Thin film deposition is a critical process in various industries, including electronics, optics, and coatings. However, it comes with several disadvantages and challenges that can affect the quality, performance, and scalability of the final product. These challenges include issues related to uniformity, adhesion, contamination, substrate compatibility, stress management, purity, and cost-effectiveness. Additionally, temperature constraints during deposition and cooling, as well as the difficulty in achieving consistent thickness and purity, further complicate the process. Addressing these disadvantages requires careful optimization and advanced techniques to ensure the desired film properties and performance.
Key Points Explained:
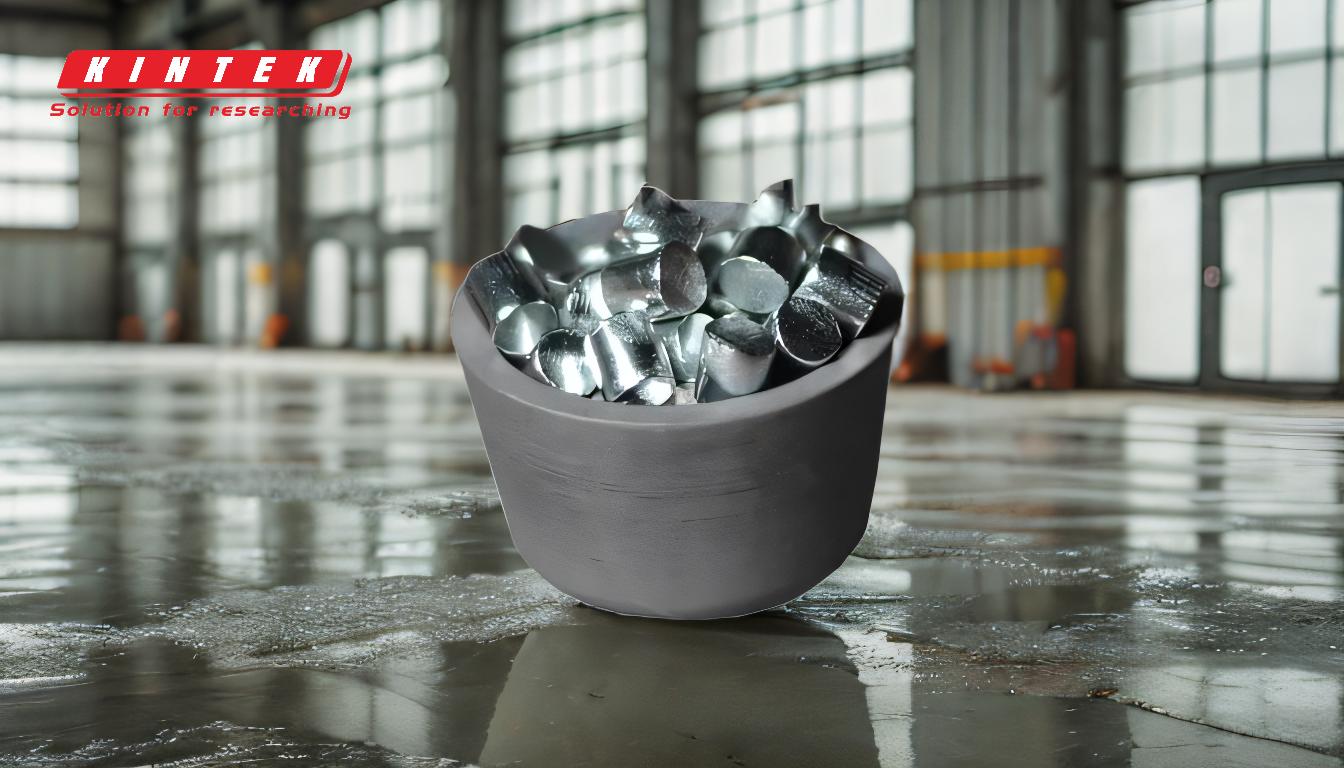
-
Uniformity and Thickness Control:
- Achieving uniform thickness across the entire substrate is a significant challenge in thin film deposition. Non-uniformity can lead to variations in film properties, affecting performance in applications such as electronics and optics.
- Factors contributing to non-uniformity include uneven deposition rates, substrate surface irregularities, and variations in temperature or gas flow during the deposition process.
- Advanced techniques like atomic layer deposition (ALD) and improved process control can help mitigate these issues, but they often come at a higher cost.
-
Adhesion and Delamination:
- Proper adhesion between the thin film and the substrate is crucial for the durability and functionality of the coating. Poor adhesion can result in delamination, where the film peels off from the substrate.
- Delamination is often caused by mismatches in thermal expansion coefficients, surface contamination, or insufficient surface preparation.
- Solutions include surface treatments, such as plasma cleaning or the use of adhesion-promoting layers, to enhance bonding between the film and substrate.
-
Contamination and Purity:
- Contamination during the deposition process can significantly degrade the quality of the thin film. Impurities can alter the electrical, optical, or mechanical properties of the film.
- Sources of contamination include residual gases in the deposition chamber, particles from the substrate, or impurities in the deposition material.
- Maintaining high levels of cleanliness, using ultra-high-purity materials, and implementing strict process controls are essential to minimize contamination.
-
Substrate Compatibility:
- The choice of substrate material is critical, as it must be compatible with the deposition process and the film material. Incompatibility can lead to issues such as poor adhesion, stress-induced cracking, or chemical reactions between the film and substrate.
- For example, high-temperature deposition processes may not be suitable for substrates with low thermal stability.
- Careful selection of substrate materials and deposition conditions is necessary to ensure compatibility and achieve the desired film properties.
-
Stress and Strain Management:
- Thin films often experience internal stresses due to differences in thermal expansion coefficients between the film and substrate, or due to the deposition process itself. These stresses can lead to cracking, buckling, or delamination of the film.
- Stress management techniques include optimizing deposition parameters, such as temperature and pressure, and using stress-relieving layers or annealing processes to reduce residual stresses.
- However, these techniques can add complexity and cost to the deposition process.
-
Temperature Constraints:
- Many thin film deposition processes require elevated temperatures, which can limit the choice of substrate materials and increase the risk of thermal damage.
- For example, high-temperature processes may not be suitable for polymers or other temperature-sensitive materials.
- Low-temperature deposition techniques, such as plasma-enhanced chemical vapor deposition (PECVD), can be used as alternatives, but they may have limitations in terms of film quality and deposition rate.
-
Cooling-Induced Stresses:
- During the cooling phase after deposition, undesirable stresses can develop in the thin film due to differences in thermal contraction between the film and substrate.
- These stresses can lead to defects such as cracks or delamination, compromising the integrity of the film.
- Gradual cooling or post-deposition annealing can help mitigate these stresses, but these steps add time and complexity to the process.
-
Cost and Scalability:
- Thin film deposition processes can be expensive, particularly when advanced techniques or high-purity materials are required. The cost of equipment, maintenance, and process optimization can be a significant barrier, especially for large-scale production.
- Scaling up the deposition process while maintaining consistent film quality is another challenge. Variations in deposition conditions, such as temperature or gas flow, can become more pronounced at larger scales, leading to non-uniformity or defects.
- Balancing cost and scalability requires careful optimization of deposition parameters and the use of cost-effective materials and techniques without compromising film quality.
In conclusion, while thin film deposition is a powerful technology with wide-ranging applications, it is not without its challenges. Addressing issues related to uniformity, adhesion, contamination, substrate compatibility, stress management, and cost-effectiveness is essential to produce high-quality films that meet the demands of modern applications. Advanced techniques and careful process optimization can help overcome these disadvantages, but they often come with increased complexity and cost.
Summary Table:
Challenge | Description | Solution |
---|---|---|
Uniformity & Thickness | Non-uniform thickness affects film performance. | Use advanced techniques like ALD and improved process control. |
Adhesion & Delamination | Poor adhesion causes film peeling. | Apply surface treatments (e.g., plasma cleaning) or adhesion-promoting layers. |
Contamination & Purity | Impurities degrade film quality. | Maintain cleanliness, use ultra-high-purity materials, and strict controls. |
Substrate Compatibility | Incompatible substrates lead to poor adhesion or cracking. | Select compatible materials and optimize deposition conditions. |
Stress & Strain | Internal stresses cause cracking or delamination. | Optimize deposition parameters and use stress-relieving layers or annealing. |
Temperature Constraints | High temperatures limit substrate options. | Use low-temperature techniques like PECVD. |
Cooling-Induced Stresses | Stresses during cooling cause defects. | Implement gradual cooling or post-deposition annealing. |
Cost & Scalability | High costs and scaling challenges affect large-scale production. | Optimize parameters and use cost-effective materials without compromising quality. |
Need help overcoming thin film deposition challenges? Contact our experts today for tailored solutions!