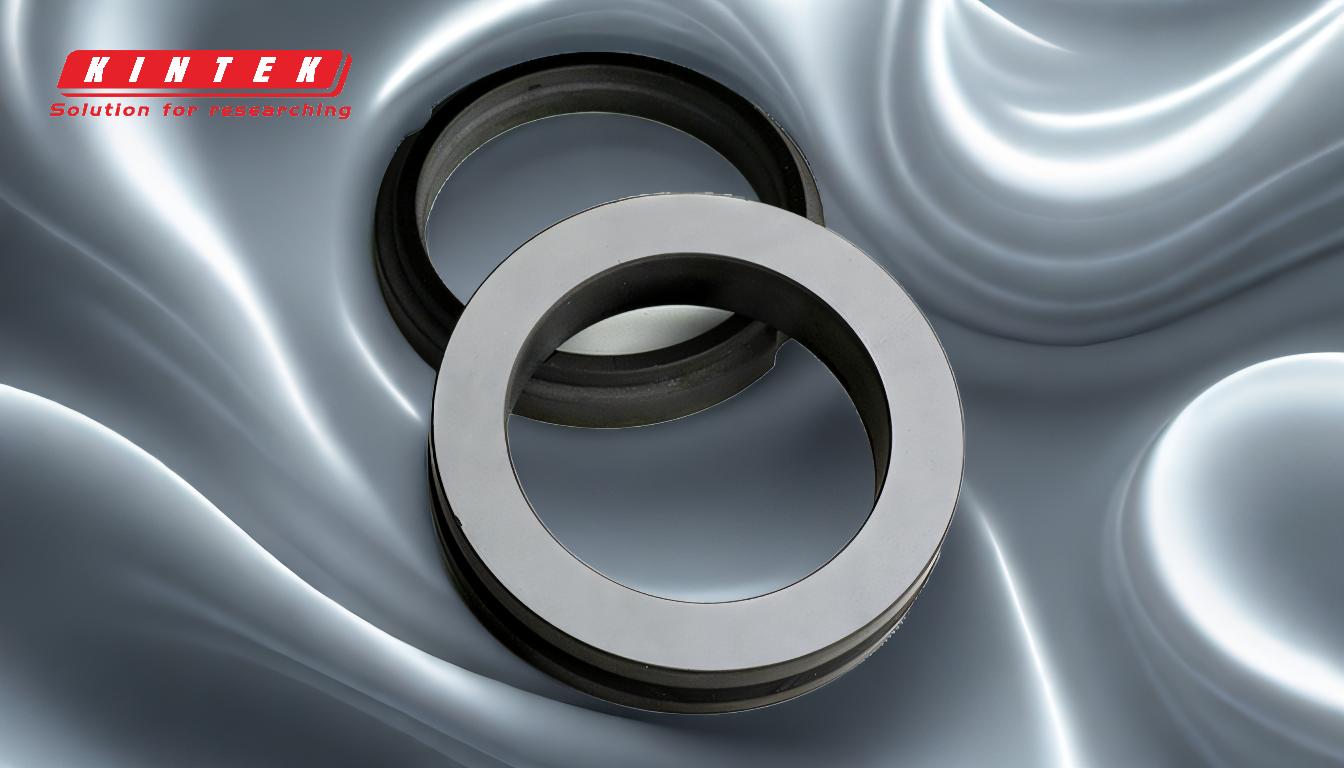
-
Composition and Structure:
- DLC coatings consist of a mixture of Sp3 (diamond-like) and Sp2 (graphite-like) carbon bonds. This hybrid structure gives DLC its unique combination of hardness and lubricity.
- The amorphous nature of DLC means it lacks a crystalline structure, which contributes to its adaptability and uniformity when applied as a coating.
-
High Hardness:
- DLC coatings exhibit high hardness, typically ranging from 1500 to 3000 HV (Vickers hardness). This makes them ideal for wear-protective applications, such as in metalworking tools, bearings, and camshafts.
- The hardness of DLC is comparable to that of diamond, providing excellent resistance to abrasion and wear.
-
Low Coefficient of Friction:
- One of the standout features of DLC coatings is their low coefficient of friction (COF). This property reduces energy loss due to friction, making DLC coatings suitable for energy-saving components in power trains, bearings, and other mechanical systems.
- The low friction also enhances the sliding properties of coated surfaces, extending their lifespan and improving efficiency.
-
Chemical Inertness and Corrosion Resistance:
- DLC coatings are chemically inert, meaning they do not react with most chemicals. This makes them highly resistant to corrosion, even in harsh environments.
- Their resistance to chemicals and corrosive agents makes DLC coatings suitable for use in biomedical prostheses, optical components, and other applications where exposure to aggressive substances is a concern.
-
Biocompatibility:
- DLC coatings are biocompatible, making them suitable for medical applications, such as coatings for biomedical prostheses and implants. Their biocompatibility ensures they do not cause adverse reactions when in contact with human tissues.
-
Surface Smoothness and Adhesion:
- DLC coatings are known for their low surface roughness, which contributes to their effectiveness as protective and passivating coatings. The smooth surface reduces wear and friction, enhancing the performance of coated components.
- Good adhesion is another critical characteristic of DLC coatings. When deposited with adequate bonding layers, such as silicon-based films produced by PACVD (Plasma-Assisted Chemical Vapor Deposition), DLC coatings exhibit strong adhesion to substrates like steel and hard metals.
-
Optical and Antireflective Properties:
- DLC coatings are used in optical sensing applications and as antireflective coatings. Their ability to precisely control thickness and refractive index makes them valuable in optical components, such as lenses and sensors.
- The optical properties of DLC coatings also make them suitable for use in watches, where they enhance functional properties while maintaining a luxurious appearance.
-
Low-Temperature Deposition:
- DLC coatings can be deposited at relatively low temperatures (around 300 °C), which is advantageous for coating temperature-sensitive materials. This low-temperature deposition process, combined with high adhesive strength, makes DLC coatings versatile for a wide range of substrates.
-
Applications Across Industries:
- Automotive and Machinery: DLC coatings are used in power trains, bearings, camshafts, and other components to reduce friction and wear, improving energy efficiency and durability.
- Optical and Biomedical: DLC coatings protect optical components, enhance biocompatibility in medical implants, and serve as antireflective coatings.
- Watchmaking: DLC coatings are applied to watches to enhance durability and maintain a premium aesthetic.
-
Forms of DLC:
- DLC coatings come in various forms, such as ta-C (tetrahedral amorphous carbon), a-C (amorphous carbon), and H-terminated DLC. Each form has specific properties tailored to different applications, such as reducing friction in automotive components or enhancing wear resistance in tools.
In summary, DLC coatings are highly versatile materials with a unique combination of properties that make them suitable for a wide range of applications. Their high hardness, low friction, chemical inertness, biocompatibility, and optical properties make them invaluable in industries ranging from automotive and machinery to biomedical and optical. The ability to deposit DLC coatings at low temperatures and their excellent adhesion to various substrates further enhance their utility and appeal.
Summary Table:
Property | Description |
---|---|
High Hardness | 1500-3000 HV, comparable to diamond, ideal for wear protection. |
Low Coefficient of Friction | Reduces energy loss, enhances sliding properties, and extends component lifespan. |
Chemical Inertness | Resistant to corrosion and chemicals, suitable for harsh environments. |
Biocompatibility | Safe for medical implants and prostheses, no adverse reactions. |
Low Surface Roughness | Smooth surface reduces wear and friction, improving performance. |
Low-Temperature Deposition | Can be applied at ~300°C, ideal for temperature-sensitive materials. |
Applications | Automotive, machinery, optical, biomedical, and watchmaking industries. |
Unlock the potential of DLC coatings for your applications—contact us today to learn more!