Milling efficiency is influenced by a variety of factors, including the properties of the material being processed, the operational parameters of the milling equipment, and the supporting measures in place. Key factors include the particle size of the finished product, material hardness, humidity, composition, and viscosity. Additionally, operational factors such as residence time, ball size, density, and number, feed rate, and rotation speed of the mill cylinder play significant roles. Understanding these factors helps in optimizing milling operations for better efficiency and output quality.
Key Points Explained:
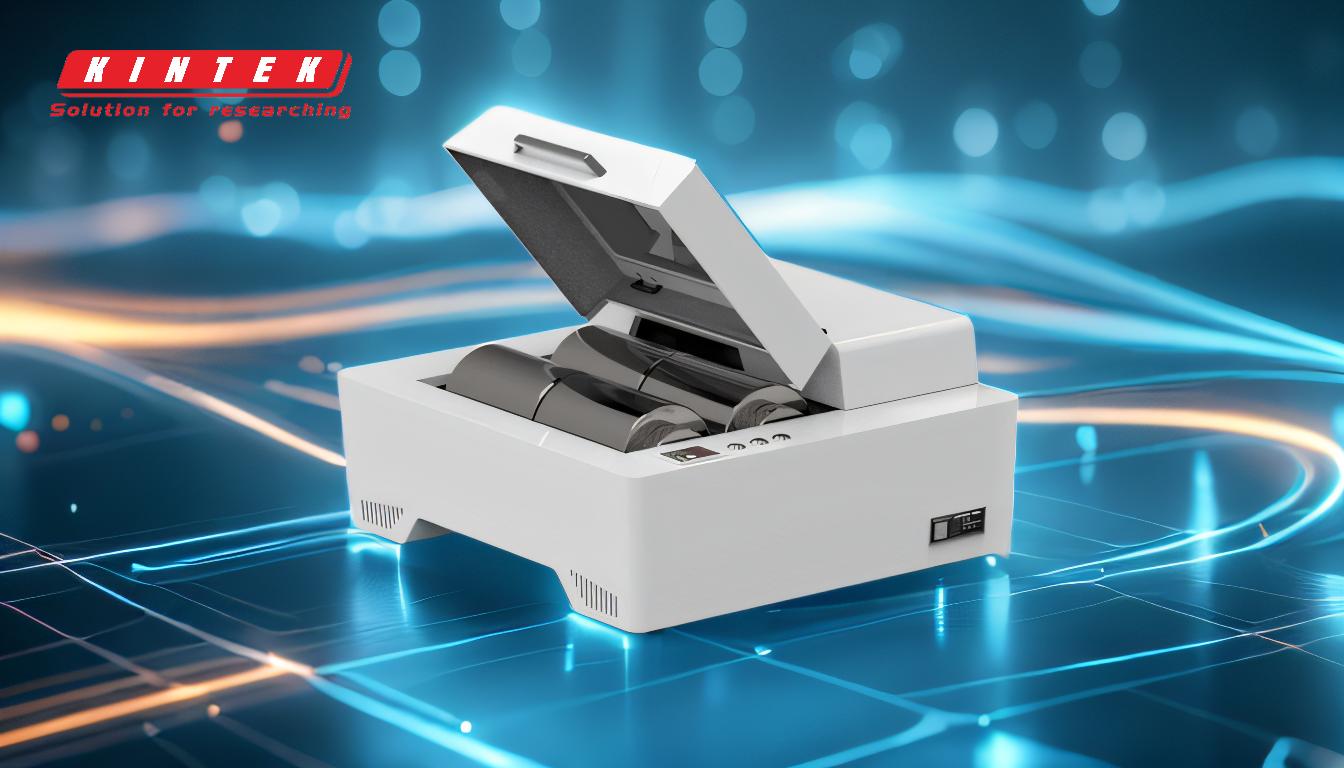
-
Particle Size of the Finished Product
- Explanation: The desired particle size of the final product directly impacts milling efficiency. Finer particles require more energy and time to achieve, which can reduce throughput and increase operational costs.
- Impact: Adjusting the mill settings to achieve the optimal balance between particle size and energy consumption is crucial for efficiency.
-
Hardness of the Material
- Explanation: Harder materials are more resistant to grinding and require more energy to break down. This can lead to increased wear on milling equipment and higher operational costs.
- Impact: Selecting appropriate milling media and optimizing mill parameters for hard materials can help maintain efficiency.
-
Humidity of the Material
- Explanation: Moisture content in the material can affect its flow properties and the milling process. High humidity can lead to clogging and reduced throughput.
- Impact: Pre-drying materials or using mills designed to handle wet materials can mitigate these issues.
-
Composition of the Material
- Explanation: The chemical and physical composition of the material can influence its grindability. Materials with heterogeneous compositions may require different milling strategies.
- Impact: Tailoring the milling process to the specific composition of the material can enhance efficiency.
-
Viscosity of the Material
- Explanation: Viscous materials can be more difficult to mill due to their resistance to flow and tendency to stick to milling surfaces.
- Impact: Using mills with appropriate surface treatments or additives to reduce viscosity can improve milling efficiency.
-
Residence Time in the Mill Chamber
- Explanation: The amount of time material spends in the mill affects the degree of milling. Longer residence times can lead to finer particles but may also increase energy consumption.
- Impact: Optimizing residence time to achieve the desired particle size without excessive energy use is key.
-
Size, Density, and Number of Balls
- Explanation: The characteristics of the milling media (balls) influence the grinding efficiency. Larger or denser balls can provide more impact force but may also increase wear.
- Impact: Selecting the right combination of ball size, density, and number can optimize milling efficiency.
-
Feed Rate and Level in the Vessel
- Explanation: The rate at which material is fed into the mill and the level of material in the mill vessel affect the milling process. Overloading can reduce efficiency, while underloading can lead to insufficient milling.
- Impact: Maintaining an optimal feed rate and material level ensures consistent milling performance.
-
Rotation Speed of the Cylinder
- Explanation: The speed at which the mill cylinder rotates affects the impact and shear forces on the material. Higher speeds can increase milling efficiency but may also lead to increased wear and energy consumption.
- Impact: Adjusting the rotation speed to balance efficiency and wear is important for long-term operational success.
-
Supporting Measures
- Explanation: The efficiency of supporting measures such as cooling systems, dust collection, and material handling systems can impact overall milling efficiency.
- Impact: Ensuring that all supporting systems are functioning optimally can enhance the overall efficiency of the milling operation.
By understanding and addressing these factors, milling operations can be optimized for better efficiency, reduced costs, and improved product quality.
Summary Table:
Factor | Explanation | Impact |
---|---|---|
Particle Size | Desired particle size affects energy and time required. | Balance particle size and energy consumption for efficiency. |
Material Hardness | Harder materials require more energy and cause increased wear. | Optimize milling media and parameters for hard materials. |
Humidity | Moisture affects flow properties and can cause clogging. | Pre-dry materials or use mills designed for wet materials. |
Composition | Chemical and physical properties influence grindability. | Tailor milling process to material composition. |
Viscosity | Viscous materials resist flow and stick to surfaces. | Use surface treatments or additives to reduce viscosity. |
Residence Time | Time in the mill affects particle size and energy use. | Optimize time for desired particle size without excessive energy. |
Ball Size, Density, Number | Milling media characteristics impact grinding efficiency. | Select optimal ball size, density, and number. |
Feed Rate and Level | Overloading or underloading affects milling performance. | Maintain optimal feed rate and material level. |
Rotation Speed | Speed affects impact and shear forces, influencing efficiency and wear. | Adjust speed to balance efficiency and wear. |
Supporting Measures | Cooling, dust collection, and material handling systems impact overall efficiency. | Ensure supporting systems are functioning optimally. |
Ready to optimize your milling operations? Contact our experts today for tailored solutions!