Sintering, while offering numerous benefits such as improved material properties and reduced porosity, also presents several hazards and challenges. These include environmental risks from harmful emissions, financial risks due to high initial investment costs, and safety concerns related to handling high-temperature materials. Additionally, the complexity of sintering certain materials and the need for precise control over process parameters can lead to potential issues in material properties and porosity. Understanding these hazards is crucial for mitigating risks and ensuring a safe and efficient sintering process.
Key Points Explained:
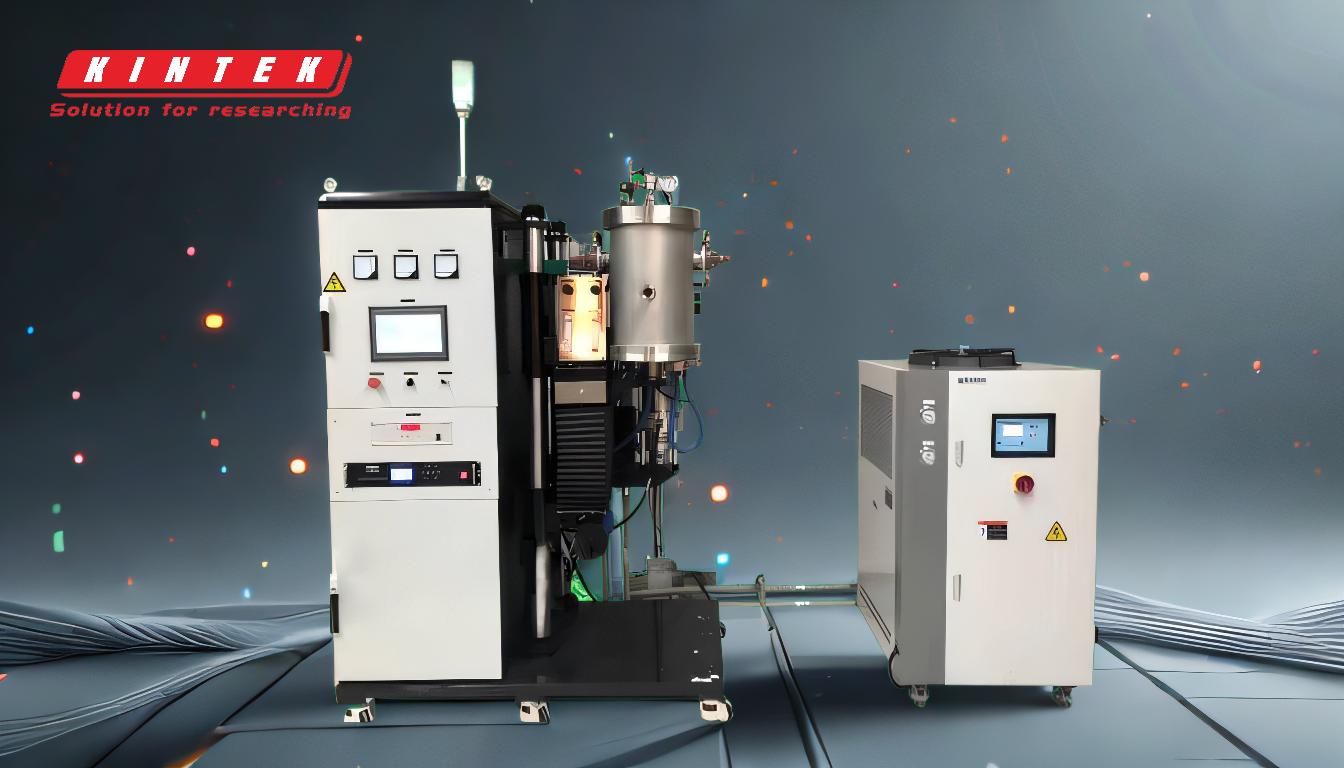
-
Environmental Hazards:
- Sintering involves processing materials at high temperatures, which can release harmful emissions into the environment. These emissions may include particulate matter, volatile organic compounds (VOCs), and other pollutants that can have adverse effects on air quality and human health.
- Governments have implemented various norms and policies to regulate these emissions, which can impact the production rate and operational flexibility of sintering facilities. Compliance with these regulations often requires additional investment in emission control technologies, adding to the overall cost of production.
-
Financial Risks:
- The initial investment required to establish a sintering production line is substantial. This includes the cost of purchasing and installing sintering furnaces, debinding equipment, and other necessary infrastructure.
- If the sintered products do not sell as expected, the high initial investment can lead to significant financial losses. This risk is particularly acute in industries with fluctuating demand or intense competition.
-
Safety Concerns:
- Sintering involves handling materials at high temperatures, which poses inherent safety risks. Proper tools and safety equipment are essential to prevent accidents and injuries during the transportation and pouring of molten materials.
- The use of personal protective equipment (PPE), such as heat-resistant gloves, face shields, and protective clothing, is crucial to ensure the safety of workers involved in the sintering process.
-
Material and Process Complexity:
- Sintering certain composite materials can be complex and requires precise control over process parameters such as temperature, pressure, and sintering time. Any deviation from the optimal conditions can result in defects such as incomplete sintering, excessive porosity, or inhomogeneous material properties.
- The complexity of sintering also extends to the need for careful selection and preparation of raw materials, as well as the design of the sintering furnace and insulation to achieve the desired material properties.
-
Porosity Control:
- One of the primary goals of sintering is to reduce porosity and enhance material properties such as strength, electrical conductivity, and thermal conductivity. However, achieving the desired level of porosity can be challenging, especially in materials with complex geometries or varying particle sizes.
- In some applications, such as filters or catalysts, it may be necessary to maintain a certain level of porosity to ensure gas permeability while still achieving the required mechanical strength.
-
Regulatory Compliance:
- The sintering process is subject to various environmental and safety regulations that can affect production rates and operational costs. Compliance with these regulations requires ongoing monitoring and investment in pollution control technologies, which can add to the overall cost of production.
- Failure to comply with regulatory requirements can result in fines, legal action, and damage to the company's reputation, further increasing the financial risks associated with sintering.
In summary, while sintering offers significant benefits in terms of material properties and performance, it also presents several hazards and challenges that must be carefully managed. These include environmental risks, financial risks, safety concerns, material and process complexity, porosity control, and regulatory compliance. By understanding and addressing these hazards, manufacturers can mitigate risks and ensure a safe and efficient sintering process.
Summary Table:
Hazard Type | Key Challenges |
---|---|
Environmental Hazards | Harmful emissions, regulatory compliance, and high costs for pollution control. |
Financial Risks | High initial investment, potential losses if products underperform. |
Safety Concerns | Handling high-temperature materials, requiring PPE and proper safety protocols. |
Material Complexity | Precise control of temperature, pressure, and time to avoid defects. |
Porosity Control | Balancing porosity for material properties while ensuring gas permeability. |
Regulatory Compliance | Ongoing monitoring and investment to meet environmental and safety standards. |
Need help managing sintering hazards? Contact our experts today for tailored solutions!