Graphene exfoliation is a critical process in the production of high-quality graphene, and it can be achieved through several methods, each with its own advantages and limitations. The primary techniques include mechanical exfoliation, liquid-phase exfoliation, and chemical vapor deposition (CVD). Mechanical exfoliation, often referred to as the "Scotch tape method," is a simple and effective way to produce high-quality graphene flakes, but it is not scalable for industrial applications. Liquid-phase exfoliation, on the other hand, involves dispersing graphite in a solvent and applying energy, such as ultrasonic waves, to separate the layers. This method is more scalable but often results in lower-quality graphene. CVD is a bottom-up approach that involves growing graphene on a substrate, typically copper or nickel, and is considered the most promising method for producing large-area, high-quality graphene. Each method has its own set of challenges, such as yield, quality, and scalability, which must be considered depending on the intended application.
Key Points Explained:
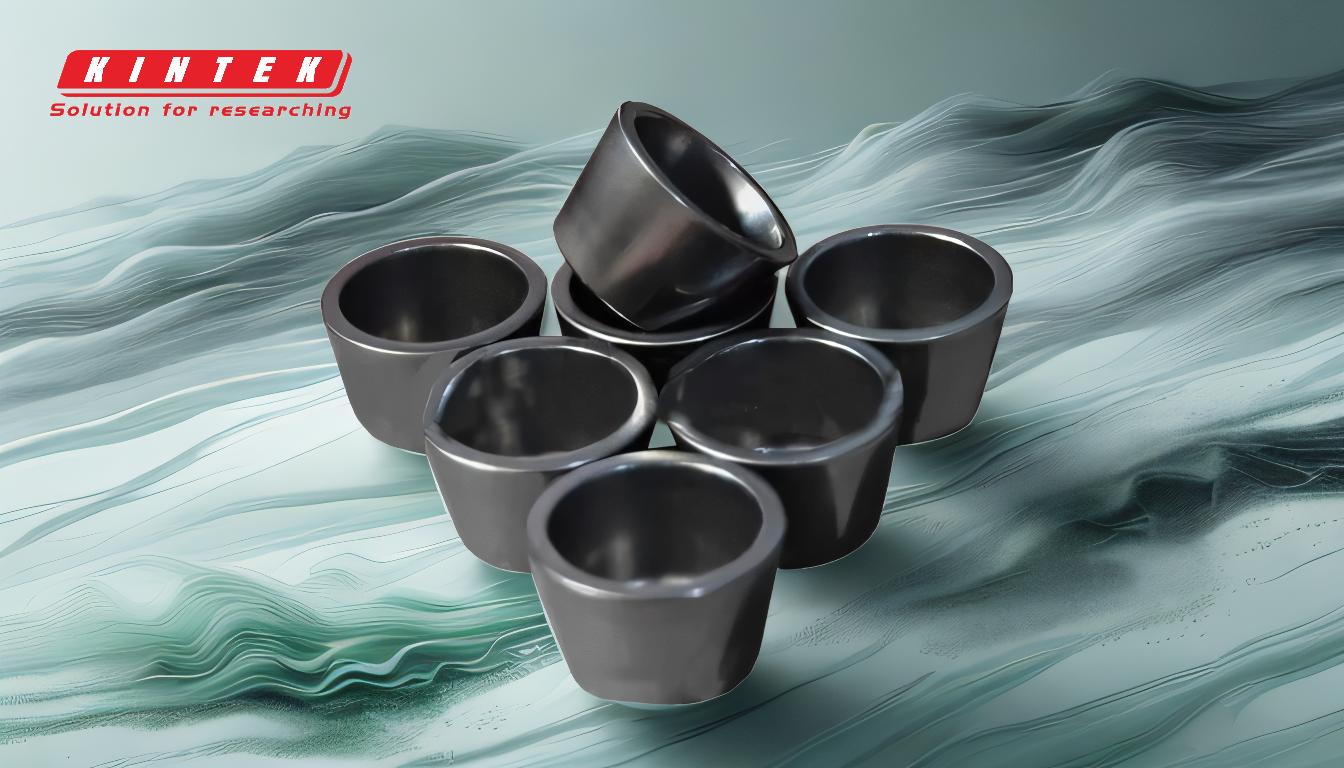
-
Mechanical Exfoliation
- Process: Mechanical exfoliation, also known as the "Scotch tape method," involves using adhesive tape to peel off layers of graphene from a graphite crystal. This method is straightforward and can produce high-quality graphene flakes.
-
Advantages:
- Produces high-quality graphene with minimal defects.
- Simple and inexpensive, making it ideal for research and fundamental studies.
-
Disadvantages:
- Not scalable for industrial applications.
- Low yield and time-consuming.
-
Liquid-Phase Exfoliation
- Process: This method involves dispersing graphite in a solvent (often non-aqueous, like n-Methyl-2-pyrrolidone) and applying energy, such as ultrasonic waves or high shear forces, to separate the graphene layers. Centrifugation is then used to isolate monolayer and few-layer graphene flakes.
-
Advantages:
- More scalable than mechanical exfoliation.
- Can produce graphene in large quantities, suitable for applications like composites and coatings.
-
Disadvantages:
- Graphene produced often has lower electrical quality.
- Requires post-processing steps like centrifugation to improve yield and quality.
-
Chemical Vapor Deposition (CVD)
- Process: CVD involves growing graphene on a substrate, typically copper or nickel, by exposing the substrate to a carbon-containing gas at high temperatures. The carbon atoms deposit on the substrate and form a graphene layer.
-
Advantages:
- Produces large-area, high-quality graphene.
- Scalable and suitable for industrial applications.
-
Disadvantages:
- Requires expensive equipment and precise control of reaction conditions.
- Post-processing steps, such as transferring graphene from the substrate, can introduce defects.
-
Reduction of Graphene Oxide (GO)
- Process: Graphene oxide is produced by oxidizing graphite, which is then reduced to graphene using chemical or thermal methods. This process can be combined with liquid-phase exfoliation to improve yield.
-
Advantages:
- Cost-effective and scalable.
- Can be used to produce graphene in bulk for applications like energy storage and sensors.
-
Disadvantages:
- Graphene produced often contains residual oxygen and defects, affecting its electrical properties.
- Requires additional steps to improve quality.
-
Sublimation of Silicon Carbide (SiC)
- Process: This method involves heating silicon carbide to high temperatures, causing the silicon atoms to sublimate and leaving behind a graphene layer on the surface.
-
Advantages:
- Produces high-quality graphene with excellent electrical properties.
- No need for a substrate transfer step, reducing the risk of defects.
-
Disadvantages:
- High cost due to the expensive starting material (SiC).
- Limited scalability for industrial applications.
-
Other Considerations
- Substrate Treatment: For methods like CVD, treating the substrate (e.g., chemically treating copper) can improve the quality of graphene by reducing defects and increasing the grain size of the substrate.
- Yield and Quality Trade-offs: Each method has trade-offs between yield, quality, and scalability. For example, mechanical exfoliation offers high quality but low yield, while liquid-phase exfoliation offers higher yield but lower quality.
- Application-Specific Methods: The choice of exfoliation method depends on the intended application. For example, CVD is ideal for electronics, while liquid-phase exfoliation may be more suitable for composites or coatings.
In summary, the choice of graphene exfoliation method depends on the desired balance between quality, yield, and scalability. Mechanical exfoliation is best for research, liquid-phase exfoliation for bulk applications, and CVD for high-quality, large-area graphene. Each method has its own set of challenges, but ongoing research continues to improve these processes, making graphene more accessible for a wide range of applications.
Summary Table:
Method | Process Summary | Advantages | Disadvantages |
---|---|---|---|
Mechanical Exfoliation | Using adhesive tape to peel graphene layers from graphite. | High-quality graphene, simple, and inexpensive. | Not scalable, low yield, and time-consuming. |
Liquid-Phase Exfoliation | Dispersing graphite in a solvent and applying energy to separate layers. | Scalable, suitable for bulk applications like composites. | Lower electrical quality, requires post-processing. |
Chemical Vapor Deposition (CVD) | Growing graphene on a substrate using carbon-containing gas. | Produces large-area, high-quality graphene, scalable for industrial use. | Expensive equipment, post-processing can introduce defects. |
Reduction of Graphene Oxide (GO) | Oxidizing graphite and reducing it to graphene. | Cost-effective, scalable for bulk applications. | Residual oxygen and defects affect electrical properties. |
Sublimation of Silicon Carbide (SiC) | Heating SiC to sublimate silicon, leaving graphene. | High-quality graphene, no substrate transfer needed. | High cost, limited scalability. |
Need help selecting the right graphene exfoliation method for your project? Contact our experts today!