Coating methods on carbide inserts are critical for enhancing their performance, durability, and efficiency in machining applications. These methods involve depositing thin layers of materials onto the carbide substrate to improve wear resistance, reduce friction, and increase thermal stability. The most common coating techniques include Chemical Vapor Deposition (CVD), Physical Vapor Deposition (PVD), and hybrid methods that combine both. Each method has its unique advantages, such as CVD providing excellent adhesion and thickness, while PVD offers superior surface finish and precision. Understanding these methods helps in selecting the right coating for specific machining needs, ensuring optimal tool performance and longevity.
Key Points Explained:
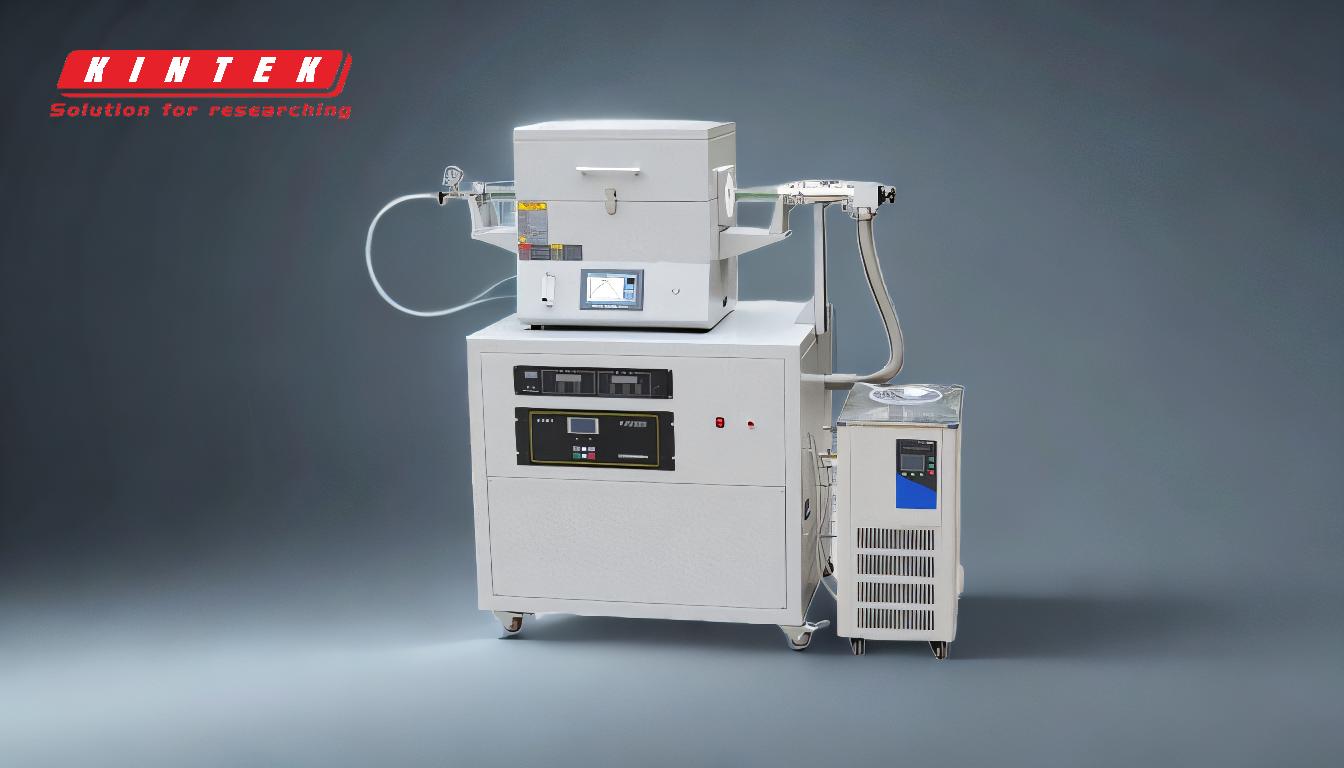
-
Chemical Vapor Deposition (CVD):
- Process: CVD involves the chemical reaction of gaseous precursors at high temperatures (800–1000°C) to deposit a solid coating on the carbide insert. Common coatings include titanium nitride (TiN), titanium carbonitride (TiCN), and aluminum oxide (Al₂O₃).
-
Advantages:
- Excellent adhesion to the substrate.
- Ability to deposit thick, uniform coatings (5–15 µm).
- High thermal stability, making it suitable for high-speed machining.
- Applications: Ideal for roughing and semi-finishing operations where high wear resistance is required.
-
Physical Vapor Deposition (PVD):
- Process: PVD involves the physical transfer of material from a target to the carbide insert in a vacuum environment. Techniques include sputtering and arc evaporation, with coatings like titanium aluminum nitride (TiAlN) and chromium nitride (CrN).
-
Advantages:
- Produces thinner coatings (2–5 µm) with a smooth surface finish.
- Lower deposition temperatures (200–500°C), reducing the risk of substrate deformation.
- Enhanced edge sharpness and precision, suitable for finishing operations.
- Applications: Preferred for precision machining, where surface finish and dimensional accuracy are critical.
-
Hybrid Coating Methods:
- Process: Hybrid methods combine CVD and PVD to leverage the strengths of both techniques. For example, a CVD layer may be applied first for wear resistance, followed by a PVD layer for improved surface finish.
-
Advantages:
- Combines the thickness and adhesion of CVD with the precision and smoothness of PVD.
- Offers versatility for a wide range of machining applications.
- Applications: Used in complex machining tasks requiring both durability and high precision.
-
Selection Criteria for Coating Methods:
- Machining Conditions: Consider factors like cutting speed, feed rate, and workpiece material. CVD is better for high-speed, high-temperature operations, while PVD is suited for fine finishing.
- Coating Properties: Evaluate wear resistance, thermal stability, and friction reduction based on the application.
- Cost and Efficiency: Balance the cost of coating with the expected tool life and performance improvements.
-
Emerging Trends in Coating Technologies:
- Nanostructured Coatings: These coatings, such as nanocomposite TiAlN, offer superior hardness and thermal stability, improving tool life in demanding applications.
- Multilayer Coatings: Alternating layers of different materials (e.g., TiN/TiCN) enhance toughness and wear resistance.
- Adaptive Coatings: Designed to respond to machining conditions, these coatings can self-adjust to optimize performance.
By understanding these coating methods and their applications, purchasers can make informed decisions to select the most suitable carbide inserts for their specific machining needs, ensuring enhanced productivity and cost-effectiveness.
Summary Table:
Coating Method | Process | Advantages | Applications |
---|---|---|---|
CVD | Chemical reaction of gaseous precursors at 800–1000°C | Excellent adhesion, thick coatings (5–15 µm), high thermal stability | Roughing, semi-finishing |
PVD | Physical transfer in vacuum at 200–500°C | Thin coatings (2–5 µm), smooth finish, enhanced precision | Precision machining, finishing |
Hybrid | Combines CVD and PVD | Thickness of CVD, smoothness of PVD, versatile | Complex machining tasks |
Ready to optimize your machining tools? Contact our experts today to find the perfect coating solution for your carbide inserts!