Chemical vapor deposition (CVD) is a widely used technique for depositing thin films and coatings, but it comes with several significant drawbacks. These include challenges in synthesizing multi-component materials due to variations in vapor pressure, nucleation, and growth rates, leading to heterogeneous particle compositions. The process often requires high temperatures, which can cause thermal instability in substrates and limit the types of materials that can be used. Additionally, the chemical precursors required for CVD can be highly toxic, volatile, and dangerous, and the by-products are often toxic and corrosive, making neutralization costly and problematic. The process is also limited by the size of the vacuum chamber, making it difficult to coat larger surfaces, and it cannot be performed on-site, requiring parts to be transported to a coating center. These factors make CVD a complex and sometimes impractical method for certain applications.
Key Points Explained:
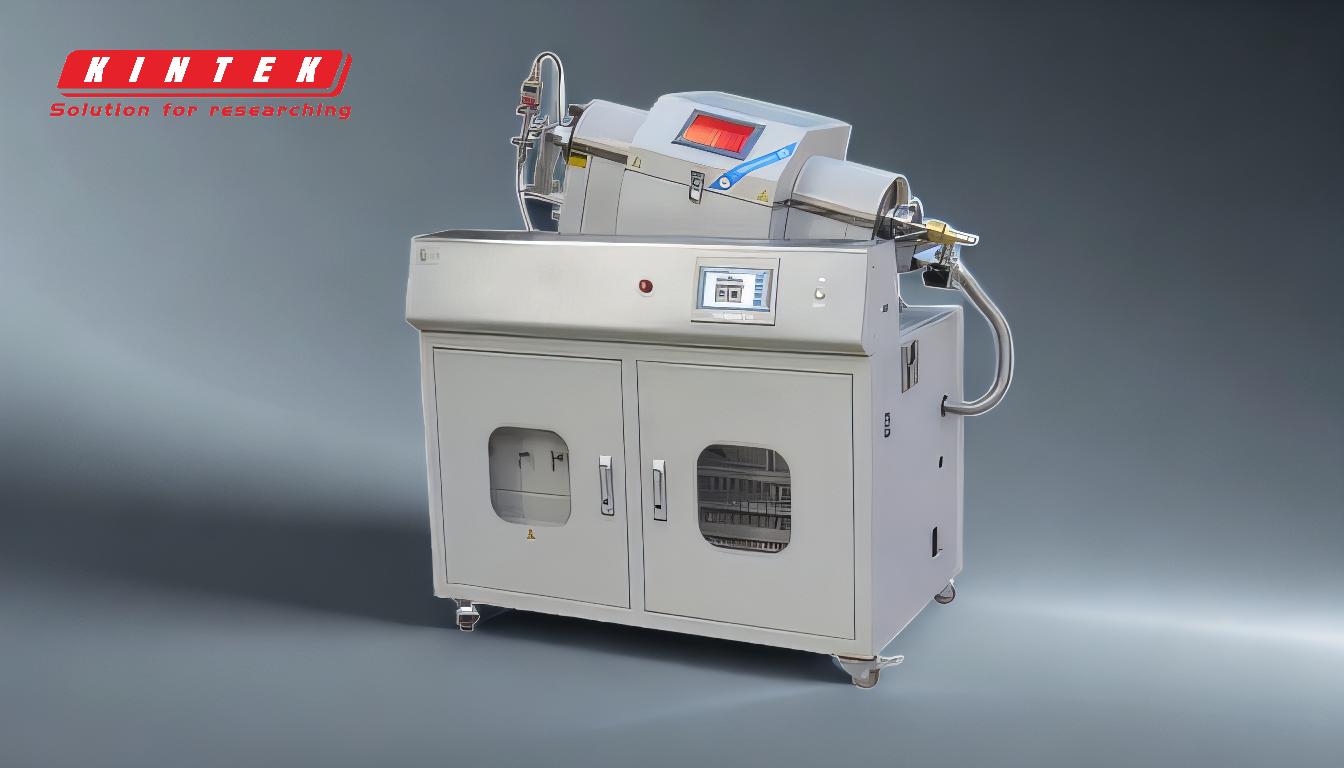
-
Difficulty in Synthesizing Multi-Component Materials:
- CVD faces challenges in creating multi-component materials due to variations in vapor pressure, nucleation, and growth rates during the gas-to-particle conversion. These variations result in a heterogeneous composition of particles, making it difficult to achieve uniform material properties. This is particularly problematic when trying to create materials with specific, well-defined characteristics, as the process can lead to inconsistencies in the final product.
-
High Operating Temperatures:
- CVD typically operates at high temperatures, which can cause thermal instability in many substrates. This limits the types of materials that can be used, as some substrates may degrade or become damaged under these conditions. High temperatures also increase energy consumption and can make the process more expensive and less environmentally friendly.
-
Toxic and Dangerous Precursors:
- The chemical precursors required for CVD often have high vapor pressures and can be highly toxic, volatile, and dangerous. Handling these chemicals requires stringent safety measures, and their use can pose significant health and environmental risks. Additionally, the lack of extremely volatile, nontoxic, and nonpyrophoric precursors further complicates the process, making it less accessible for certain applications.
-
Toxic and Corrosive By-Products:
- The by-products of CVD are often toxic and corrosive, requiring careful neutralization and disposal. This adds to the overall cost and complexity of the process, as specialized equipment and procedures are needed to handle these by-products safely. The environmental impact of these by-products is also a concern, particularly in industries where sustainability is a priority.
-
Limitations in Coating Large Surfaces:
- The size of the vacuum chamber used in CVD limits the size of the surfaces that can be coated. This makes it difficult to apply CVD coatings to large or complex structures, restricting its use in certain industries. Additionally, the process is often "all or nothing," meaning it is challenging to partially coat a material or achieve complete coverage in some cases.
-
Inability to Perform On-Site:
- CVD cannot typically be performed on-site and requires parts to be transported to a coating center. This adds to the logistical complexity and cost of the process, particularly for large or heavy components. The need to break down parts into individual components for coating further complicates the process, making it less efficient for certain applications.
-
Challenges in Producing High-Quality Graphene:
- Producing single-layer graphene using CVD is challenging due to the multiplicity of growth conditions required. Achieving high-quality graphene films requires precise control over the growth mechanism and optimal conditions, which can be difficult to maintain consistently. This limits the scalability and reproducibility of graphene production using CVD.
-
Formation of Hard Aggregates:
- Agglomeration in the gas phase during CVD can lead to the formation of hard aggregates, making it difficult to synthesize high-quality bulk materials. This issue is particularly problematic when trying to create materials with specific mechanical or structural properties, as the presence of aggregates can compromise the integrity of the final product.
In summary, while chemical vapor deposition is a powerful technique for depositing thin films and coatings, it comes with several significant drawbacks that can limit its applicability in certain scenarios. These include challenges in material synthesis, high operating temperatures, the use of toxic precursors, and limitations in coating large surfaces. Understanding these drawbacks is crucial for selecting the appropriate deposition method for a given application.
Summary Table:
Drawback | Description |
---|---|
Difficulty in Multi-Component Synthesis | Variations in vapor pressure and growth rates lead to inconsistent material properties. |
High Operating Temperatures | Thermal instability in substrates and increased energy consumption. |
Toxic and Dangerous Precursors | Requires stringent safety measures and poses health/environmental risks. |
Toxic and Corrosive By-Products | Costly neutralization and disposal processes. |
Limitations in Coating Large Surfaces | Restricted by vacuum chamber size and challenges in partial coating. |
Inability to Perform On-Site | Requires transportation to coating centers, increasing logistical complexity. |
Challenges in Producing High-Quality Graphene | Difficulty in achieving consistent growth conditions for single-layer graphene. |
Formation of Hard Aggregates | Agglomeration in the gas phase compromises material integrity. |
Need help choosing the right deposition method? Contact our experts today for personalized advice!