Sintering is a critical process in material science and manufacturing, particularly for materials with high melting points like metals and ceramics. It involves compacting and forming solid materials by applying heat and pressure below the material's melting point, allowing atoms to diffuse across particle boundaries and fuse together. This process results in enhanced mechanical properties, such as increased strength, hardness, and wear resistance, by creating a dense and cohesive structure. Additionally, sintering improves thermal and electrical conductivity, reduces porosity, and influences grain size and distribution, ultimately leading to superior material performance in various applications, including powder metallurgy and ceramic production.
Key Points Explained:
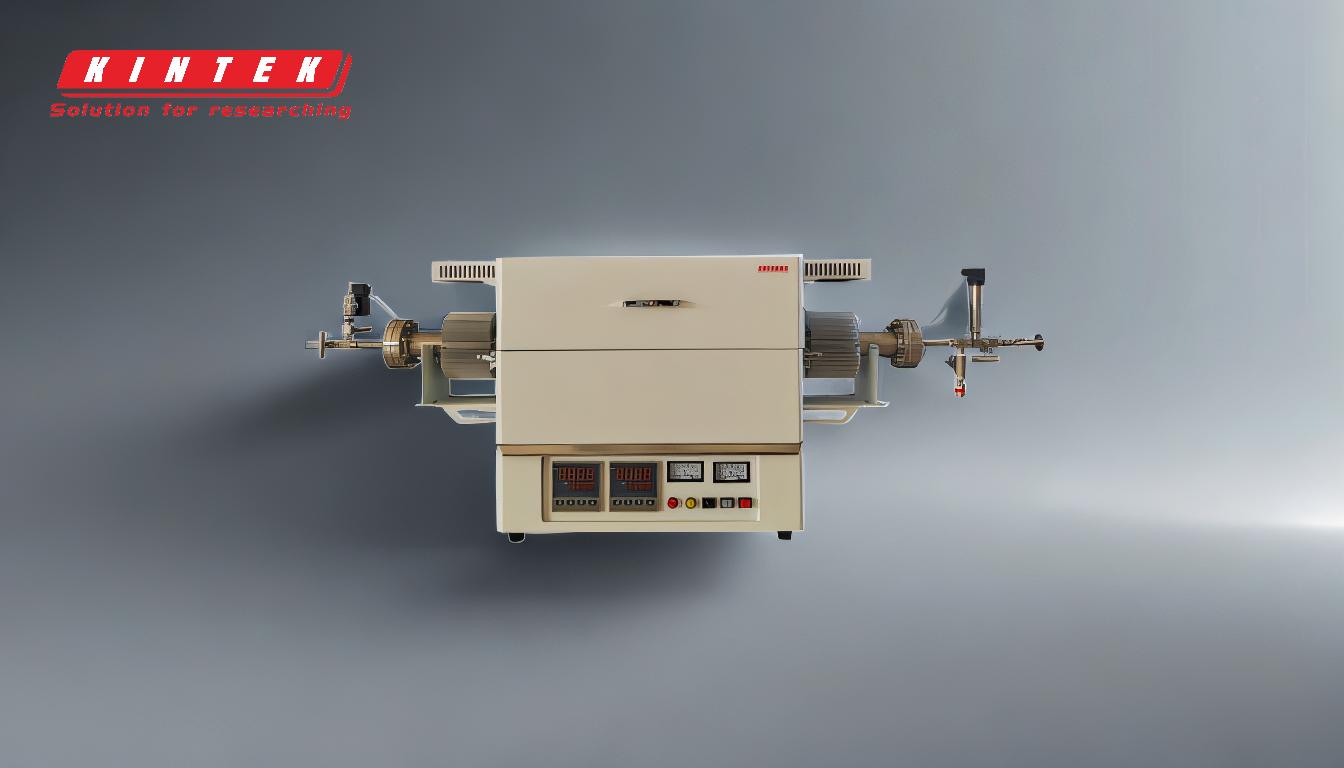
-
Definition and Purpose of Sintering
- Sintering is a process that compacts and forms solid materials by applying heat and pressure below the melting point of the material.
- It is used to transform powdery or fragmented materials into dense, solid bodies, often for materials with high melting points like tungsten, molybdenum, ceramics, and metal powders.
- The primary goal is to create a fully dense part with improved material properties, such as strength, durability, and performance.
-
Mechanism of Sintering
- During sintering, atoms diffuse across the boundaries of particles, fusing them together to form a cohesive solid mass.
- This diffusion occurs due to the application of heat and pressure, which facilitates atomic movement without liquefying the material.
- The process minimizes porous spaces and enhances the overall density of the material.
-
Effects on Mechanical Properties
- Strength and Hardness: Sintering enhances the mechanical properties of materials by creating strong atomic bonds between particles, resulting in increased strength and hardness.
- Wear Resistance: The densification process reduces porosity, making the material more resistant to wear and tear.
- Durability: The cohesive structure formed during sintering improves the material's ability to withstand stress and deformation.
-
Effects on Microstructure
- Grain Size and Distribution: Sintering influences the grain size and distribution in the material's microstructure, which directly affects its mechanical properties. Smaller and more uniformly distributed grains typically result in stronger materials.
- Pore Size and Shape: The process reduces pore size and alters pore shape, leading to a denser and more uniform structure.
- Grain Boundary Shape: The shape and distribution of grain boundaries are modified, contributing to the material's overall integrity and performance.
-
Thermal and Electrical Conductivity
- Sintering improves thermal and electrical conductivity by reducing porosity and creating a more continuous atomic structure.
- This is particularly beneficial for materials used in applications requiring efficient heat or electricity transfer, such as electronic components or heat exchangers.
-
Applications of Sintering
- Powder Metallurgy: Sintering is widely used in powder metallurgy to produce metal components with high strength and durability.
- Ceramic Manufacturing: The process is essential for creating dense and durable ceramic products, such as pottery and advanced ceramics used in industrial applications.
- High-Melting-Point Materials: Sintering is particularly useful for materials like tungsten and molybdenum, which have extremely high melting points and are difficult to process using traditional methods.
-
Advantages of Sintering
- Cost-Effective: Sintering allows for the production of complex shapes and components without the need for expensive melting processes.
- Material Efficiency: The process minimizes material waste by compacting and fusing particles into a solid mass.
- Enhanced Properties: Sintered materials exhibit superior mechanical, thermal, and electrical properties compared to their unsintered counterparts.
-
Limitations and Challenges
- Precision Required: The sintering process requires precise control of temperature, pressure, and time to achieve the desired material properties.
- Material-Specific: Not all materials are suitable for sintering, as the process depends on the material's ability to diffuse and bond at high temperatures.
- Post-Processing: In some cases, additional post-processing steps, such as machining or surface treatment, may be required to achieve the final product specifications.
In summary, sintering is a versatile and essential process in material science and manufacturing, offering significant improvements in material properties and performance. By understanding its effects on microstructure, mechanical properties, and conductivity, manufacturers can optimize the process to produce high-quality components for a wide range of applications.
Summary Table:
Aspect | Impact of Sintering |
---|---|
Mechanical Properties | Increases strength, hardness, wear resistance, and durability. |
Microstructure | Reduces porosity, improves grain size/distribution, and enhances grain boundary shape. |
Conductivity | Improves thermal and electrical conductivity for better performance in heat/electricity transfer. |
Applications | Used in powder metallurgy, ceramic manufacturing, and high-melting-point materials. |
Advantages | Cost-effective, material-efficient, and enhances mechanical, thermal, and electrical properties. |
Want to optimize sintering for your materials? Contact our experts today for tailored solutions!