Magnetron sputtering is a versatile and widely used physical vapor deposition (PVD) technique for coating substrates with thin films. It is characterized by its ability to deposit a wide range of materials, including metals, alloys, and ceramics, with high precision and uniformity. The process involves creating a plasma environment where target materials are bombarded by high-energy ions, causing atoms to be ejected and deposited onto a substrate. Magnetron sputtering is highly scalable, making it suitable for industrial applications, and offers advantages such as high deposition rates, excellent film density, and strong adhesion. The process can be further categorized into different types based on the configuration and operational parameters, each tailored for specific applications and material requirements.
Key Points Explained:
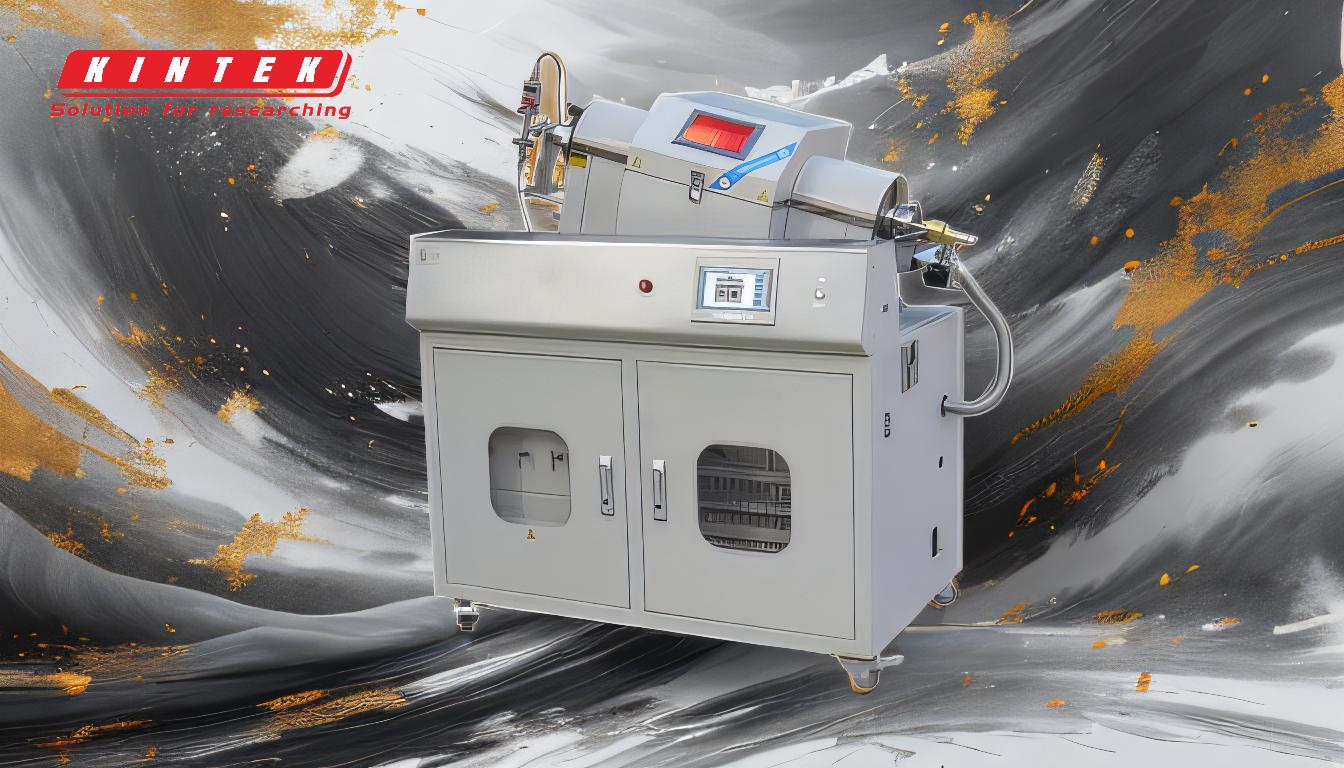
-
Basic Principles of Magnetron Sputtering:
- Magnetron sputtering operates by creating a plasma in a vacuum chamber using an inert gas, typically argon. A magnetic field is applied to confine electrons near the target surface, increasing the probability of ionizing the gas atoms. This enhances the sputtering efficiency and deposition rate.
- The target material is negatively charged, attracting positively charged argon ions. When these ions collide with the target, they dislodge atoms, which then travel and deposit onto the substrate, forming a thin film.
-
Types of Magnetron Sputtering:
- DC Magnetron Sputtering: This is the most common type, where a direct current (DC) power supply is used to generate the plasma. It is primarily used for conductive materials like metals. The simplicity and cost-effectiveness of DC sputtering make it ideal for industrial applications.
- RF Magnetron Sputtering: Radiofrequency (RF) sputtering is used for non-conductive materials, such as ceramics and dielectrics. The alternating current allows the system to handle insulating targets by preventing charge buildup on the target surface.
- Pulsed DC Magnetron Sputtering: This method combines the benefits of DC and RF sputtering. It uses pulsed DC power to deposit both conductive and non-conductive materials while reducing arcing and improving film quality.
- Reactive Magnetron Sputtering: In this process, reactive gases like oxygen or nitrogen are introduced into the chamber to create compound films (e.g., oxides or nitrides). This is useful for depositing materials like aluminum oxide or titanium nitride.
- High-Power Impulse Magnetron Sputtering (HiPIMS): HiPIMS uses short, high-power pulses to achieve high ionization rates of the sputtered material. This results in denser and more adherent films, making it suitable for demanding applications like cutting tools and wear-resistant coatings.
-
Advantages of Magnetron Sputtering:
- Versatility: It can deposit a wide range of materials, including metals, alloys, ceramics, and composites.
- High-Quality Films: The process produces films with excellent uniformity, density, and adhesion.
- Scalability: Magnetron sputtering is easily scalable for industrial production, with automation options available.
- Low Impurity Levels: The vacuum environment ensures minimal contamination, resulting in high-purity films.
- Heat-Sensitive Substrates: The process can deposit films on heat-sensitive materials without damaging them.
-
Key Parameters Influencing Magnetron Sputtering:
- Target Power Density: Higher power densities increase the sputtering rate but must be balanced to avoid target damage.
- Gas Pressure: Optimal gas pressure ensures efficient ionization and sputtering without excessive scattering of sputtered atoms.
- Substrate Temperature: Controlling the substrate temperature can influence film microstructure and properties.
- Deposition Rate: Adjusting the deposition rate is critical for achieving the desired film thickness and quality.
-
Applications of Magnetron Sputtering:
- Optical Coatings: Used for anti-reflective and reflective coatings in lenses and mirrors.
- Semiconductor Industry: Essential for depositing thin films in integrated circuits and microelectronics.
- Decorative Coatings: Applied to consumer products for aesthetic and protective purposes.
- Wear-Resistant Coatings: Used in cutting tools and industrial components to enhance durability.
By understanding the different types of magnetron sputtering and their unique characteristics, equipment and consumable purchasers can select the most appropriate method for their specific application, ensuring optimal performance and cost-effectiveness.
Summary Table:
Type | Description | Applications |
---|---|---|
DC Magnetron Sputtering | Uses direct current (DC) power for conductive materials like metals. | Industrial applications, cost-effective for large-scale production. |
RF Magnetron Sputtering | Uses radiofrequency (RF) power for non-conductive materials like ceramics and dielectrics. | Insulating materials, thin-film electronics. |
Pulsed DC Magnetron Sputtering | Combines DC and RF benefits, reducing arcing and improving film quality. | Conductive and non-conductive materials, high-quality films. |
Reactive Magnetron Sputtering | Introduces reactive gases (e.g., oxygen, nitrogen) to create compound films like oxides or nitrides. | Oxide or nitride coatings, wear-resistant films. |
HiPIMS | Uses high-power pulses for dense, adherent films, ideal for demanding applications. | Cutting tools, wear-resistant coatings, high-performance films. |
Need help choosing the right magnetron sputtering method for your application? Contact our experts today!