Induction melting is a widely used process in metallurgy due to its efficiency, speed, and precision. However, it is not without its drawbacks. The primary disadvantages include a time-consuming cooling process, challenges in maintaining tight dimensional tolerances, and the necessity for additional machining and polishing, which can increase costs and production time. Despite these limitations, induction melting remains a preferred method for many applications due to its numerous advantages, such as energy efficiency, environmental friendliness, and the ability to produce high-quality metals with minimal contamination.
Key Points Explained:
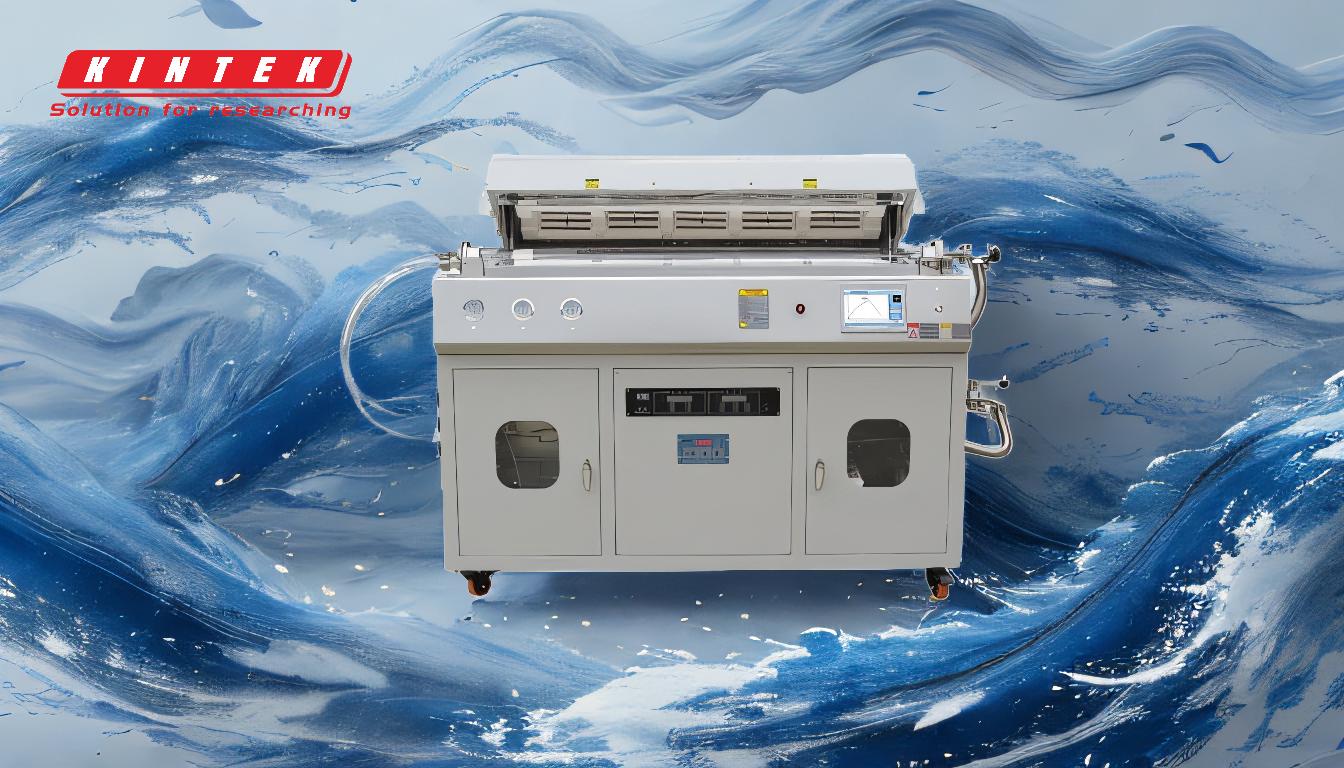
-
Time-Consuming Cooling Process:
- Induction melting involves rapid heating, but the cooling process can be slower, especially when precise temperature control is required. This can lead to longer production cycles, particularly for large-scale operations or when dealing with metals that require specific cooling rates to achieve desired material properties.
-
Difficulty in Holding Tight Dimensional Tolerances:
- While induction melting offers precise control over the melting process, maintaining tight dimensional tolerances in the final product can be challenging. This is often due to the inherent nature of the process, which may introduce slight variations in the molten metal's flow and solidification patterns. As a result, additional machining may be required to achieve the desired dimensions, adding to the overall cost and time.
-
Need for Additional Machining and Polishing:
- The surface finish of parts produced through induction melting may not always meet the required standards directly from the furnace. This necessitates additional machining and polishing to achieve the desired surface quality. These post-processing steps can significantly increase the overall production cost and extend the lead time.
-
Energy Efficiency and Environmental Impact:
- Despite the drawbacks, induction melting is highly energy-efficient compared to conventional methods like fossil fuel furnaces. Induction furnaces can achieve efficiencies of up to 92%, significantly reducing energy consumption and minimizing environmental pollution. This makes induction melting a more sustainable option in the long run.
-
Production of High-Quality Metals:
- Induction melting is known for producing high-quality metals with minimal contamination. The process allows for precise control over the composition of the alloy, ensuring that the final product meets stringent quality standards. Additionally, the inherent inductive stirring ensures a homogeneous mix of the molten metal, which is crucial for achieving consistent material properties.
-
Flexibility and Customization:
- One of the significant advantages of induction melting is its flexibility. The process can be easily customized to melt different types of metals and alloys, making it suitable for a wide range of applications. The ability to quickly change over between different materials and the option for immediate shutdown if needed further enhance its operational efficiency.
-
Safety and Cleanliness:
- Induction melting is a clean process that does not produce dust, smoke, or pollutants, making it safer for both operators and the environment. The elimination of combustion heating reduces the risks of fire, explosion, or burns, contributing to a safer work environment.
In summary, while induction melting has its disadvantages, such as the need for additional machining and challenges in maintaining tight tolerances, its advantages in terms of energy efficiency, environmental impact, and the production of high-quality metals make it a valuable process in modern metallurgy.
Summary Table:
Disadvantages | Challenges | Impact |
---|---|---|
Time-Consuming Cooling Process | Slower cooling, especially for precise temperature control | Longer production cycles, increased costs |
Difficulty in Holding Tight Tolerances | Variations in molten metal flow and solidification | Additional machining required, higher costs |
Need for Additional Machining and Polishing | Surface finish may not meet standards directly from the furnace | Increased production costs and lead time |
Advantages | Benefits | Impact |
Energy Efficiency | Up to 92% efficiency, reduced energy consumption | Lower operational costs, environmental sustainability |
High-Quality Metal Production | Minimal contamination, precise alloy composition control | Consistent material properties, high-quality output |
Flexibility and Customization | Suitable for various metals and alloys, quick changeover | Enhanced operational efficiency |
Safety and Cleanliness | No dust, smoke, or pollutants; reduced fire and explosion risks | Safer work environment, eco-friendly process |
Want to learn more about induction melting and how it can benefit your operations? Contact our experts today for tailored advice!