Chemical vapor deposition (CVD) is a versatile and widely used technique in nanotechnology for depositing thin films and coatings. It involves the vaporization of a precursor material, which then decomposes and reacts on a substrate to form a thin film. CVD offers numerous advantages, such as the ability to produce high-purity materials, control over film properties, and the capability to deposit complex materials at relatively low temperatures. In nanotechnology, different types of CVD processes are employed depending on the specific application and desired film characteristics. These variations include Atmospheric Pressure CVD (APCVD), Low-Pressure CVD (LPCVD), Plasma-Enhanced CVD (PECVD), Metal-Organic CVD (MOCVD), and Atomic Layer Deposition (ALD), among others. Each type has unique mechanisms and is suited for specific applications in nanotechnology.
Key Points Explained:
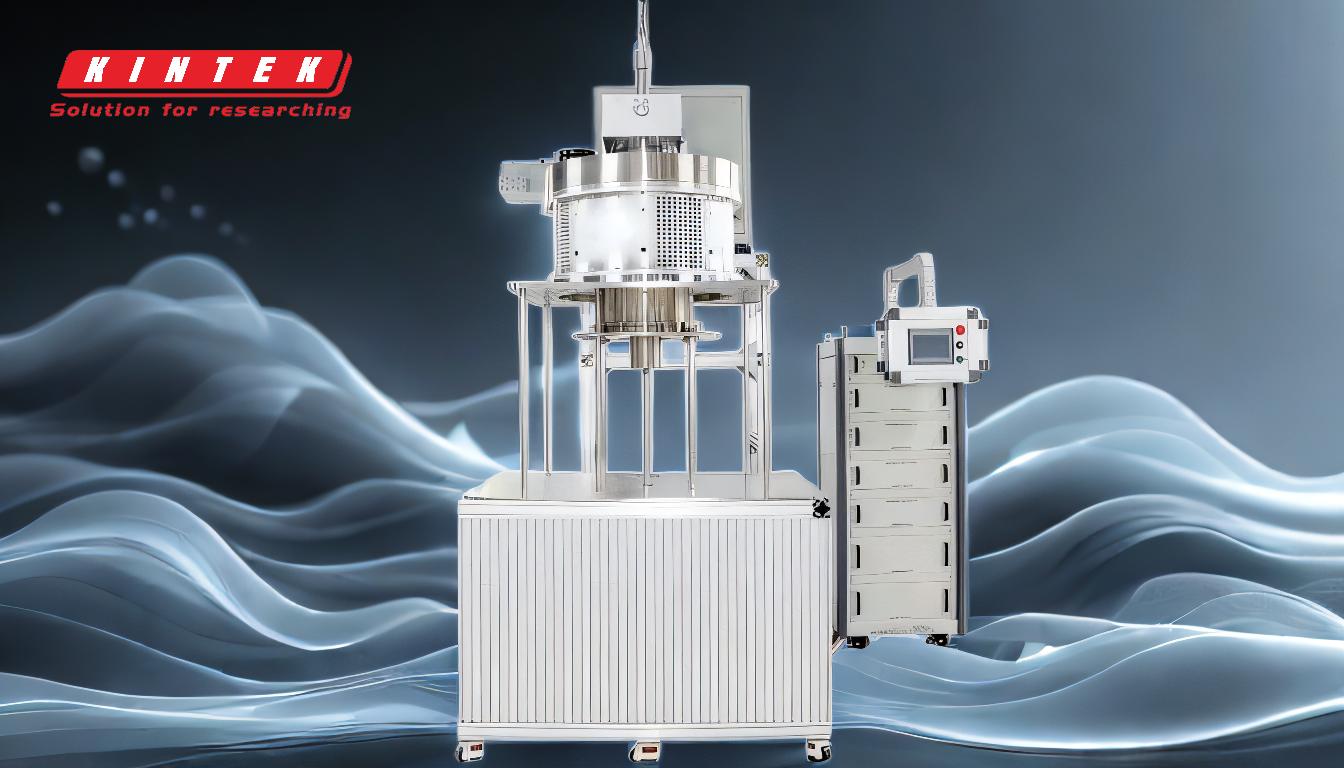
-
Atmospheric Pressure CVD (APCVD):
- APCVD is conducted at atmospheric pressure, making it one of the simplest and most cost-effective CVD methods.
- It is typically used for depositing oxides, nitrides, and other materials at relatively high temperatures.
- The process is straightforward but may result in lower film uniformity compared to other CVD methods due to the lack of pressure control.
-
Low-Pressure CVD (LPCVD):
- LPCVD operates at reduced pressures, which enhances film uniformity and allows for better control over the deposition process.
- This method is commonly used for depositing polysilicon, silicon nitride, and silicon dioxide in semiconductor manufacturing.
- The lower pressure reduces gas-phase reactions, leading to higher-quality films with fewer defects.
-
Plasma-Enhanced CVD (PECVD):
- PECVD utilizes plasma to provide the energy needed for the chemical reactions, allowing deposition to occur at lower temperatures compared to thermal CVD methods.
- This method is ideal for depositing thin films on temperature-sensitive substrates, such as polymers or certain metals.
- PECVD is widely used in the production of solar cells, microelectronics, and optical coatings.
-
Metal-Organic CVD (MOCVD):
- MOCVD employs metal-organic compounds as precursors, enabling the deposition of complex materials such as III-V semiconductors (e.g., gallium nitride, indium phosphide).
- This method is essential for the fabrication of optoelectronic devices, including LEDs and laser diodes.
- MOCVD allows for precise control over the composition and thickness of the deposited films, making it highly suitable for nanotechnology applications.
-
Atomic Layer Deposition (ALD):
- ALD is a specialized form of CVD that deposits materials one atomic layer at a time, offering exceptional control over film thickness and uniformity.
- This method is used for depositing ultra-thin films in applications such as nanoelectronics, MEMS, and protective coatings.
- ALD is particularly valuable in nanotechnology due to its ability to produce conformal coatings on complex 3D structures.
-
Advantages of CVD in Nanotechnology:
- High Purity: CVD can produce films with high purity, which is critical for applications in semiconductors and optoelectronics.
- Versatility: The ability to deposit a wide range of materials, including metals, ceramics, and polymers, makes CVD highly versatile.
- Control Over Properties: By adjusting parameters such as temperature, pressure, and gas flow, the chemical and physical properties of the films can be tailored to specific needs.
- Scalability: CVD processes can be scaled up for industrial production, making them suitable for large-scale manufacturing of nanomaterials.
-
Applications of CVD in Nanotechnology:
- Semiconductors: CVD is extensively used in the fabrication of semiconductor devices, including transistors, diodes, and integrated circuits.
- Optoelectronics: The deposition of materials like gallium nitride and indium phosphide using MOCVD is crucial for the production of LEDs and laser diodes.
- Energy Storage: CVD is employed in the development of thin-film batteries and supercapacitors, which are essential for portable electronics and electric vehicles.
- Protective Coatings: CVD is used to deposit wear-resistant and corrosion-resistant coatings on various substrates, enhancing their durability and performance.
In conclusion, the different types of CVD processes play a crucial role in nanotechnology, enabling the deposition of high-quality thin films with precise control over their properties. Each CVD method has its unique advantages and is suited for specific applications, making CVD an indispensable tool in the advancement of nanotechnology.
Summary Table:
Type of CVD | Key Characteristics | Applications |
---|---|---|
APCVD | Conducted at atmospheric pressure; cost-effective; lower film uniformity | Depositing oxides, nitrides, and other materials at high temperatures |
LPCVD | Operates at reduced pressures; enhances film uniformity; fewer defects | Semiconductor manufacturing (polysilicon, silicon nitride, silicon dioxide) |
PECVD | Uses plasma for energy; lower-temperature deposition | Solar cells, microelectronics, optical coatings |
MOCVD | Uses metal-organic precursors; precise control over film composition and thickness | Optoelectronics (LEDs, laser diodes) |
ALD | Deposits materials one atomic layer at a time; exceptional control over film thickness | Nanoelectronics, MEMS, protective coatings |
Interested in leveraging CVD for your nanotechnology projects? Contact our experts today to learn more!