Chemical Vapor Deposition (CVD) is a versatile and widely used technique for depositing thin films and coatings on substrates. It involves a series of steps where gaseous reactants are transported to a substrate, undergo chemical reactions, and form a solid film. The process is highly controlled and can produce high-quality materials with specific properties. Below is a detailed explanation of the components and steps involved in CVD.
Key Points Explained:
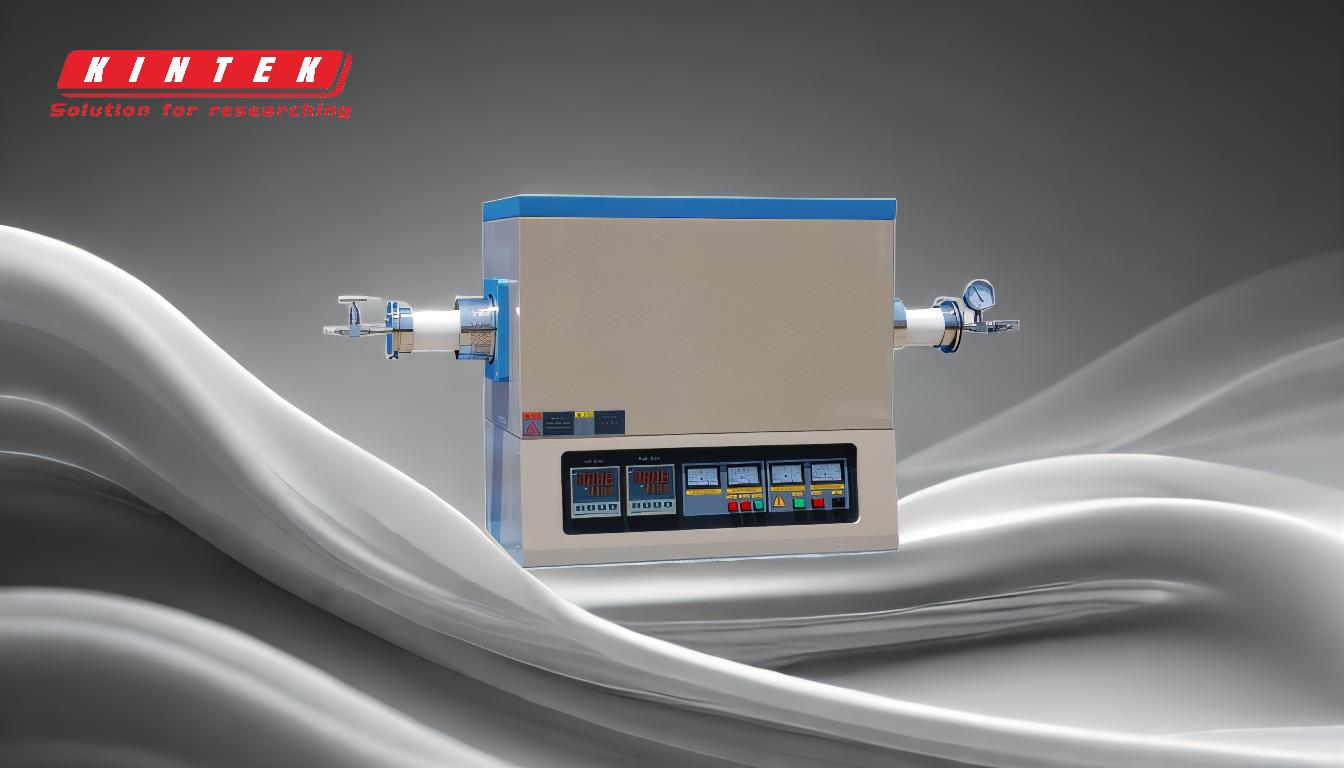
-
Transport of Reactants to the Reaction Chamber:
- The first step in CVD involves the transportation of gaseous reactants into the reaction chamber. This can occur through convection or diffusion. The reactants are typically volatile compounds that can easily vaporize and be carried into the chamber by a carrier gas.
-
Chemical and Gas Phase Reactions:
- Once inside the chamber, the reactants undergo chemical reactions in the gas phase. These reactions can produce reactive species and by-products. The nature of these reactions depends on the specific CVD method being used, such as pyrolysis, chemical transport, or synthesis reactions.
-
Transport Through the Boundary Layer:
- The reactive species must then travel through a boundary layer to reach the substrate surface. The boundary layer is a thin layer of gas adjacent to the substrate where the flow velocity changes from zero (at the substrate surface) to the free stream velocity.
-
Adsorption on the Substrate Surface:
- Upon reaching the substrate, the reactive species adsorb onto the surface. This can involve both physical adsorption (physisorption) and chemical adsorption (chemisorption), where the species form weak or strong bonds with the substrate, respectively.
-
Heterogeneous Surface Reactions:
- The adsorbed species undergo heterogeneous surface reactions, leading to the formation of a solid film. These reactions are catalyzed by the substrate surface and result in the deposition of the desired material.
-
Desorption of By-products:
- Volatile by-products formed during the surface reactions desorb from the substrate and diffuse back through the boundary layer into the main gas stream. These by-products are then carried out of the reaction chamber.
-
Removal of Gaseous By-products:
- The final step involves the removal of gaseous by-products from the reactor. This is typically achieved through convection and diffusion processes, ensuring that the reaction chamber remains clean for subsequent deposition cycles.
-
Control Parameters:
- Several parameters control the CVD process, including chamber pressure, substrate temperature, and the nature of the target materials. These parameters influence the rate and quality of the deposition. For example, higher temperatures can increase the rate of chemical reactions, while lower pressures can reduce unwanted gas-phase reactions.
-
Types of CVD:
- There are various types of CVD methods, each suited for different applications. These include:
- Atmospheric Pressure Chemical Vapor Deposition (APCVD): Operates at atmospheric pressure, suitable for large-scale production.
- Low-Pressure Chemical Vapor Deposition (LPCVD): Operates at reduced pressures, providing better control over film thickness and uniformity.
- Plasma-Enhanced Chemical Vapor Deposition (PECVD): Uses plasma to enhance chemical reactions, allowing deposition at lower temperatures.
- Atomic Layer Deposition (ALD): A variant of CVD that allows for precise control over film thickness at the atomic level.
- There are various types of CVD methods, each suited for different applications. These include:
-
Applications of CVD:
- CVD is used in a wide range of applications, including the fabrication of semiconductor devices, optical coatings, protective coatings, and advanced materials like graphene. It is valued for its ability to produce high-purity, high-quality films with excellent adhesion and uniformity.
In summary, Chemical Vapor Deposition is a complex but highly effective process for depositing thin films and coatings. It involves multiple steps, from the transport of reactants to the desorption of by-products, each controlled by specific parameters to achieve the desired material properties. The versatility and precision of CVD make it an essential technique in modern materials science and engineering.
Summary Table:
Step | Description |
---|---|
Transport of Reactants | Gaseous reactants are transported into the reaction chamber via convection or diffusion. |
Chemical and Gas Phase Reactions | Reactants undergo gas-phase reactions, producing reactive species and by-products. |
Transport Through Boundary Layer | Reactive species travel through a boundary layer to reach the substrate surface. |
Adsorption on Substrate Surface | Reactive species adsorb onto the substrate via physisorption or chemisorption. |
Heterogeneous Surface Reactions | Adsorbed species undergo surface reactions, forming a solid film. |
Desorption of By-products | Volatile by-products desorb and diffuse back into the gas stream. |
Removal of Gaseous By-products | By-products are removed from the reactor via convection and diffusion. |
Control Parameters | Parameters like pressure, temperature, and target materials influence deposition. |
Types of CVD | Includes APCVD, LPCVD, PECVD, and ALD, each suited for specific applications. |
Applications | Used in semiconductors, optical coatings, protective coatings, and advanced materials. |
Discover how CVD can enhance your material science projects—contact our experts today for tailored solutions!