Pyrolysis is a thermal decomposition process that occurs in the absence of oxygen, leading to the breakdown of organic materials into smaller molecules, gases, and solid residues. During this process, contaminants can be introduced or formed, which may affect the quality of the end products and pose environmental or health risks. These contaminants can originate from the feedstock, the pyrolysis process itself, or external sources. Understanding these contaminants is crucial for optimizing pyrolysis processes, ensuring product quality, and mitigating environmental impacts.
Key Points Explained:
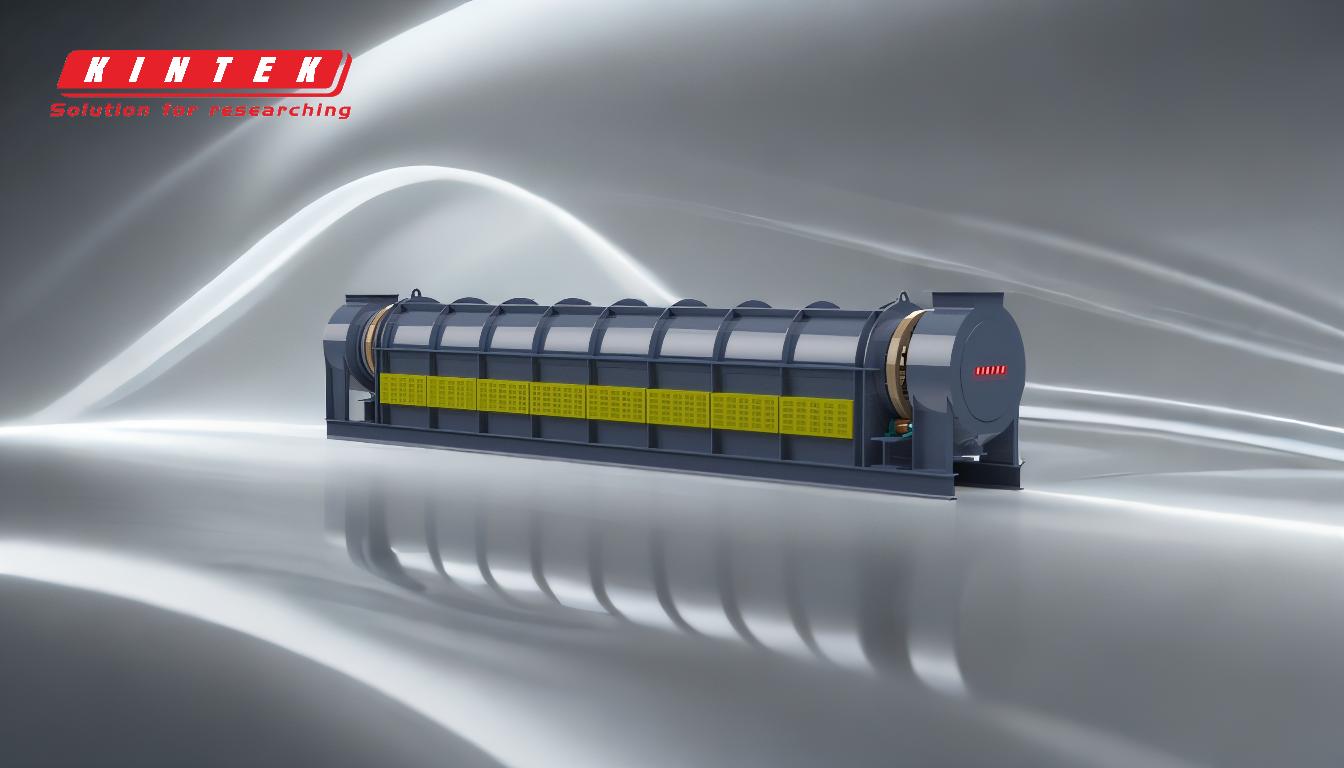
-
Contaminants from Feedstock
- Feedstock impurities: The raw materials used in pyrolysis, such as biomass, plastics, or waste, often contain impurities like heavy metals, chlorine, sulfur, and nitrogen compounds. These impurities can carry over into the pyrolysis products.
- Moisture content: High moisture in feedstock can lead to the formation of water vapor during pyrolysis, which may dilute the pyrolysis gases and reduce their calorific value.
- Inorganic matter: Ash and other inorganic materials in the feedstock can remain as solid residues (char) or contribute to the formation of particulate matter in the gas phase.
-
Process-Induced Contaminants
- Tar formation: One of the most significant byproducts of pyrolysis is tar, a complex mixture of hydrocarbons. Tar can condense in downstream equipment, causing blockages and reducing efficiency.
- Polycyclic aromatic hydrocarbons (PAHs): These are formed during the pyrolysis of organic materials, especially at high temperatures, and are known for their carcinogenic properties.
- Particulate matter: Fine particles can be generated during pyrolysis, particularly if the feedstock contains ash or if the process conditions are not optimized.
-
External Contaminants
- Airborne pollutants: If the pyrolysis process is not fully sealed, external contaminants like dust or pollutants from the surrounding environment can enter the system.
- Process gases: Incomplete pyrolysis or improper gas handling can lead to the release of harmful gases such as carbon monoxide, methane, and volatile organic compounds (VOCs).
-
Environmental and Health Impacts
- Air pollution: Contaminants like PAHs, particulate matter, and VOCs can contribute to air pollution if not properly managed.
- Soil and water contamination: Improper disposal of pyrolysis residues (char or ash) can lead to the leaching of heavy metals and other harmful substances into the environment.
- Occupational hazards: Workers involved in pyrolysis processes may be exposed to harmful contaminants, necessitating proper safety measures.
-
Mitigation Strategies
- Feedstock pre-treatment: Cleaning and drying the feedstock can reduce impurities and moisture content, improving pyrolysis efficiency and reducing contaminants.
- Process optimization: Adjusting temperature, heating rate, and residence time can minimize the formation of undesirable byproducts like tar and PAHs.
- Gas cleaning systems: Installing filters, scrubbers, and condensers can help remove particulate matter, tar, and harmful gases from the pyrolysis gas stream.
- Proper waste management: Ensuring safe disposal or utilization of pyrolysis residues can prevent environmental contamination.
By addressing these contaminants through careful feedstock selection, process optimization, and effective mitigation strategies, the pyrolysis process can be made more efficient, environmentally friendly, and safe for both operators and the surrounding ecosystem.
Summary Table:
Source of Contaminants | Examples | Impact |
---|---|---|
Feedstock Impurities | Heavy metals, chlorine, sulfur | Carry over into pyrolysis products |
Process-Induced Contaminants | Tar, PAHs, particulate matter | Equipment blockages, carcinogenic risks |
External Contaminants | Airborne pollutants, process gases | Air pollution, health hazards |
Environmental & Health Impacts | Air, soil, water contamination | Environmental degradation, occupational risks |
Mitigation Strategies | Feedstock pre-treatment, process optimization | Improved efficiency, reduced risks |
Ready to optimize your pyrolysis process? Contact our experts today for tailored solutions!