Nitriding, while offering significant advantages in enhancing material properties such as wear resistance and surface hardness, comes with several disadvantages. These include challenges related to process control, environmental concerns, and economic factors. Plasma nitriding, for instance, requires meticulous surface preparation and careful management of power distribution to prevent overheating and unstable arcs. Liquid nitriding, on the other hand, faces restrictions due to the use of toxic cyanide salts, despite the development of non-toxic alternatives. Additionally, the high initial costs associated with plasma nitriding equipment and the limitations on batch processing due to the power/area relationship further complicate its adoption.
Key Points Explained:
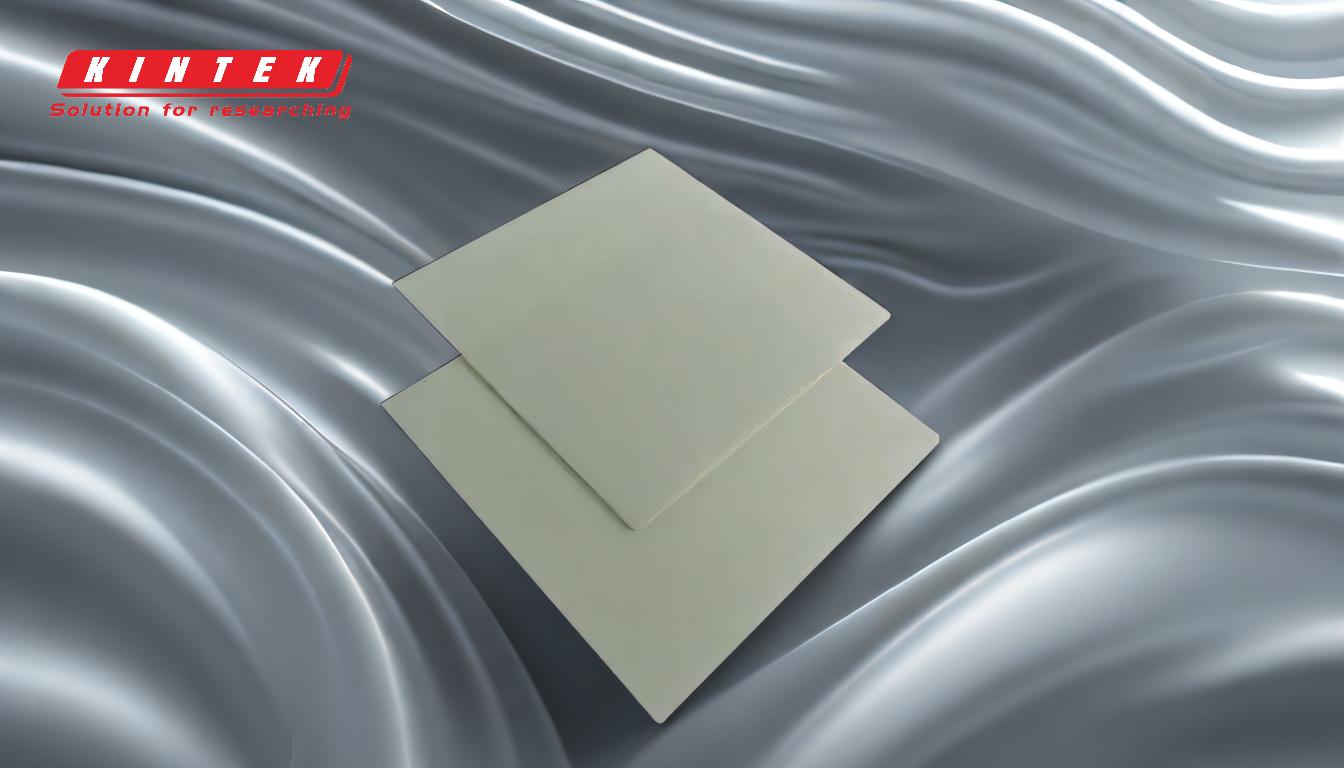
-
Surface Cleanliness and Stability in Plasma Nitriding:
- Critical Surface Preparation: The effectiveness of plasma nitriding heavily depends on the cleanliness of the component surfaces. Any contamination can lead to the formation of unstable arcs during the heating cycles, which can compromise the quality of the nitrided layer.
- Prevention of Overheating: Parts require precise repair and preparation to avoid overheating during the process, which can lead to material degradation or failure.
-
Batch Processing Limitations:
- Power/Area Relationship: In plasma nitriding, components of similar size cannot be processed in one batch due to the power/area relationship. This limitation necessitates multiple runs or specialized setups, increasing both the time and cost of production.
-
Economic Considerations:
- High Initial Costs: The setup for plasma nitriding involves significant initial investment in equipment and technology. This high cost can be a barrier for smaller operations or those with limited budgets.
-
Environmental and Health Concerns in Liquid Nitriding:
- Use of Toxic Cyanide Salts: Traditional liquid nitriding processes use cyanide salts, which pose serious health risks to operators and environmental challenges in waste disposal.
- Regulatory Restrictions: Due to these health and environmental risks, the use of cyanide salts is increasingly restricted, pushing the industry towards non-toxic alternatives, though these may not yet match the effectiveness of traditional methods.
-
Thin Nitriding Layer:
- Layer Thickness: Liquid nitriding typically results in a relatively thin nitriding layer (0.01-0.02mm), which may not be sufficient for applications requiring deeper case hardening.
In summary, while nitriding processes significantly enhance material properties, they come with a set of challenges that need careful consideration. These include technical limitations in processing, economic barriers, and environmental and health concerns, particularly with liquid nitriding. Understanding these disadvantages is crucial for industries to make informed decisions about the adoption and implementation of nitriding technologies.
Summary Table:
Disadvantage | Description |
---|---|
Surface Cleanliness & Stability | Plasma nitriding requires meticulous surface prep to avoid unstable arcs and overheating. |
Batch Processing Limitations | Power/area relationship restricts batch processing, increasing time and costs. |
High Initial Costs | Plasma nitriding equipment involves significant upfront investment. |
Environmental & Health Concerns | Liquid nitriding uses toxic cyanide salts, posing health and disposal challenges. |
Thin Nitriding Layer | Liquid nitriding produces thin layers (0.01-0.02mm), limiting depth for some applications. |
Need help navigating the challenges of nitriding? Contact our experts today for tailored solutions!