Sintering is a critical process in the production of zirconia, where heat is used to fuse materials into a solid mass without reaching a liquid state. This process significantly impacts the mechanical strength and overall quality of the final product. The conditions for sintering, particularly in a zirconia sintering furnace, involve precise control of temperature, pressure, and atmosphere. Temperature control is especially crucial as it influences grain boundary diffusion and bulk diffusion, which are dependent on factors like particle size, material distribution, composition, and the sintering environment. Advanced sintering furnaces, such as those used in dental applications, feature high-precision controllers, efficient heating elements, and optimized air circulation systems to ensure uniform heat distribution, maintain oxygen levels, and achieve the desired color and surface finish of the sintered zirconia.
Key Points Explained:
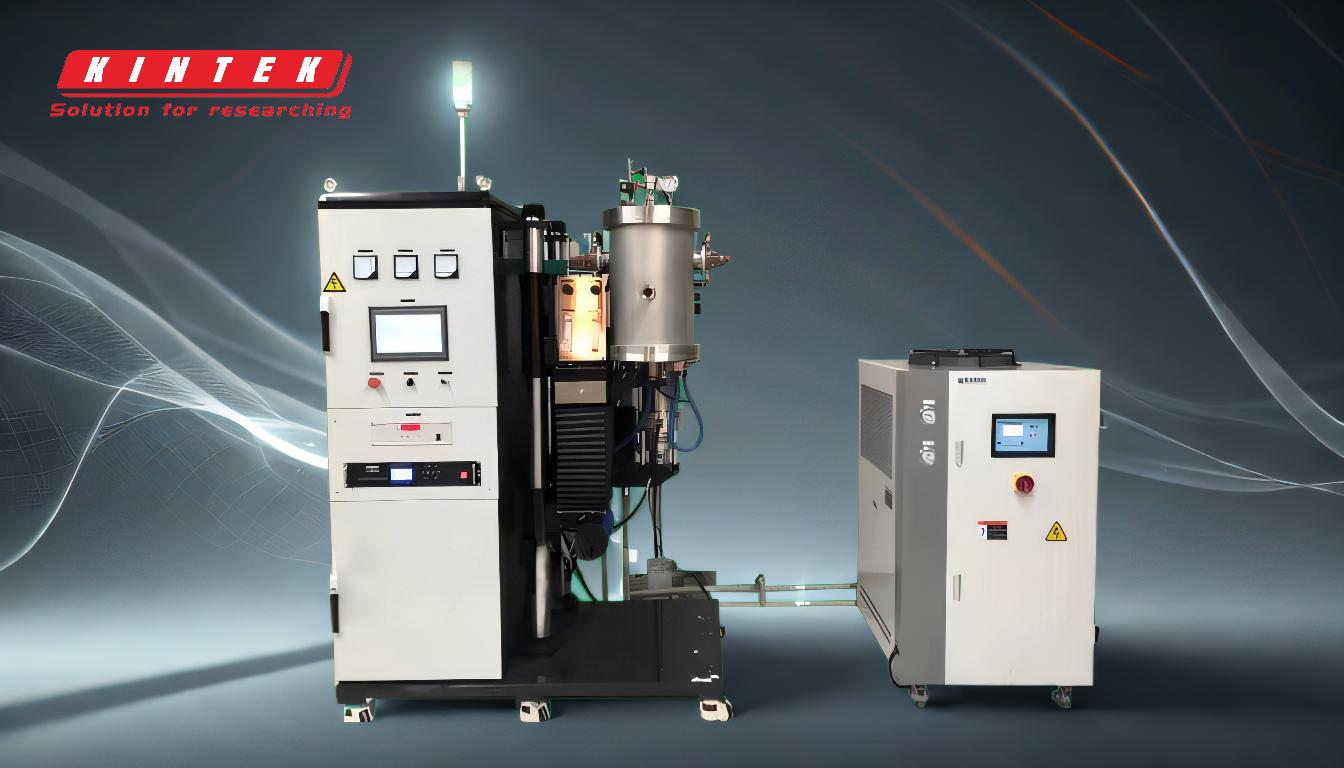
-
Temperature Control:
- Temperature is the most critical factor in sintering. It directly affects grain boundary diffusion and bulk diffusion, which are essential for achieving a dense and strong final product.
- Modern sintering furnaces, like the zirconia sintering furnace, use PID intelligent temperature control systems to maintain precise temperatures with an accuracy of ±1℃.
- AI-based controllers are also employed to ensure consistent temperatures across all zones of the furnace, improving efficiency and reducing energy consumption.
-
Heating Elements and Heat Distribution:
- High-purity and pollution-free dental silicon molybdenum rods are commonly used in sintering furnaces to provide even heat distribution.
- Advanced heating elements ensure that heat is uniformly transferred to the surface of the zirconia and conducted to its core, resulting in a dense and mechanically strong product.
-
Sintering Phases:
- The sintering process typically consists of three phases: heating, sintering, and cooling.
- In the heating phase, the material is gradually brought up to the required temperature.
- During the sintering phase, the material is held at a specific temperature to allow diffusion and bonding of particles.
- The cooling phase is equally important, as rapid or uneven cooling can lead to defects in the final product.
-
Atmosphere Control:
- The sintering environment, including oxygen levels, must be carefully controlled to achieve the desired color and surface finish of the zirconia.
- Efficient air circulation systems in sintering furnaces help maintain optimal oxygen levels and prevent contamination.
-
Programmability and Automation:
- Modern sintering furnaces can store multiple programs (e.g., up to 40 programs) and feature user-friendly interfaces, such as 7-inch color touch screens, for easy parameter modification.
- Memory functions allow the furnace to resume operations from the point of interruption in case of power outages, ensuring consistency in the sintering process.
-
Efficiency and Capacity:
- Some sintering furnaces offer fast sintering programs that complete the process in as little as 65 minutes, including heating, keeping warm, and cooling.
- These furnaces can handle large volumes, such as stacking three layers of crucibles and sintering up to 150 units in a single run.
-
Environmental Considerations:
- Green, environmentally friendly thermal insulation materials are used in sintering furnaces to provide stable temperatures and reduce energy consumption.
- These materials also contribute to the overall sustainability of the sintering process.
By carefully controlling these conditions, sintering furnaces ensure the production of high-quality zirconia with the desired mechanical properties, surface finish, and color.
Summary Table:
Key Condition | Description |
---|---|
Temperature Control | Precise control (±1℃) using PID and AI systems for uniform heat distribution. |
Heating Elements | High-purity silicon molybdenum rods ensure even heat transfer. |
Sintering Phases | Heating, sintering, and cooling phases are carefully managed to avoid defects. |
Atmosphere Control | Controlled oxygen levels and air circulation for desired color and finish. |
Programmability | Up to 40 programs with 7-inch touch screens for easy parameter modification. |
Efficiency | Fast sintering programs (65 minutes) and high capacity (150 units per run). |
Environmental Impact | Green insulation materials reduce energy consumption and enhance sustainability. |
Ready to optimize your sintering process? Contact our experts today for tailored solutions!