Fast pyrolysis, while a promising technology for converting biomass into valuable products like bio-oil, bio-char, and syngas, faces several significant disadvantages. These include high capital and operating costs, technical challenges in scaling up the process, potential emissions of pollutants, variability in feedstock quality, high energy consumption, and the need for efficient separation and purification of end products. Additionally, the economic viability of fast pyrolysis is hindered by its cost disparity compared to fossil-based energy, creating barriers to market penetration. These challenges necessitate further research and development to optimize the process and make it more competitive and sustainable.
Key Points Explained:
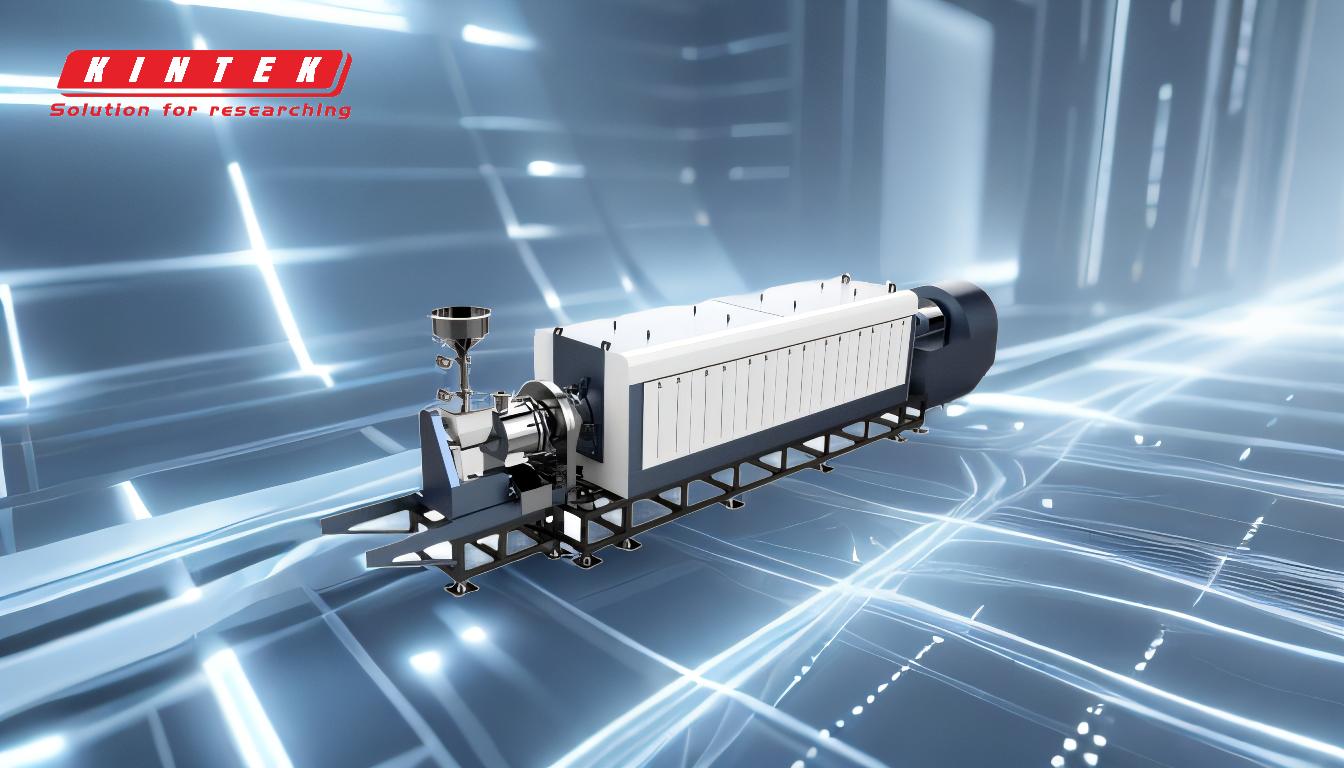
-
High Capital and Operating Costs:
- Explanation: Fast pyrolysis requires specialized equipment and machinery, which are expensive to purchase and maintain. The high temperatures and long residence times needed for the process also contribute to high energy consumption, further increasing operational costs.
- Impact: These costs make fast pyrolysis less economically viable compared to traditional fossil fuel-based energy sources, creating significant barriers to market entry and scalability.
-
Technical Challenges in Scaling Up:
- Explanation: While fast pyrolysis has been successfully demonstrated on a small scale, scaling up the process to industrial levels presents numerous technical challenges. These include maintaining consistent product quality, ensuring efficient heat transfer, and managing the complexities of larger systems.
- Impact: These challenges can lead to increased costs and potential failures in large-scale operations, limiting the widespread adoption of the technology.
-
Potential Emissions of Pollutants:
- Explanation: The fast pyrolysis process can emit pollutants such as volatile organic compounds (VOCs) and particulate matter. These emissions can have negative environmental and health impacts if not properly managed.
- Impact: The need for advanced emission control systems adds to the overall cost and complexity of the process, and regulatory compliance can be challenging.
-
Variability in Feedstock Quality and Composition:
- Explanation: Biomass feedstocks can vary widely in terms of moisture content, chemical composition, and physical properties. This variability can affect the efficiency and consistency of the pyrolysis process.
- Impact: Inconsistent feedstock quality can lead to variations in the quality and quantity of the final products, making it difficult to achieve reliable and predictable outcomes.
-
High Energy Consumption:
- Explanation: Fast pyrolysis requires high temperatures (typically between 400-600°C) and long residence times to achieve the desired conversion of biomass into bio-oil, bio-char, and syngas. This results in significant energy consumption.
- Impact: The high energy demand increases operational costs and reduces the overall energy efficiency of the process, making it less competitive with other energy sources.
-
Need for Efficient Separation and Purification:
- Explanation: The mixed product stream from fast pyrolysis (comprising bio-oil, bio-char, and syngas) requires further separation and purification to obtain usable end products. This adds complexity and cost to the process.
- Impact: The additional steps required for separation and purification increase the overall cost and reduce the economic viability of fast pyrolysis, especially when compared to simpler fossil fuel-based processes.
-
Economic and Non-Technical Barriers:
- Explanation: Despite the potential benefits, fast pyrolysis technologies face economic and non-technical barriers, such as the high cost disparity compared to fossil-based energy and the need for full integration into a biomass system.
- Impact: These barriers hinder the widespread adoption and commercialization of fast pyrolysis, limiting its potential to contribute to sustainable energy solutions.
In summary, while fast pyrolysis offers a promising pathway for converting biomass into valuable products, it is currently hindered by high costs, technical challenges, potential emissions, feedstock variability, high energy consumption, and the need for efficient separation and purification. Addressing these disadvantages through further research and development is crucial for optimizing the process and making it a viable and competitive option in the energy market.
Summary Table:
Disadvantage | Explanation | Impact |
---|---|---|
High Capital and Operating Costs | Requires expensive equipment and high energy consumption. | Reduces economic viability and scalability. |
Technical Challenges in Scaling Up | Difficulties in maintaining product quality and heat transfer at large scales. | Increases costs and risks of failure in industrial applications. |
Potential Emissions of Pollutants | Releases VOCs and particulate matter if not managed properly. | Adds cost for emission control systems and complicates regulatory compliance. |
Variability in Feedstock Quality | Inconsistent moisture, composition, and properties of biomass feedstocks. | Leads to unpredictable product quality and quantity. |
High Energy Consumption | Requires high temperatures (400-600°C) and long residence times. | Increases operational costs and reduces energy efficiency. |
Need for Separation and Purification | Mixed product stream requires additional processing. | Adds complexity and cost, reducing economic competitiveness. |
Economic and Non-Technical Barriers | High cost disparity with fossil fuels and integration challenges. | Hinders widespread adoption and commercialization. |
Interested in overcoming the challenges of fast pyrolysis? Contact our experts today to explore solutions!