RF magnetron sputtering, while advantageous for its ability to deposit thin films on non-conductive materials and its high deposition rates, has several notable disadvantages. These include limitations in the effective coating area, poor bonding strength of the film substrate, and the formation of porous, rough columnar structures. Additionally, the process can cause higher substrate heating and increased structural defects due to intense ion bombardment. Optimizing film properties for specific applications can also be time-consuming due to the numerous control parameters involved. Despite its versatility, these drawbacks must be carefully considered when selecting this technique for thin film deposition.
Key Points Explained:
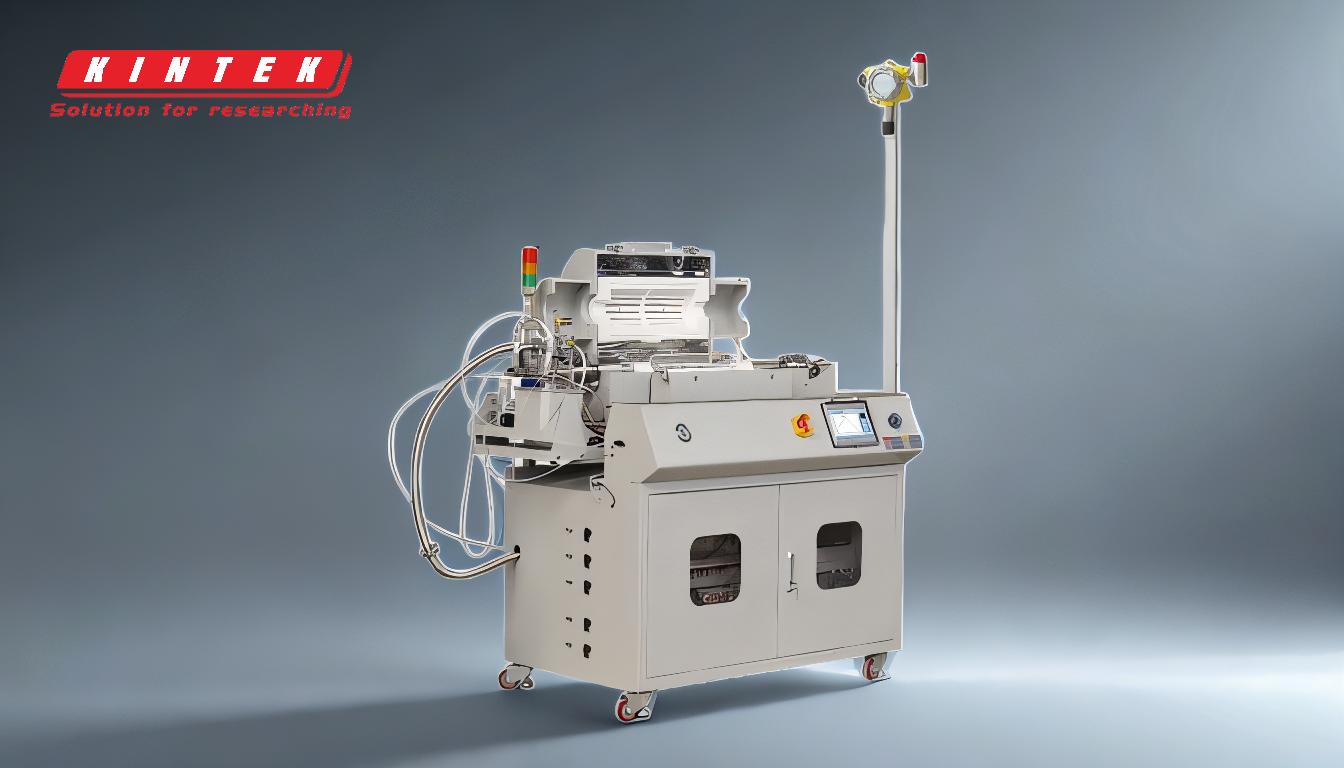
-
Limited Effective Coating Area:
- RF magnetron sputtering has a short effective coating area, which restricts the geometric size of workpieces that can be plated. The plasma concentration decreases rapidly beyond 60 mm from the target surface, limiting where workpieces can be placed. This constraint can be problematic for larger or more complex substrates, as uniform coating becomes challenging.
-
Low Energy of Target Particles:
- The energy of the flying target particles in RF magnetron sputtering is relatively low. This results in poor bonding strength between the film and the substrate, which can compromise the durability and performance of the coated material. Low-energy particles also tend to form porous and rough columnar structures, which may not be desirable for applications requiring smooth and dense films.
-
High Substrate Heating:
- One of the significant drawbacks of RF magnetron sputtering is the higher substrate heating, which can reach up to 250°C. This elevated temperature can be detrimental to heat-sensitive materials, limiting the range of substrates that can be effectively coated. Additionally, high temperatures can lead to thermal stress and deformation in some materials.
-
Increased Structural Defects:
- The intense ion bombardment on the substrate during RF magnetron sputtering can lead to increased structural defects in the deposited films. These defects can negatively impact the mechanical, electrical, and optical properties of the films, making them less suitable for high-performance applications.
-
Complex Optimization Process:
- Optimizing film properties for specific applications can be a complex and time-consuming process in RF magnetron sputtering. The technique involves numerous control parameters, such as power, pressure, and gas composition, which need to be carefully adjusted to achieve the desired film characteristics. This complexity can increase the time and cost associated with process development.
-
Material Limitations:
- While RF magnetron sputtering is advantageous for depositing films on non-conductive materials, it still has limitations in terms of the types of materials that can be effectively coated. Some materials may not withstand the high temperatures or intense ion bombardment involved in the process, limiting their suitability for certain applications.
-
Formation of Porous and Rough Films:
- The low energy of the sputtered particles often results in the formation of porous and rough columnar structures in the deposited films. These structures can have inferior mechanical and optical properties compared to dense and smooth films, which may be a significant disadvantage for applications requiring high-quality coatings.
In summary, while RF magnetron sputtering offers several advantages, such as high deposition rates and the ability to coat non-conductive materials, it also has several disadvantages that must be considered. These include limitations in coating area, poor bonding strength, high substrate heating, increased structural defects, complex optimization processes, material limitations, and the formation of porous and rough films. These factors should be carefully evaluated when selecting RF magnetron sputtering for specific thin film deposition applications.
Summary Table:
Disadvantage | Description |
---|---|
Limited Effective Coating Area | Plasma concentration decreases beyond 60 mm, restricting uniform coating. |
Low Energy of Target Particles | Poor bonding strength and porous, rough columnar structures in films. |
High Substrate Heating | Temperatures up to 250°C can damage heat-sensitive materials. |
Increased Structural Defects | Intense ion bombardment leads to defects in mechanical and optical properties. |
Complex Optimization Process | Time-consuming adjustments of power, pressure, and gas composition required. |
Material Limitations | Some materials cannot withstand high temperatures or ion bombardment. |
Formation of Porous, Rough Films | Films often have inferior mechanical and optical properties. |
Need help choosing the right thin film deposition technique? Contact our experts today for personalized guidance!