Induction furnaces, particularly those using IGBT technology, are widely used in metal melting due to their efficiency and precision. However, they come with certain hazards and limitations that users must be aware of. One of the primary drawbacks is their inability to refine materials, meaning the charge materials must be free of oxides and have a known composition. This limitation can lead to the loss of alloying elements due to oxidation, requiring additional steps to re-add these elements to the melt. Understanding these hazards is crucial for safe and effective operation.
Key Points Explained:
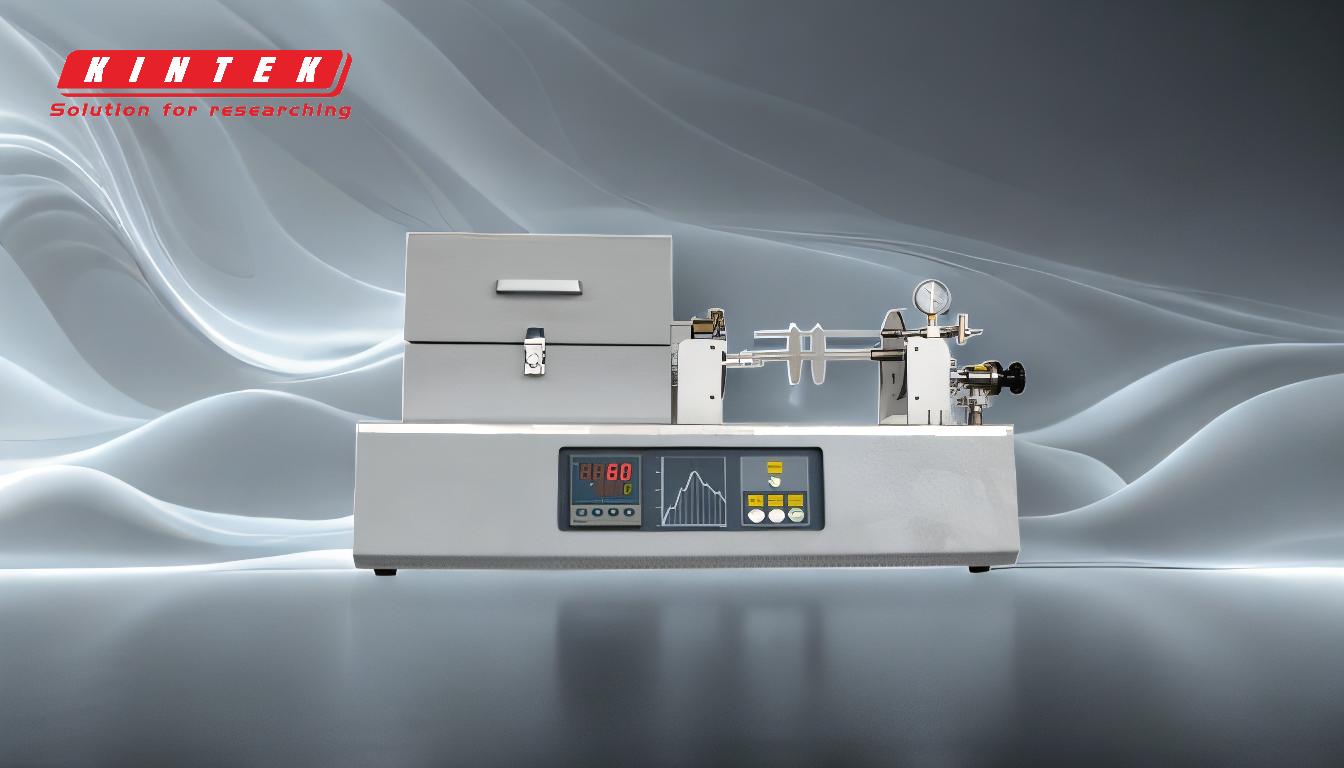
-
Lack of Refining Capacity:
- Induction furnaces, including IGBT induction furnaces, do not have the capability to refine materials. This means that the charge materials used must already be free of oxides and contaminants.
- The absence of refining capacity can lead to impurities in the final product if the initial charge materials are not of high quality.
-
Requirement for Known Composition:
- The composition of the charge materials must be known and consistent. Any variation can affect the quality of the melt.
- This requirement places a significant emphasis on the quality control of raw materials, which can increase operational costs and complexity.
-
Loss of Alloying Elements:
- During the melting process, some alloying elements may be lost due to oxidation. This is particularly problematic for elements that are prone to oxidation.
- To compensate for this loss, these elements must be re-added to the melt, which can complicate the process and increase material costs.
-
Operational Hazards:
- The high temperatures and electromagnetic fields involved in induction melting can pose safety risks to operators if proper precautions are not taken.
- Electrical hazards, including the risk of electric shock, are also a concern, especially in environments where safety protocols are not strictly followed.
-
Maintenance and Wear:
- The components of an induction furnace, such as the crucible and coils, are subject to wear and tear due to the high temperatures and mechanical stresses involved.
- Regular maintenance is required to ensure the longevity and safe operation of the furnace, which can add to the operational costs.
-
Energy Consumption:
- While induction furnaces are generally energy-efficient, the high power requirements for melting metals can still lead to significant energy consumption.
- This can be a concern in regions where energy costs are high or where there are restrictions on energy usage.
In summary, while IGBT induction furnaces offer many advantages in terms of efficiency and precision, they also come with several hazards and limitations. Understanding these factors is essential for anyone involved in the operation or procurement of such equipment. Proper handling, maintenance, and quality control of materials can mitigate many of these risks, ensuring safe and effective operation.
Summary Table:
Hazard/Limitation | Description |
---|---|
Lack of Refining Capacity | Cannot refine materials; charge materials must be free of oxides and contaminants. |
Known Composition Required | Charge materials must have a consistent composition to ensure quality. |
Loss of Alloying Elements | Oxidation during melting can lead to loss of alloying elements, requiring re-addition. |
Operational Hazards | High temperatures and electromagnetic fields pose safety risks to operators. |
Maintenance and Wear | Components like crucibles and coils wear out, requiring regular maintenance. |
Energy Consumption | High power requirements can lead to significant energy usage and costs. |
Ensure safe and efficient operation of your induction furnace—contact our experts today for personalized advice!