A rotary kiln is a complex piece of equipment used in various industrial processes, such as cement production, lime calcination, and chemical processing. It consists of several key components that work together to facilitate the high-temperature treatment of materials. The primary components include the kiln shell, refractory lining, support tyres (riding rings) and rollers, drive gear, and internal heat exchangers. Each component plays a critical role in ensuring the kiln operates efficiently and withstands the high temperatures and mechanical stresses encountered during operation.
Key Points Explained:
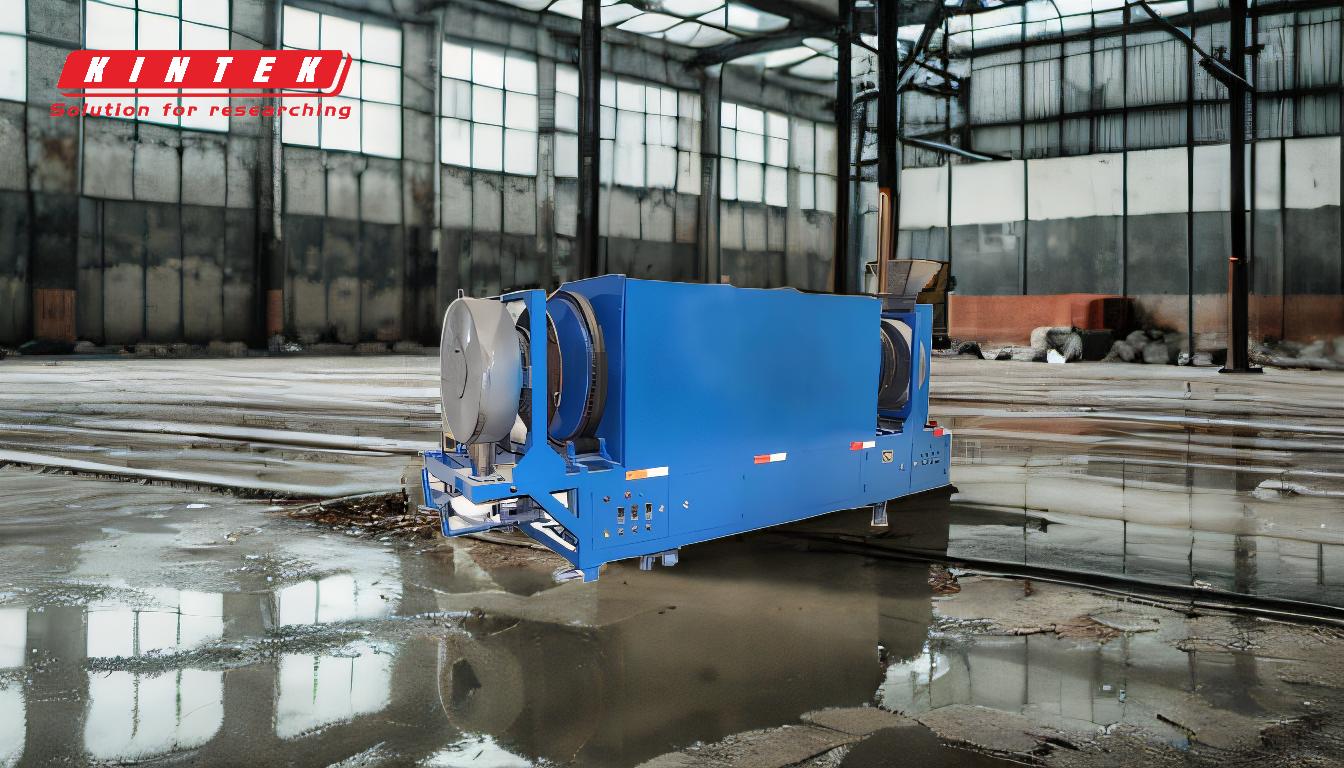
-
Kiln Shell:
- The kiln shell is the outer cylindrical structure of the rotary kiln, typically made of steel. It is conically tapered at the ends to facilitate the movement of materials through the kiln.
- The shell experiences significant mechanical stresses, including torsion and flexural stress, due to the rotation and the weight of the materials inside.
- The shell must be robust and durable to withstand these stresses and the high temperatures generated during operation.
-
Refractory Lining:
- The refractory lining is a layer of heat-resistant material applied to the inner surface of the kiln shell. It protects the shell from the extreme temperatures inside the kiln and helps to retain heat.
- The lining is made from refractory materials that do not melt at high temperatures, ensuring the kiln can operate efficiently without damage to the shell.
- The choice of refractory material depends on the specific application and the temperatures involved.
-
Support Tyres (Riding Rings) and Rollers:
- Support tyres, also known as riding rings, are large, heavy-duty rings that encircle the kiln shell and rest on rollers. These components support the weight of the kiln and allow it to rotate smoothly.
- The rollers are mounted on a fixed base and are designed to bear the load of the kiln while minimizing friction during rotation.
- Proper alignment and maintenance of the support tyres and rollers are crucial for the smooth operation of the kiln and to prevent excessive wear and tear.
-
Drive Gear:
- The drive gear is responsible for rotating the kiln. It can be powered by various drive assemblies, including chain and sprocket drives, gear drives, friction drives, or direct drive assemblies.
- The drive gear must provide consistent and reliable rotation to ensure the materials inside the kiln are evenly heated and processed.
- The choice of drive assembly depends on the size and capacity of the kiln, as well as the specific requirements of the process.
-
Internal Heat Exchangers:
- Internal heat exchangers are components within the kiln that facilitate the transfer of heat to the materials being processed. They help to optimize the thermal efficiency of the kiln.
- Heat exchangers can take various forms, such as tubes or plates, and are designed to maximize the surface area for heat transfer.
- Efficient heat exchangers are essential for reducing energy consumption and ensuring uniform heating of the materials.
-
Kiln Body and Electrical Control Box (for Lab Rotary Kilns):
- In lab-scale rotary kilns, the kiln body is divided into the electric furnace body and the power rotation system. The furnace body typically uses an alumina fiber furnace for insulation and heat retention.
- The power rotation system includes a motor, reduction gearbox, transmission shaft, and chain to rotate the furnace tube. The motor and reduction box are usually placed under the furnace body to maintain a compact structure.
- The tilt of the furnace body is controlled by a hydraulic device operated with a hand wheel, allowing for precise control over the angle of the kiln.
-
Material Feed and Outlet Housings:
- The rotary kiln is mounted between stationary material feed and outlet housings. These housings facilitate the continuous feeding of raw materials into the kiln and the discharge of processed materials.
- The design of the feed and outlet housings must ensure a smooth flow of materials and prevent any blockages or leaks.
- Proper sealing of these housings is essential to maintain the internal environment of the kiln and prevent heat loss.
In summary, the components of a rotary kiln are designed to work together to provide efficient and reliable high-temperature processing of materials. Each component, from the kiln shell to the drive gear, plays a vital role in ensuring the kiln operates smoothly and withstands the harsh conditions of industrial processes. Understanding these components is crucial for anyone involved in the design, operation, or maintenance of rotary kilns.
Summary Table:
Component | Function | Key Features |
---|---|---|
Kiln Shell | Outer cylindrical structure made of steel | Conically tapered ends, withstands mechanical stress and high temperatures |
Refractory Lining | Heat-resistant layer inside the shell | Protects shell, retains heat, made of durable refractory materials |
Support Tyres & Rollers | Supports kiln weight and enables smooth rotation | Heavy-duty rings, rollers minimize friction, require proper alignment |
Drive Gear | Rotates the kiln | Powered by chain, gear, or friction drives, ensures consistent rotation |
Internal Heat Exchangers | Facilitates heat transfer to materials | Optimizes thermal efficiency, reduces energy consumption |
Kiln Body & Control Box | Lab-scale kiln components (electric furnace body, power rotation system) | Alumina fiber insulation, hydraulic tilt control, compact design |
Feed & Outlet Housings | Facilitates material flow into and out of the kiln | Prevents blockages, ensures proper sealing to maintain internal environment |
Need a rotary kiln tailored to your industrial needs? Contact our experts today for a customized solution!