Mould design is a critical aspect of manufacturing, particularly in industries like injection moulding, casting, and plastic production. It involves creating a precise and functional mould that can produce high-quality parts efficiently. Key considerations include material selection, part geometry, cooling systems, and manufacturability. A well-designed mould ensures durability, cost-effectiveness, and consistency in production. Below, we explore the essential factors to consider when designing a mould, ensuring it meets both functional and economic requirements.
Key Points Explained:
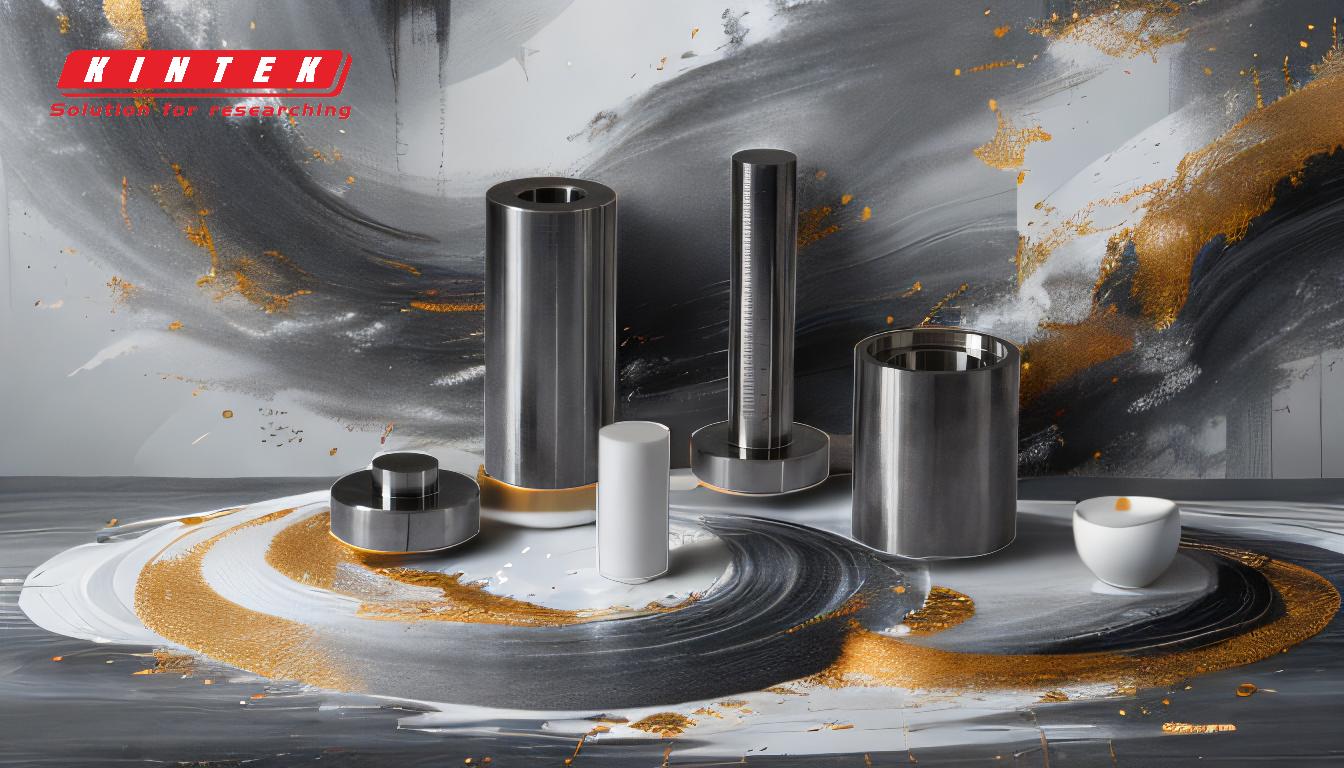
-
Material Selection
- The choice of material for the mould is crucial as it directly impacts durability, thermal conductivity, and cost. Common materials include steel, aluminum, and beryllium-copper alloys.
- Steel is often preferred for high-volume production due to its durability and resistance to wear. Aluminum, on the other hand, is lighter and offers better thermal conductivity, making it suitable for prototypes or low-volume production.
- The material must also resist corrosion and thermal fatigue, especially in high-temperature applications like injection moulding.
-
Part Geometry and Design
- The mould design must account for the geometry of the final part, including features like undercuts, ribs, and bosses.
- Draft angles are essential to facilitate easy ejection of the part from the mould. Typically, a draft angle of 1-2 degrees is recommended, though this may vary depending on the material and part complexity.
- Wall thickness uniformity is critical to avoid defects like warping, sink marks, or voids. Uneven thickness can lead to inconsistent cooling and stress concentrations.
-
Cooling System Design
- Efficient cooling is vital for maintaining cycle times and ensuring part quality. The cooling system must be designed to remove heat uniformly from the mould.
- Cooling channels should be strategically placed to avoid hot spots and ensure even cooling. Computational fluid dynamics (CFD) simulations can help optimize channel placement.
- The choice of coolant (water, oil, or air) depends on the mould material and the thermal requirements of the process.
-
Ejection System
- The ejection system must be designed to remove the part from the mould without causing damage. Common ejection methods include ejector pins, sleeves, and air blasts.
- The placement and size of ejector pins must be carefully planned to avoid marking or distorting the part.
- For complex parts, additional mechanisms like lifters or slides may be required to release undercuts.
-
Gating and Runner Systems
- The gate is the entry point for the material into the mould cavity. Its design affects the flow of material, filling time, and part quality.
- Runner systems distribute the material to multiple cavities in multi-cavity moulds. Balanced runners ensure uniform filling and reduce waste.
- Gate location should minimize weld lines and air traps, which can weaken the part or create surface defects.
-
Venting
- Proper venting is necessary to allow air and gases to escape during the moulding process. Inadequate venting can cause defects like burns, voids, or incomplete filling.
- Venting channels should be placed at the end of the flow path and designed to prevent material leakage.
- The size and depth of vents depend on the material viscosity and flow characteristics.
-
Manufacturability and Maintenance
- The mould design should simplify manufacturing and assembly processes. Complex designs may increase production costs and lead to longer lead times.
- Consideration should be given to ease of maintenance, such as accessibility for cleaning, repairs, and part replacement.
- Modular designs can reduce downtime and allow for quick modifications or upgrades.
-
Cost Considerations
- The design must balance performance and cost. High-quality materials and complex features can increase the initial investment but may reduce long-term costs through improved durability and efficiency.
- Design for manufacturability (DFM) principles should be applied to minimize waste and optimize production processes.
- Prototyping and testing can help identify potential issues early, reducing the risk of costly redesigns.
-
Surface Finish and Texture
- The surface finish of the mould affects the appearance and functionality of the final part. Textures can be added to the mould to achieve specific aesthetic or functional requirements.
- Polishing or coating the mould surface can improve part release and reduce wear.
- The choice of surface finish depends on the application, with options ranging from mirror finishes to rough textures.
-
Tolerance and Precision
- Moulds must be designed to meet tight tolerances, ensuring consistent part dimensions and quality.
- Precision machining techniques, such as CNC milling and EDM (electrical discharge machining), are often used to achieve the required accuracy.
- Tolerance considerations should account for material shrinkage, thermal expansion, and other factors that may affect part dimensions.
-
Environmental and Safety Considerations
- The mould design should minimize environmental impact by reducing material waste and energy consumption.
- Safety features, such as interlocks and guards, should be incorporated to protect operators during mould operation and maintenance.
- Compliance with industry standards and regulations is essential to ensure safe and sustainable production.
By addressing these considerations, mould designers can create efficient, durable, and cost-effective moulds that meet the demands of modern manufacturing. Each factor plays a critical role in ensuring the success of the moulding process, from initial design to final production.
Summary Table:
Key Consideration | Details |
---|---|
Material Selection | Steel for durability, aluminum for thermal conductivity, corrosion resistance. |
Part Geometry | Draft angles, wall thickness uniformity, and feature complexity. |
Cooling System | Uniform cooling, strategic channel placement, and coolant selection. |
Ejection System | Ejector pins, sleeves, and mechanisms for complex parts. |
Gating and Runner Systems | Gate design, balanced runners, and minimizing weld lines. |
Venting | Proper venting to prevent defects like burns and voids. |
Manufacturability | Simplified design, modularity, and ease of maintenance. |
Cost Considerations | Balancing performance and cost, applying DFM principles. |
Surface Finish | Textures, polishing, and coatings for part release and aesthetics. |
Tolerance and Precision | Tight tolerances, precision machining, and accounting for material shrinkage. |
Environmental & Safety | Reducing waste, energy efficiency, and compliance with safety standards. |
Ready to design a mould that meets your production needs? Contact our experts today for personalized guidance!