Physical vapor deposition (PVD) is a widely used technique for applying thin film coatings, offering benefits such as enhanced durability, corrosion resistance, and environmental friendliness. However, it also comes with several disadvantages that can impact its suitability for certain applications. These drawbacks include high operational costs, limitations in coating complex geometries, slower deposition rates, and the need for specialized equipment and skilled operators. Understanding these limitations is crucial for making informed decisions when considering PVD for specific industrial or manufacturing needs.
Key Points Explained:
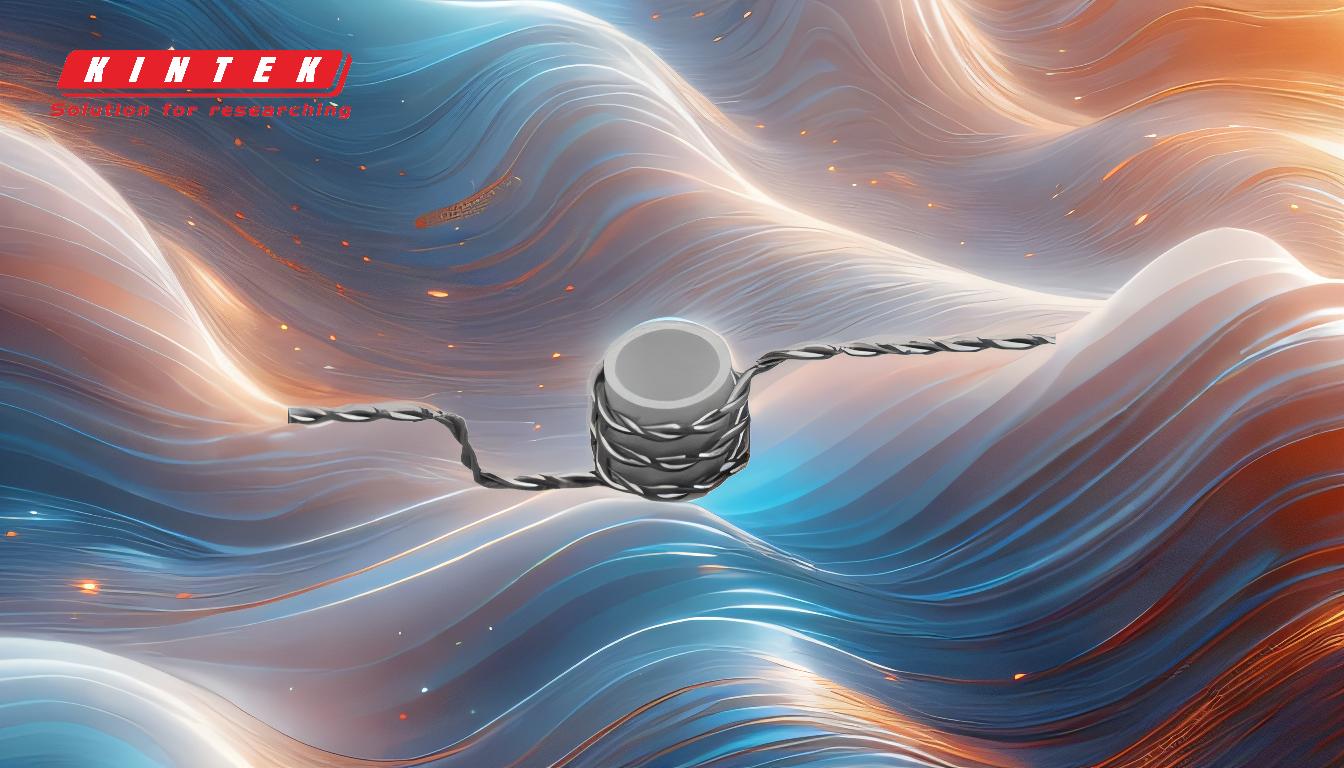
-
High Operational Costs
- PVD processes often require significant energy input due to intense heating and cooling cycles. This increases operational expenses, especially in large-scale applications.
- The cost of equipment, such as vacuum chambers and advanced sputtering systems, is high. Additionally, maintenance and repair of these systems can be expensive.
- Skilled operators are needed to manage the complex machinery, further driving up labor costs.
-
Line-of-Sight Limitation
- PVD is a "line of sight" technique, meaning it can only coat surfaces directly exposed to the vapor source. This makes it unsuitable for coating complex geometries or non-visible surfaces, such as internal cavities or intricate components.
- This limitation restricts its use in applications requiring uniform coating on all surfaces, such as certain medical devices or aerospace components.
-
Relatively Slow Deposition Rates
- Compared to other coating methods like chemical vapor deposition (CVD), PVD has slower deposition rates. This can lead to longer processing times, reducing throughput and efficiency in high-volume production environments.
- The slower rate may also limit its use in applications requiring rapid turnaround times.
-
Equipment Complexity and Scalability Challenges
- PVD systems are complex and require precise control of parameters like pressure, temperature, and power. This complexity can make scaling up production difficult and costly.
- While some PVD methods, such as magnetron sputtering, offer better scalability, they are still more expensive than alternative techniques.
-
Limited Material Compatibility
- PVD is primarily used for metallic and ceramic coatings, which may not be suitable for all applications. For example, it is less effective for depositing certain polymers or organic materials.
- The process may also struggle with multi-component materials due to variations in vapor pressure and nucleation rates.
-
Environmental and Safety Concerns
- Although PVD is generally considered environmentally friendly compared to CVD, it still involves the use of high-energy processes and potentially hazardous materials.
- Proper handling and disposal of by-products, such as metal vapors and particulates, are necessary to ensure safety and compliance with environmental regulations.
-
Residual Stress and Coating Integrity
- PVD coatings can sometimes exhibit residual stress, which may affect the mechanical properties of the coated material. This stress can lead to issues like cracking or delamination under certain conditions.
- Ensuring coating uniformity and adhesion can also be challenging, particularly on substrates with irregular surfaces.
By carefully weighing these disadvantages against the advantages of PVD, such as its durability and environmental benefits, stakeholders can determine whether it is the right choice for their specific application. Alternatives like CVD or hybrid techniques may be more suitable in cases where PVD's limitations are prohibitive.
Summary Table:
Disadvantage | Key Details |
---|---|
High Operational Costs | Energy-intensive processes, expensive equipment, and skilled labor requirements. |
Line-of-Sight Limitation | Cannot coat complex geometries or internal surfaces. |
Slow Deposition Rates | Slower than CVD, reducing throughput in high-volume production. |
Equipment Complexity | Requires precise control, making scalability challenging. |
Limited Material Compatibility | Primarily for metallic/ceramic coatings; struggles with polymers. |
Environmental and Safety Concerns | High-energy processes and hazardous by-products. |
Residual Stress and Coating Issues | Risk of cracking, delamination, and adhesion challenges. |
Need help deciding if PVD is right for your application? Contact our experts today!