Electric arc furnaces (EAFs) are widely used in metal production due to their efficiency and flexibility. However, they come with several disadvantages that can impact operational efficiency, cost, and product quality. These include high power consumption, which strains electrical systems, and specific challenges related to non-self-consuming electrode arc furnaces, such as contamination risks, operational difficulties, and limitations in alloy composition control. Additionally, EAFs are often limited to small-scale production, making them less economically viable for large-scale operations unless electricity costs are exceptionally low.
Key Points Explained:
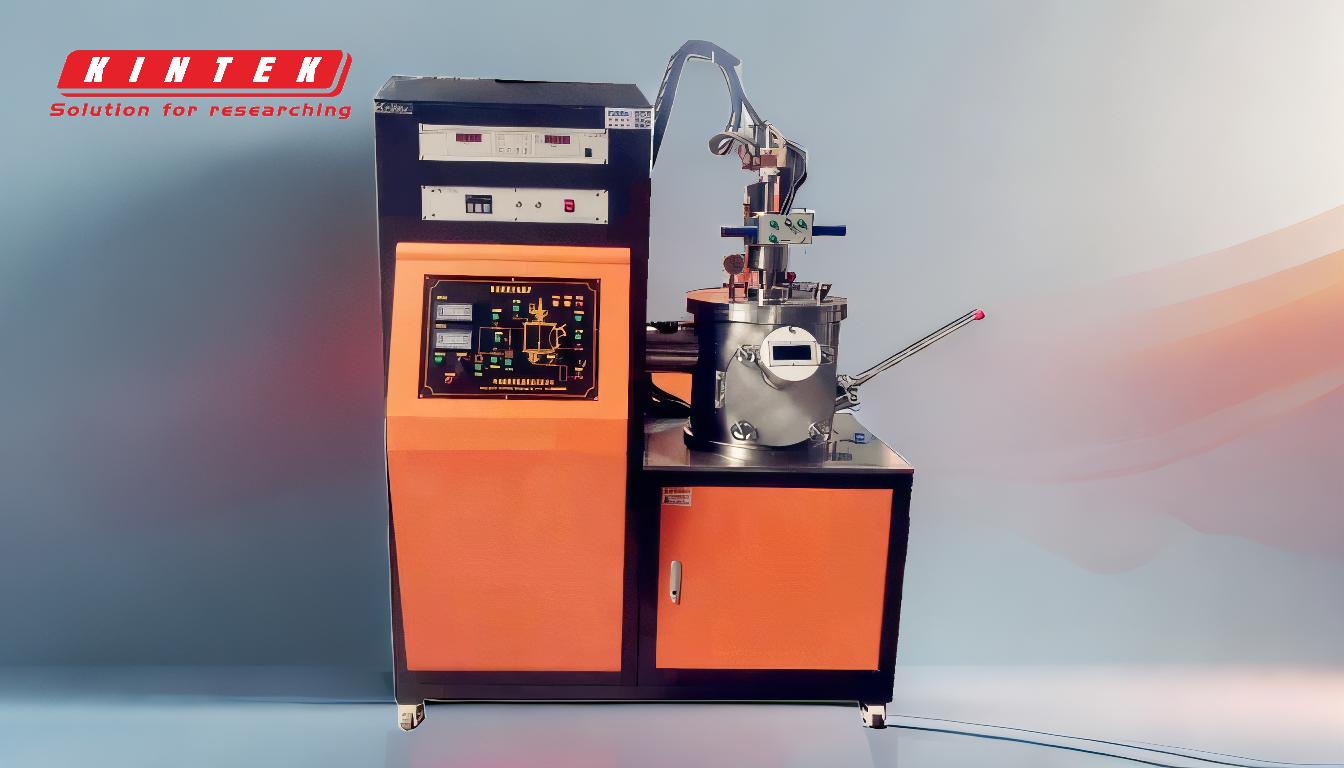
-
High Power Consumption
- Electric arc furnaces require a significant amount of electrical power to generate the heat needed for melting metals. This high energy demand can strain local electrical grids, especially in regions with limited power infrastructure.
- The reliance on electricity makes EAFs vulnerable to power supply fluctuations, which can disrupt production and increase operational costs.
- For industries operating in areas with high electricity costs, the energy consumption of EAFs can significantly impact overall profitability.
-
Contamination Risks in Non-Self-Consuming Electrode Arc Furnaces
- In non-self-consuming electrode arc furnaces, the molten metal is at risk of contamination from the electrode material. While such contamination is usually localized and rare, it can compromise the quality of the final product.
- Contamination is particularly problematic in industries requiring high-purity metals, such as aerospace or electronics manufacturing, where even minor impurities can lead to product failure.
-
Operational Challenges in Non-Self-Consuming Electrode Arc Furnaces
- Vacuum non-self-consuming arc furnaces often suffer from poor arc stability, making them difficult to operate consistently. This instability can lead to uneven heating and melting, affecting the quality of the metal produced.
- The process requires forming a molten pool before degassing, which adds complexity and time to the production process.
- These operational challenges can increase labor costs and reduce overall efficiency.
-
Limitations in Production Scale
- Non-self-consuming electrode arc furnaces are typically limited to small-scale production, with single melting alloy quantities ranging from dozens to hundreds of grams. This makes them unsuitable for large-scale industrial applications.
- The small production capacity also limits their economic viability, as the cost per unit of metal produced can be significantly higher compared to larger-scale alternatives.
-
Difficulty in Alloy Composition Control
- Controlling the proportion of alloy components in non-self-consuming electrode arc furnaces is challenging. The method of charging materials can lead to inconsistencies in alloy composition, affecting the final product's properties.
- This lack of precision is a significant drawback in industries where specific alloy compositions are critical, such as in the production of high-performance alloys for specialized applications.
-
Economic Viability Concerns
- Electric arc furnaces, particularly those using plasma torches or non-self-consuming electrodes, are often limited to handling only a few tonnes of dross or metal at a time. This small-scale operation is not economically viable unless electrical power is exceptionally cheap.
- For larger-scale operations, alternative methods such as blast furnaces or induction furnaces may be more cost-effective, especially in regions with high electricity costs.
In summary, while electric arc furnaces offer several advantages, including flexibility and efficiency, their disadvantages—such as high power consumption, contamination risks, operational challenges, and limitations in production scale and alloy control—must be carefully considered. These factors can impact both the quality of the final product and the overall cost-effectiveness of using EAFs in industrial applications.
Summary Table:
Disadvantage | Key Impact |
---|---|
High Power Consumption | Strains electrical systems, increases operational costs, and reduces profitability. |
Contamination Risks | Compromises product quality, especially in high-purity metal industries. |
Operational Challenges | Poor arc stability, uneven heating, and increased labor costs. |
Limitations in Production Scale | Limited to small-scale production, reducing economic viability. |
Difficulty in Alloy Composition Control | Inconsistent alloy proportions, affecting final product properties. |
Economic Viability Concerns | Small-scale operations are less cost-effective unless electricity is cheap. |
Need help choosing the right furnace for your metal production? Contact our experts today for tailored solutions!