Graphite furnaces are widely used for high-temperature applications due to their ability to generate extreme heat, making them suitable for processes like sintering, graphitizing, and pyrolysis. However, they come with significant disadvantages, including the need for heavy power supplies and water cooling systems, which limit their portability. Additionally, graphite furnaces are prone to oxidation under atmospheric conditions, requiring protective gases to extend their lifespan. The reducing atmosphere within these furnaces can also attack refractories and introduce uncertainties in melting-point determinations. These factors make graphite furnaces less versatile and more challenging to maintain compared to other heating systems.
Key Points Explained:
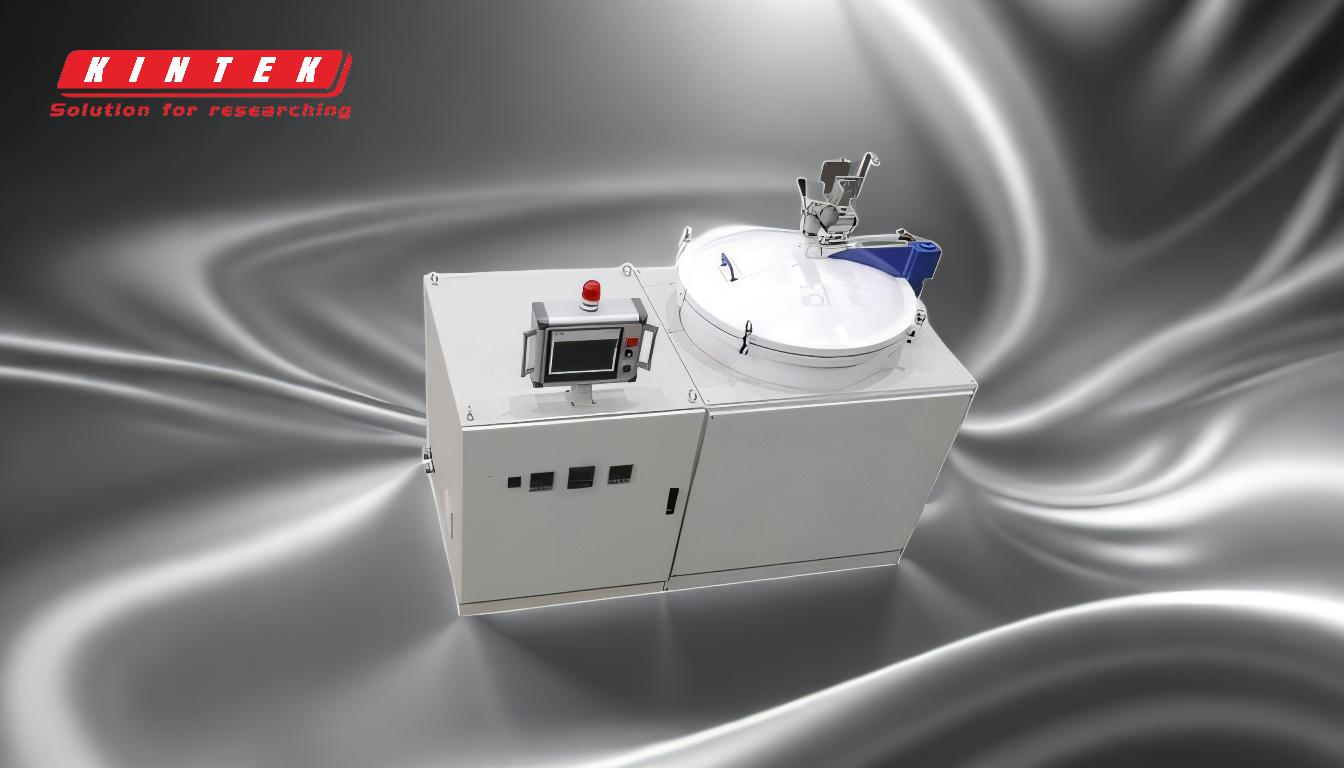
-
Heavy Power Supplies and Water Cooling Systems
- Graphite furnaces require substantial power supplies to generate the high temperatures needed for processes like sintering and graphitizing.
- Water cooling systems are essential to manage the heat generated, adding to the overall weight and complexity of the equipment.
- These requirements make graphite furnaces unsuitable for portable or field applications, limiting their use to fixed laboratory or industrial settings.
-
Oxidation and Short Lifespan
- Graphite furnaces are prone to oxidation when operated under atmospheric pressure, significantly reducing their operational lifespan.
- To mitigate oxidation, neutral or reducing gases (e.g., argon or nitrogen) must be passed through or around the furnace.
- This adds complexity and cost to the system, as it requires a continuous supply of protective gases.
-
Reducing Atmosphere and Refractory Attack
- The atmosphere inside graphite furnaces is strongly reducing, which can degrade many refractory materials over time.
- This necessitates frequent maintenance or replacement of furnace components, increasing operational costs.
- The reducing environment can also complicate processes like melting-point determinations, as it may alter the chemical composition of materials being heated.
-
Uncertainty in Melting-Point Determinations
- The reducing atmosphere can introduce uncertainties in melting-point determinations, as it may cause unintended chemical reactions or reductions.
- This makes it difficult to achieve precise and reproducible results, particularly in research or quality control applications.
-
Limited Versatility
- While graphite furnaces excel in high-temperature applications, their design and operational constraints limit their versatility.
- They are not well-suited for applications requiring portability, rapid heating/cooling cycles, or precise atmospheric control.
- Alternative heating systems, such as induction or resistance furnaces, may offer greater flexibility for certain applications.
-
High Operational and Maintenance Costs
- The need for heavy power supplies, water cooling, protective gases, and frequent refractory replacements contributes to high operational costs.
- Maintenance requirements are also higher compared to other types of furnaces, as components must be regularly inspected and replaced to ensure consistent performance.
In summary, while graphite furnaces are highly effective for specific high-temperature applications, their disadvantages—including high operational costs, susceptibility to oxidation, and limited portability—make them less suitable for certain uses. These factors should be carefully considered when selecting a furnace for a particular application.
Summary Table:
Disadvantages | Details |
---|---|
Heavy Power Supplies & Water Cooling | Requires substantial power and water cooling, limiting portability. |
Oxidation & Short Lifespan | Prone to oxidation; requires protective gases to extend lifespan. |
Reducing Atmosphere & Refractory Attack | Degrades refractory materials, increasing maintenance costs. |
Uncertainty in Melting-Point Determinations | Reducing atmosphere can alter chemical compositions, causing uncertainties. |
Limited Versatility | Not suitable for portable or rapid heating/cooling applications. |
High Operational & Maintenance Costs | Frequent maintenance and protective gas use increase overall costs. |
Need help choosing the right furnace for your application? Contact our experts today for personalized advice!