The quality of films formed via sputtering is influenced by a variety of factors, making it a complex process that requires careful control of multiple parameters. Key factors include the choice of target material, the type of gas used, and the process parameters such as ion energy, angle of incidence, and sputtering duration. Additionally, the purity of the target material and the performance of the sputtering system play crucial roles in determining the structural integrity and overall quality of the film. Understanding and optimizing these factors are essential for achieving high-quality thin films with desired properties.
Key Points Explained:
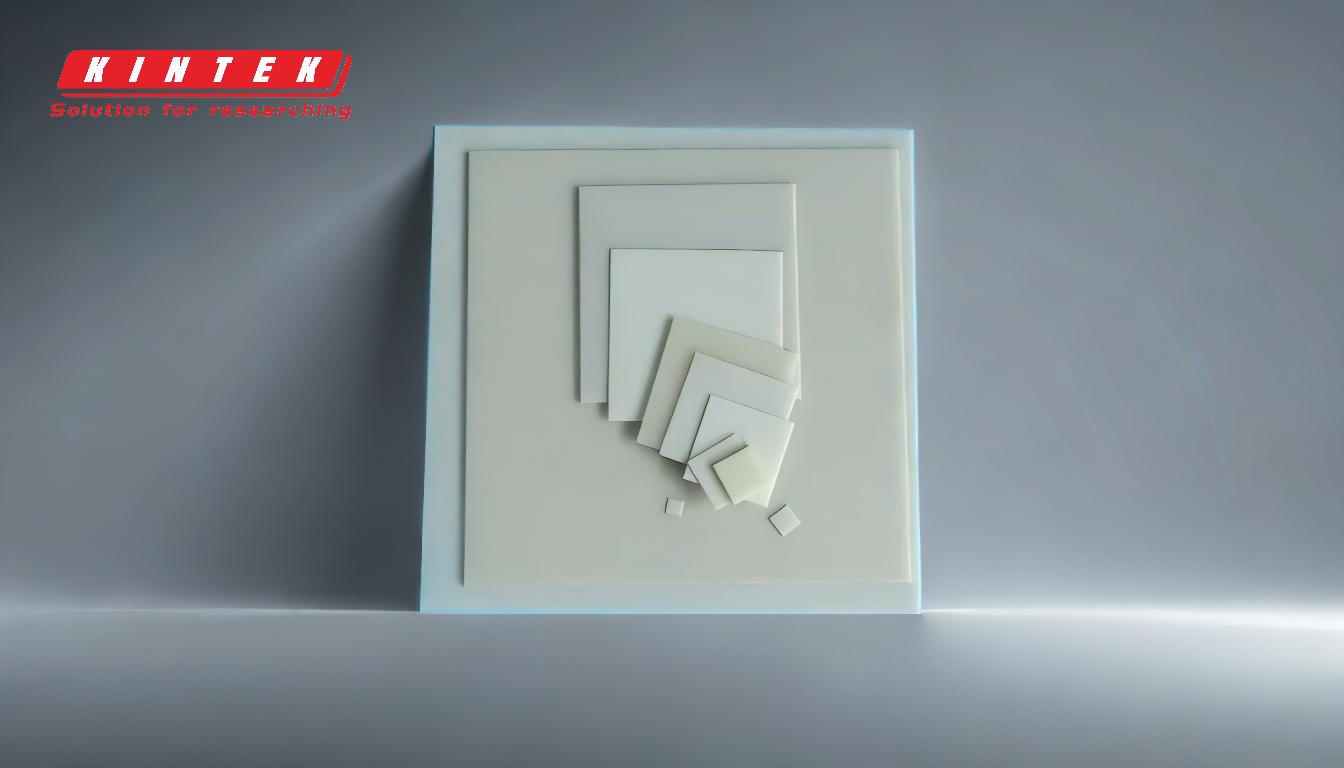
-
Target Material Properties:
- The composition and purity of the target material significantly impact the quality of the sputtered film. Pure metals or alloys used as target materials generally result in films with better structural integrity. Impurities in the target can lead to defects in the film, affecting its mechanical, electrical, and optical properties.
-
Type of Gas Used:
- The choice of sputtering gas, typically an inert gas like argon, influences the sputtering yield and the energy of the sputtered particles. Reactive gases can also be used to form compound films, but the gas type must be carefully selected to avoid unwanted chemical reactions or contamination.
-
Process Parameters:
- Ion Energy: The energy of the incident ions affects the sputtering yield and the energy of the ejected target atoms. Higher ion energy can increase the sputtering rate but may also lead to damage or defects in the film.
- Angle of Incidence: The angle at which ions strike the target affects the distribution and energy of the sputtered particles, influencing the film's uniformity and density.
- Sputtering Duration: The time the sputtering process runs directly affects the film thickness. Longer durations result in thicker films, but the process must be controlled to avoid excessive stress or defects.
-
Sputtering System Performance:
- The design and condition of the sputtering system, including the vacuum quality, power supply stability, and target-to-substrate distance, are critical for consistent film quality. Any instability or contamination in the system can lead to poor film properties.
-
Sputtering Yield:
- The sputtering yield, defined as the number of target atoms ejected per incident ion, depends on factors such as ion mass, target atom mass, and ion energy. Optimizing these factors is essential for achieving the desired film composition and thickness.
-
Film Growth and Microstructure:
- The growth rate and microstructure of the film are influenced by the deposition conditions, including substrate temperature, pressure, and the presence of impurities. Controlling these conditions allows for the formation of films with specific crystalline structures and mechanical properties.
-
Substrate Preparation and Conditions:
- The quality of the substrate, including its cleanliness, temperature, and surface roughness, affects the adhesion and uniformity of the sputtered film. Proper substrate preparation is crucial for achieving high-quality films.
By carefully considering and optimizing these factors, it is possible to produce high-quality thin films with the desired properties for various applications, ranging from electronics to optics and beyond.
Summary Table:
Factor | Impact on Film Quality |
---|---|
Target Material | Purity and composition affect structural integrity, mechanical, and optical properties. |
Type of Gas Used | Inert or reactive gases influence sputtering yield and film composition. |
Ion Energy | Higher energy increases sputtering rate but may cause film defects. |
Angle of Incidence | Affects particle distribution and film uniformity. |
Sputtering Duration | Determines film thickness; excessive duration may cause stress or defects. |
Sputtering System | Vacuum quality, power stability, and target-to-substrate distance impact consistency. |
Substrate Preparation | Cleanliness, temperature, and surface roughness affect film adhesion and uniformity. |
Need help optimizing your sputtering process? Contact our experts today for tailored solutions!