Planetary ball mills are widely used in material science, chemistry, and other industries for grinding and mixing materials into fine particles. While they offer advantages such as high grinding energy and the ability to produce very small particle sizes, they also come with several disadvantages. These include high energy consumption, significant wear and tear, potential thermal damage to materials, loud noise during operation, and limitations in handling certain types of materials. Additionally, the equipment can be cumbersome, heavy, and may require frequent maintenance due to the wear of components. These factors can impact the efficiency, cost, and overall usability of planetary ball mills in various applications.
Key Points Explained:
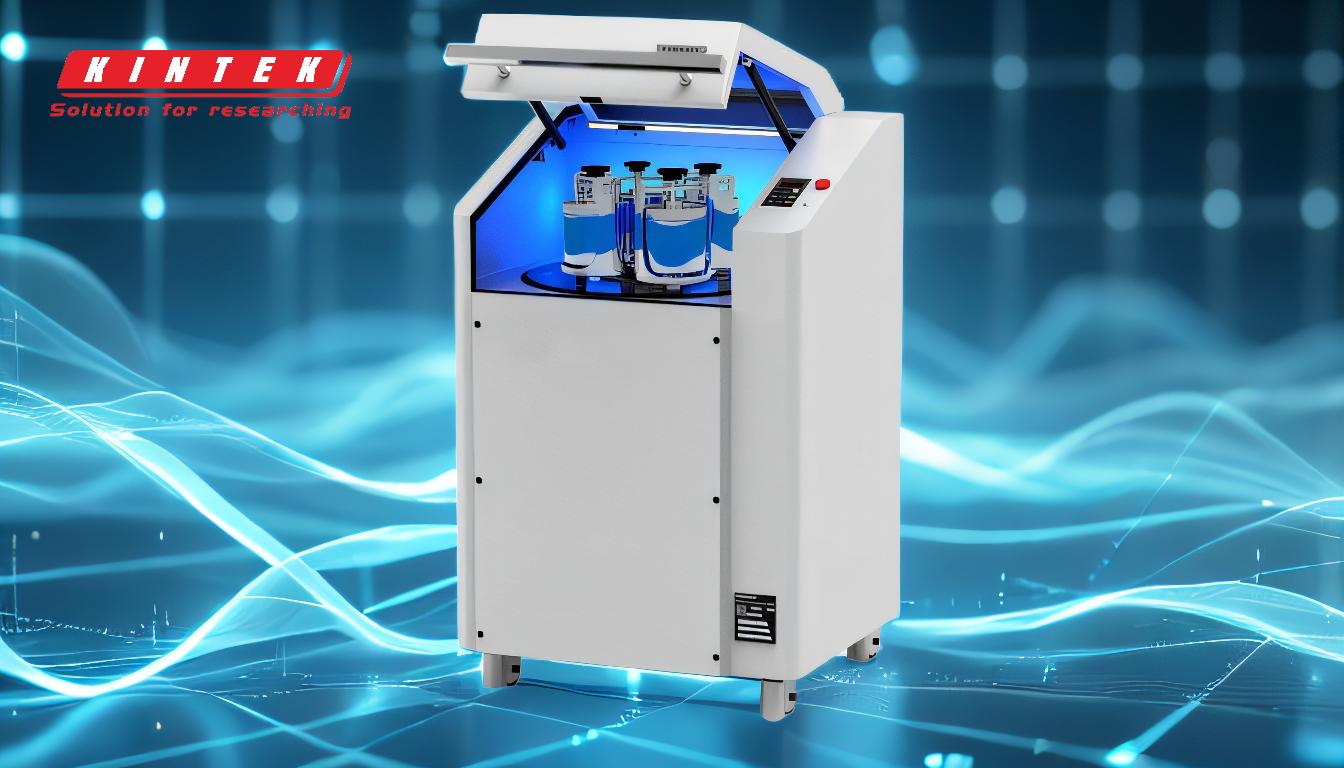
-
High Energy Consumption:
- Planetary ball mills consume a significant amount of energy, primarily due to the wear of grinding balls and wall armor, friction, and the heating of materials during the grinding process.
- This high energy consumption can lead to increased operational costs, making it less economical for large-scale or continuous use.
-
Significant Wear and Tear:
- The friction between the grinding media (balls) and the material being processed leads to considerable wear on the equipment.
- Components such as the grinding balls, wall armor, and other internal parts may need frequent replacement, increasing maintenance costs and downtime.
-
Potential Thermal Damage to Materials:
- The heat generated during the grinding process can cause thermal damage to sensitive materials, potentially altering their properties or reducing the quality of the final product.
- This is particularly problematic for materials that are heat-sensitive or require precise temperature control.
-
Loud Noise During Operation:
- Planetary ball mills produce loud noise during operation due to the high-speed rotation and impact of grinding balls.
- This noise can be a significant issue in environments where noise pollution is a concern, requiring additional soundproofing measures or protective equipment for operators.
-
Limitations in Handling Certain Materials:
- Planetary ball mills are not suitable for grinding soft, tacky, or fibrous materials, as these can clog the equipment or reduce its efficiency.
- This limitation restricts the range of materials that can be processed using planetary ball mills.
-
Contamination Risks:
- The wear of internal components, such as the grinding balls and wall armor, can lead to contamination of the material being processed.
- This is particularly problematic in applications where material purity is critical, such as in the production of pharmaceuticals or high-purity chemicals.
-
Cumbersome and Heavy Equipment:
- Planetary ball mills are often large and heavy, making them difficult to move or install in certain environments.
- This can be a disadvantage in facilities with limited space or where equipment mobility is required.
-
Slow Process:
- The grinding process in planetary ball mills can be relatively slow, especially when compared to other types of milling equipment.
- This slow processing time can be a bottleneck in production lines where speed and efficiency are critical.
-
Vibrations:
- Planetary ball mills can produce strong vibrations during operation, which can affect the stability of the equipment and the surrounding environment.
- These vibrations may require additional measures to stabilize the equipment and prevent damage to nearby structures or sensitive equipment.
-
Limited Capacity for Large Quantities:
- Planetary ball mills typically have a limited capacity for handling large quantities of material at once.
- This limitation can be a disadvantage in industrial settings where large-scale production is required.
In summary, while planetary ball mills offer significant advantages in terms of grinding efficiency and particle size reduction, they also come with several disadvantages that need to be carefully considered. These include high energy consumption, significant wear and tear, potential thermal damage to materials, loud noise, and limitations in handling certain types of materials. Additionally, the equipment can be cumbersome, heavy, and may require frequent maintenance, which can impact overall operational efficiency and cost.
Summary Table:
Disadvantage | Description |
---|---|
High Energy Consumption | High operational costs due to energy use and component wear. |
Significant Wear and Tear | Frequent replacement of grinding balls and wall armor increases maintenance. |
Thermal Damage to Materials | Heat generated can alter properties of heat-sensitive materials. |
Loud Noise During Operation | Requires soundproofing or protective measures for operators. |
Material Limitations | Not suitable for soft, tacky, or fibrous materials. |
Contamination Risks | Wear of components can lead to material contamination. |
Cumbersome and Heavy Equipment | Difficult to move or install in limited spaces. |
Slow Process | Grinding can be slower compared to other milling equipment. |
Vibrations | Strong vibrations may require stabilization measures. |
Limited Capacity | Not ideal for large-scale production due to limited material handling capacity. |
Need help choosing the right milling equipment for your needs? Contact us today for expert advice!