Fluidized bed reactors (FBRs) are widely used in various industries due to their advantages, such as uniform particle mixing, temperature gradients, and continuous operation. However, they also come with several notable disadvantages. These include increased reactor vessel size, higher pumping requirements and pressure drop, particle entrainment, erosion of internal components, and pressure loss scenarios. Additionally, fluidized-bed pyrolyzers, a specific type of FBR, face challenges such as the need for small particle sizes, large quantities of inert gases, and high operating costs. Understanding these drawbacks is crucial for making informed decisions when considering FBRs for specific applications.
Key Points Explained:
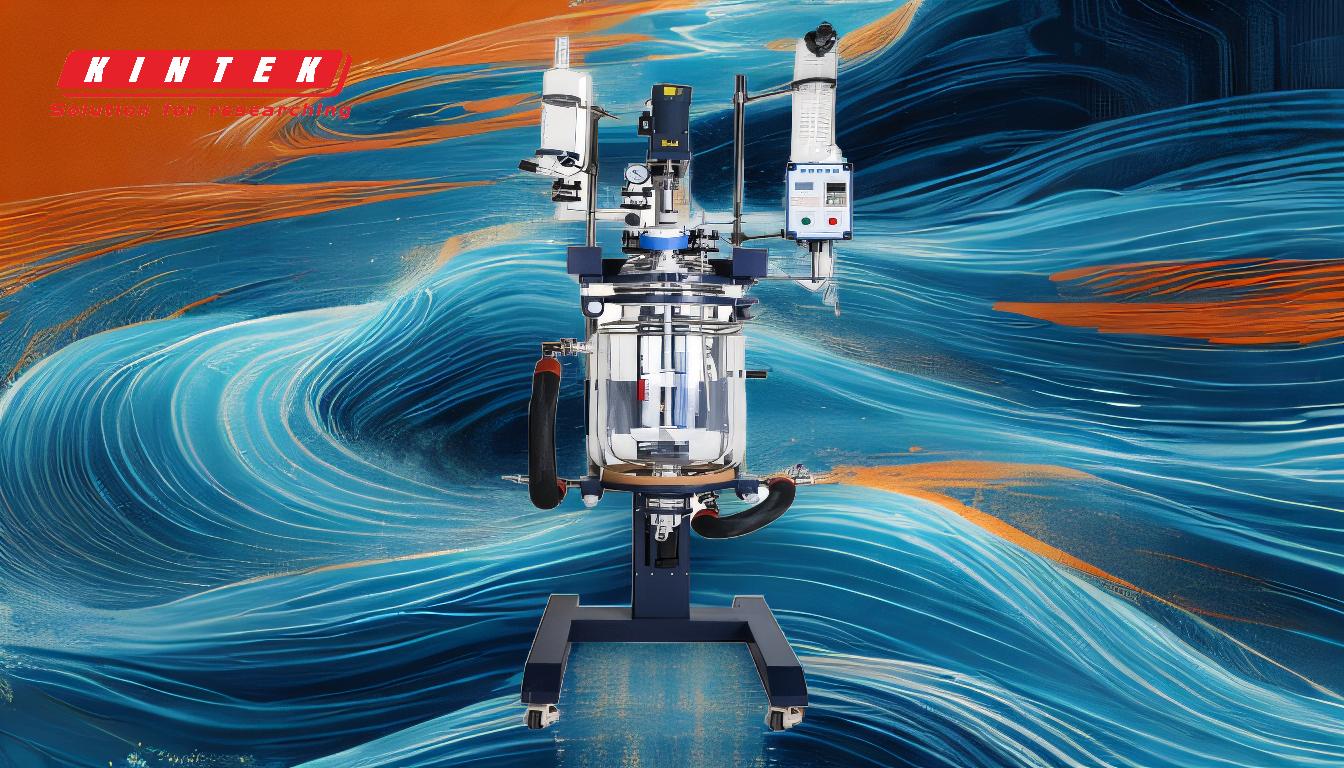
-
Increased Reactor Vessel Size:
- Fluidized bed reactors often require larger vessel sizes compared to other reactor types. This is due to the need to accommodate the fluidized particles and ensure proper mixing and reaction conditions. The larger size can lead to higher capital costs and more space requirements, which may not be feasible for all applications.
-
Higher Pumping Requirements and Pressure Drop:
- FBRs typically require higher pumping power to maintain the fluidized state of the particles. This results in increased energy consumption and operational costs. Additionally, the pressure drop across the bed can be significant, necessitating robust and expensive pumping systems to maintain the desired flow rates.
-
Particle Entrainment:
- One of the challenges with FBRs is the entrainment of fine particles in the gas stream. This can lead to loss of valuable reactants or products and may require additional equipment, such as cyclones or filters, to capture and recycle the entrained particles. This adds complexity and cost to the system.
-
Erosion of Internal Components:
- The continuous movement of particles in a fluidized bed can cause erosion of internal components, such as the reactor walls, distributor plates, and heat exchangers. This erosion can lead to frequent maintenance and replacement of parts, increasing the overall operational costs and downtime.
-
Pressure Loss Scenarios:
- FBRs are susceptible to pressure loss scenarios, which can disrupt the fluidization process and affect the overall performance of the reactor. Managing and mitigating these pressure losses require careful design and monitoring, adding to the complexity and cost of the system.
-
Requirement for Small Particle Sizes:
- Fluidized-bed pyrolyzers, a specific type of FBR, require small particle sizes to achieve optimal performance. This necessitates additional processing steps to reduce particle size, which can increase the overall cost and complexity of the system.
-
Large Quantity of Inert Gases:
- The operation of fluidized-bed pyrolyzers often requires a large quantity of inert gases to maintain the desired reaction conditions. This can lead to higher operational costs and the need for additional gas handling and storage infrastructure.
-
High Operating Costs:
- The combination of higher pumping requirements, particle entrainment, erosion of internal components, and the need for small particle sizes and inert gases contributes to the high operating costs associated with FBRs. These costs can be a significant drawback, especially for applications where cost-efficiency is a critical factor.
In summary, while fluidized bed reactors offer several advantages, such as uniform mixing and temperature gradients, they also come with notable disadvantages that need to be carefully considered. These include increased reactor size, higher pumping requirements, particle entrainment, erosion of internal components, pressure loss scenarios, and high operating costs. Understanding these drawbacks is essential for making informed decisions when selecting and designing FBRs for specific applications.
Summary Table:
Disadvantage | Description |
---|---|
Increased Reactor Vessel Size | Larger vessels increase capital costs and space requirements. |
Higher Pumping Requirements | Requires more energy and robust systems to maintain fluidization. |
Particle Entrainment | Fine particles may escape, requiring additional equipment for recovery. |
Erosion of Internal Components | Continuous particle movement causes wear, leading to frequent maintenance. |
Pressure Loss Scenarios | Pressure drops can disrupt fluidization, requiring careful design and monitoring. |
Requirement for Small Particle Sizes | Additional processing needed to reduce particle size, increasing costs. |
Large Quantity of Inert Gases | High operational costs due to the need for inert gases. |
High Operating Costs | Combined factors lead to significant operational expenses. |
Need help deciding if fluidized bed reactors are right for your application? Contact our experts today!