Grinding operations are influenced by a variety of factors that impact efficiency, particle size, and overall performance. These factors can be broadly categorized into operational parameters, equipment design, and material properties. Key factors include grinding method, feeding speed, media addition, rotation speed, grinding concentration, classifier settings, ball-to-material ratio, and return sand ratio. Additionally, bead size, rotor speed, rotor type, and bead mass are critical in bead mills, while rotation speed, grinding medium size and type, material properties, and mill filling ratio are significant in ball mills. Understanding these factors helps optimize grinding processes for better performance and cost-effectiveness.
Key Points Explained:
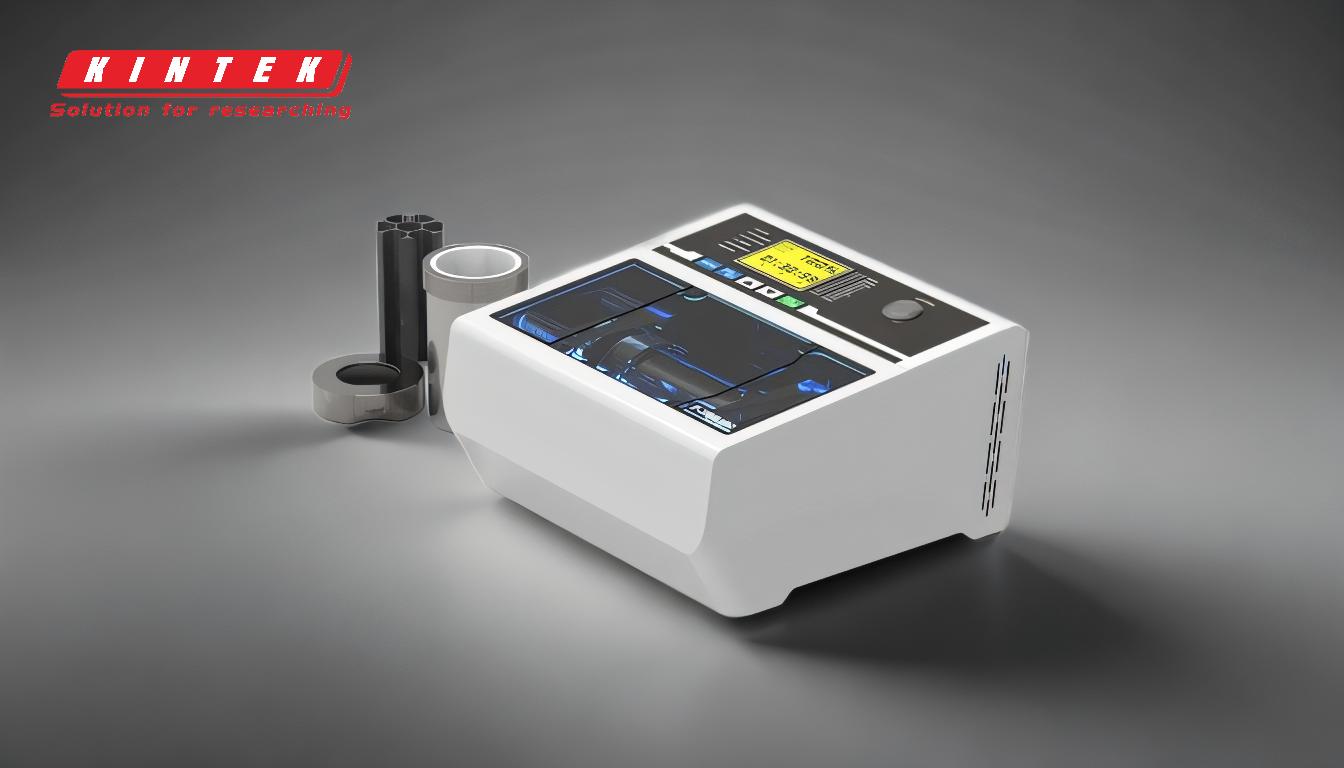
-
Grinding Method
- The choice of grinding method (e.g., dry or wet grinding) significantly impacts the efficiency and outcome of the process. Wet grinding is often preferred for finer particle sizes, while dry grinding is suitable for coarser materials.
- The method also affects energy consumption and equipment wear.
-
Feeding Speed
- The rate at which material is fed into the grinding equipment influences the residence time and grinding efficiency.
- Too high a feeding speed can lead to incomplete grinding, while too low a speed may reduce throughput and increase energy consumption.
-
Media Addition System
- The type, size, and quantity of grinding media (e.g., balls or beads) affect the energy transfer and particle size reduction.
- Proper media selection ensures optimal impact energy and frequency, improving grinding efficiency.
-
Rotation Speed of Grinding Equipment
- The speed at which the grinding equipment rotates determines the kinetic energy imparted to the grinding media.
- Higher speeds increase impact energy but may also lead to excessive wear and heat generation.
-
Grinding Concentration
- The concentration of solids in the grinding slurry affects viscosity and flow dynamics.
- Optimal concentration ensures efficient particle breakage without clogging or excessive energy consumption.
-
Classifier Overflow Concentration and Fineness
- The settings of the classifier (e.g., overflow concentration and fineness) determine the size distribution of the ground particles.
- Proper classifier settings ensure the desired particle size and prevent over-grinding.
-
Ball-to-Material Ratio
- The ratio of grinding media to material influences the grinding efficiency and energy consumption.
- An optimal ratio ensures sufficient impact energy for particle breakage without wasting energy.
-
Return Sand Ratio
- The proportion of coarse particles returned for re-grinding affects the overall efficiency and particle size distribution.
- A balanced return sand ratio ensures consistent grinding performance.
-
Bead Size, Rotor Speed, and Type (for Bead Mills)
- Smaller beads provide more contact points for finer grinding, while larger beads are suitable for coarser materials.
- Rotor speed and type determine the energy transfer and grinding intensity.
-
Mass of Beads Charged in the Mill
- The total mass of beads affects the grinding capacity and energy consumption.
- Proper bead mass ensures efficient grinding without overloading the equipment.
-
Speed of Rotation (for Ball Mills)
- The rotation speed determines the cascading and cataracting action of the grinding media.
- Optimal speed ensures effective particle breakage without excessive wear.
-
Size and Type of Grinding Medium
- Larger grinding media are suitable for coarse grinding, while smaller media are used for fine grinding.
- The type of media (e.g., steel, ceramic) affects wear resistance and grinding efficiency.
-
Size and Type of Material to be Ground
- The hardness, brittleness, and size of the material influence the grinding process.
- Harder materials require higher energy input, while brittle materials are easier to grind.
-
Filling Ratio of the Mill
- The percentage of the mill volume filled with grinding media affects the grinding efficiency.
- An optimal filling ratio ensures sufficient media interaction with the material.
By carefully controlling and optimizing these factors, grinding operations can achieve higher efficiency, better particle size control, and reduced energy consumption.
Summary Table:
Category | Key Factors | Impact |
---|---|---|
Operational Parameters | Grinding method, feeding speed, rotation speed, grinding concentration | Affects efficiency, particle size, and energy consumption |
Equipment Design | Media addition system, classifier settings, ball-to-material ratio, return sand ratio | Influences grinding intensity and particle distribution |
Material Properties | Size and type of material, hardness, brittleness | Determines grinding difficulty and energy requirements |
Bead Mills | Bead size, rotor speed, rotor type, bead mass | Affects grinding precision and capacity |
Ball Mills | Rotation speed, grinding medium size and type, mill filling ratio | Impacts grinding efficiency and wear |
Optimize your grinding process for better performance—contact our experts today!