Chemical Vapor Deposition (CVD) is a versatile and widely used technique for depositing thin films and coatings on substrates. The process involves introducing precursor gases into a reaction chamber under controlled conditions of temperature, pressure, and flow rate. These gases undergo chemical reactions, leading to the formation of a solid material that deposits onto the substrate. The process is highly controllable and can produce high-quality, high-performance materials with precise thickness and composition. CVD is used in various industries, including semiconductors, optics, and protective coatings, due to its ability to create uniform and dense layers.
Key Points Explained:
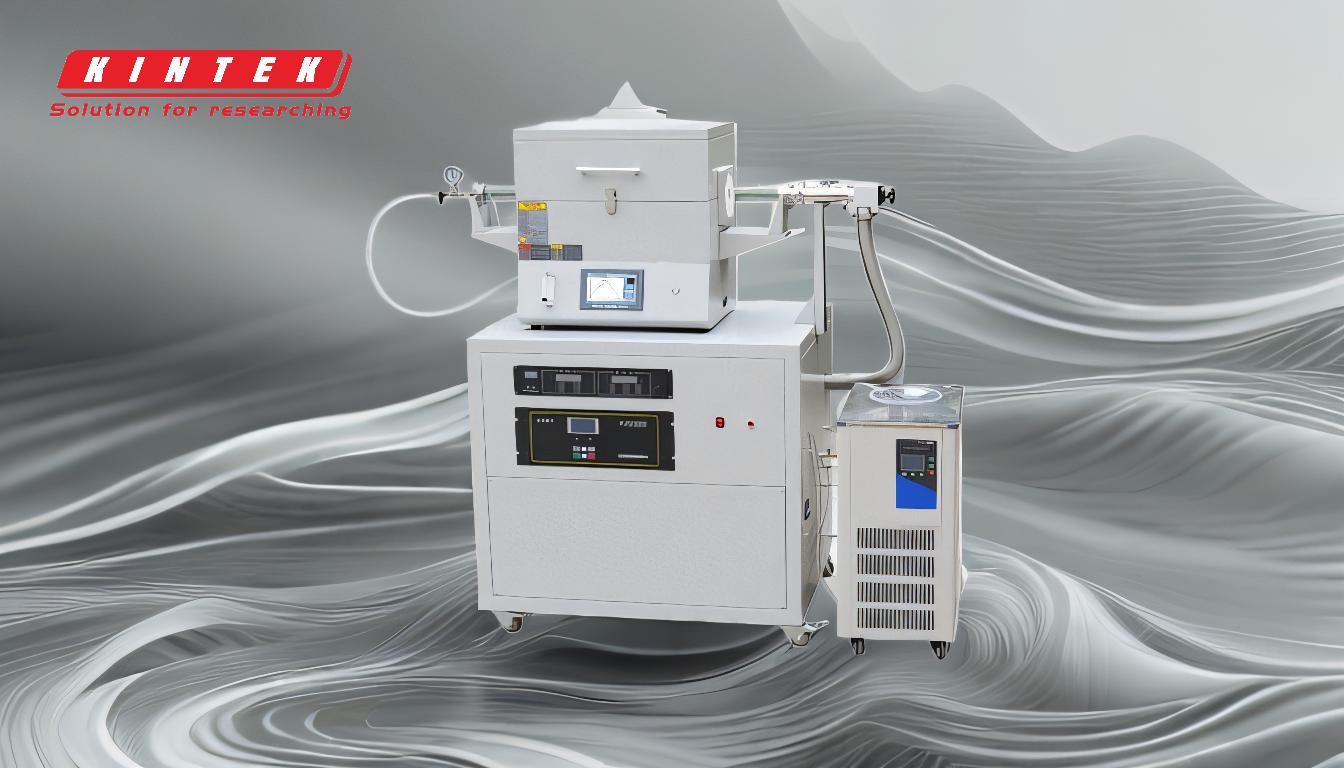
-
Introduction of Precursor Gases:
- CVD begins with the introduction of precursor gases into a reaction chamber. These gases are typically volatile and can be easily vaporized.
- The choice of precursor gases depends on the desired material to be deposited. For example, silane (SiH4) and ammonia (NH3) are used to deposit silicon nitride (Si3N4).
-
Controlled Reaction Conditions:
- The reaction chamber is maintained under controlled conditions of temperature, pressure, and flow rate. These parameters are critical for ensuring the desired chemical reactions occur.
- High temperatures are often required to vaporize the precursor gases and facilitate the chemical reactions. The pressure is usually kept low to prevent unwanted side reactions and to ensure uniform deposition.
-
Chemical Reactions and Decomposition:
- Once inside the reaction chamber, the precursor gases undergo chemical reactions. These reactions can include decomposition, where the precursor molecules break down into smaller components.
- For example, in the deposition of silicon nitride, silane (SiH4) decomposes to form silicon (Si) and hydrogen (H2), which then react with ammonia (NH3) to form silicon nitride (Si3N4).
-
Deposition of Solid Material:
- The products of the chemical reactions deposit onto the substrate, forming a thin, uniform layer. The deposition occurs as the reactive species in the gas phase adsorb onto the substrate surface and undergo further reactions to form a solid film.
- The deposited material can be a single crystal, polycrystalline, or amorphous, depending on the process conditions and the nature of the substrate.
-
Removal of By-products:
- During the CVD process, volatile by-products are often formed. These by-products are removed from the reaction chamber by the flow of gas.
- Efficient removal of by-products is essential to maintain the purity of the deposited film and to prevent contamination.
-
Variations of CVD:
- CVD can be performed using different methods, each with its own advantages and applications. Some common variations include:
- Atmospheric Pressure CVD (APCVD): Performed at atmospheric pressure, suitable for large-area coatings.
- Low-Pressure CVD (LPCVD): Conducted at reduced pressures, providing better control over film thickness and uniformity.
- Plasma-Enhanced CVD (PECVD): Uses plasma to enhance the chemical reactions, allowing deposition at lower temperatures.
- Metal-Organic CVD (MOCVD): Uses metal-organic compounds as precursors, commonly used for depositing compound semiconductors.
- CVD can be performed using different methods, each with its own advantages and applications. Some common variations include:
-
Applications of CVD:
- CVD is used in a wide range of applications, including:
- Semiconductor Manufacturing: For depositing thin films of silicon, silicon dioxide, and other materials used in integrated circuits.
- Optical Coatings: For creating anti-reflective coatings, mirrors, and other optical components.
- Protective Coatings: For applying wear-resistant and corrosion-resistant coatings on tools and components.
- Nanomaterials: For synthesizing carbon nanotubes, graphene, and other nanomaterials.
- CVD is used in a wide range of applications, including:
In summary, CVD is a highly controlled and versatile process that relies on chemical reactions to deposit thin films and coatings on substrates. The process involves the introduction of precursor gases, controlled reaction conditions, chemical decomposition, and the deposition of solid material. Variations of CVD allow for tailored deposition processes to meet specific application requirements. The ability to produce high-quality, uniform films makes CVD an essential technique in many high-tech industries.
Summary Table:
Key Aspect | Description |
---|---|
Precursor Gases | Volatile gases introduced into the reaction chamber (e.g., silane, ammonia). |
Reaction Conditions | Controlled temperature, pressure, and flow rate for precise deposition. |
Chemical Reactions | Decomposition and reaction of gases to form solid materials. |
Deposition | Formation of thin, uniform layers on substrates. |
By-product Removal | Volatile by-products removed to ensure film purity. |
CVD Variations | APCVD, LPCVD, PECVD, MOCVD for tailored applications. |
Applications | Semiconductors, optical coatings, protective coatings, nanomaterials. |
Discover how CVD can revolutionize your material deposition process—contact our experts today!