LPCVD (Low-Pressure Chemical Vapor Deposition) is widely used in semiconductor manufacturing and MEMS devices due to its ability to produce high-quality, uniform films with excellent conformal step coverage. However, despite its advantages, LPCVD has several disadvantages, including challenges in precise control during large-scale production, the use of toxic or flammable materials, high-temperature requirements, and issues with nonuniform film removal. These limitations can impact its suitability for certain applications and materials.
Key Points Explained:
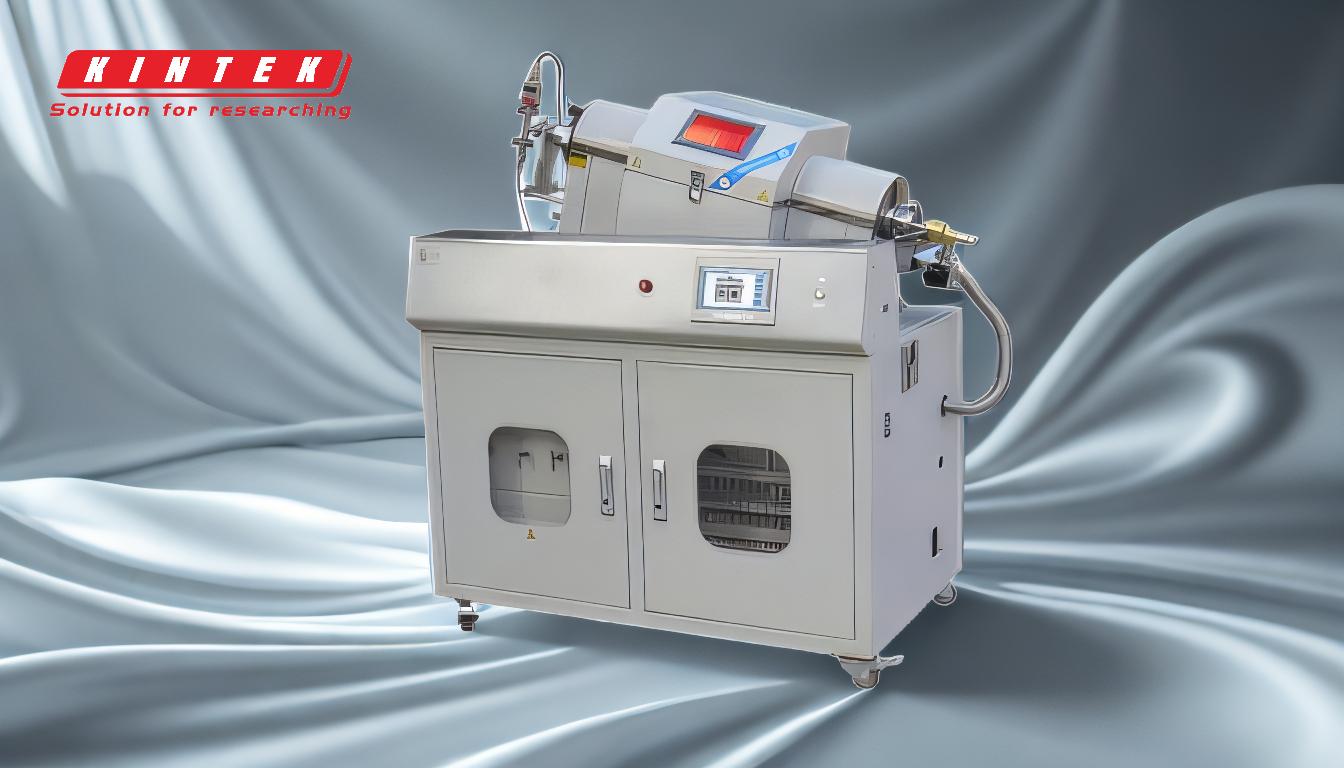
-
Challenges in Precise Control and Scaling Up:
- Maintaining uniform temperature and pressure profiles across large substrates or multiple wafers is difficult, especially in large-scale production. This requires sophisticated equipment and advanced process control strategies, which can increase costs and complexity.
-
High-Temperature Requirements:
- LPCVD typically operates at higher temperatures, which limits the types of materials that can be used. High temperatures are not always suitable for production-scale systems and can lead to thermal stress or damage to sensitive substrates.
-
Nonuniform Film Removal:
- High temperatures and high concentrations of oxygen or nitrogen during LPCVD can cause nonuniform film removal. This is due to increased ion bombardment, which leads to uneven etching. Achieving uniform film properties requires careful optimization of the process.
-
Use of Toxic or Flammable Materials:
- LPCVD often involves highly toxic or flammable source materials, which pose safety risks and require specialized handling and equipment. This adds to the operational complexity and cost of the process.
-
Shorter Species Lifetime:
- In LPCVD, the lifetime of reactive species is shorter than the time needed for them to travel from the plasma to the deposits. This can negatively affect the material etching process and lead to inconsistencies in film quality.
-
Limitations in Material Compatibility:
- The high-temperature nature of LPCVD restricts its use with temperature-sensitive materials. This limits its versatility in applications where lower-temperature processes are required.
-
Cost and Complexity:
- While LPCVD is cost-effective for certain applications, the need for advanced equipment, precise control systems, and safety measures can increase overall costs, particularly for large-scale or specialized production.
In summary, while LPCVD offers significant advantages in producing high-quality films, its disadvantages—such as high-temperature requirements, nonuniform film removal, and the use of hazardous materials—must be carefully considered when selecting a deposition method for specific applications.
Summary Table:
Disadvantage | Description |
---|---|
Precise Control & Scaling Challenges | Difficult to maintain uniform temperature/pressure in large-scale production. |
High-Temperature Requirements | Limits material compatibility and risks thermal damage to sensitive substrates. |
Nonuniform Film Removal | High temperatures and ion bombardment lead to uneven etching and film removal. |
Toxic or Flammable Materials | Requires specialized handling and safety measures, increasing operational costs. |
Shorter Species Lifetime | Reactive species decay before reaching deposits, affecting film quality. |
Material Compatibility Limitations | High temperatures restrict use with temperature-sensitive materials. |
Cost & Complexity | Advanced equipment and safety measures increase overall production costs. |
Need help selecting the right deposition method for your application? Contact our experts today!