Pyrolysis, a thermal decomposition process that occurs in the absence of oxygen, requires efficient and reliable heat sources to achieve the desired chemical reactions. The heat sources for pyrolysis can vary depending on the scale, type of feedstock, and desired end products. Common heat sources include hot flue gas, combustible gases, leftover char, and biomass. Additionally, heat can be supplied through direct or indirect heat exchange methods, such as using solid heat carriers, hot gas streams, or reactor walls. Understanding these heat sources is crucial for optimizing pyrolysis processes, ensuring energy efficiency, and achieving high-quality outputs.
Key Points Explained:
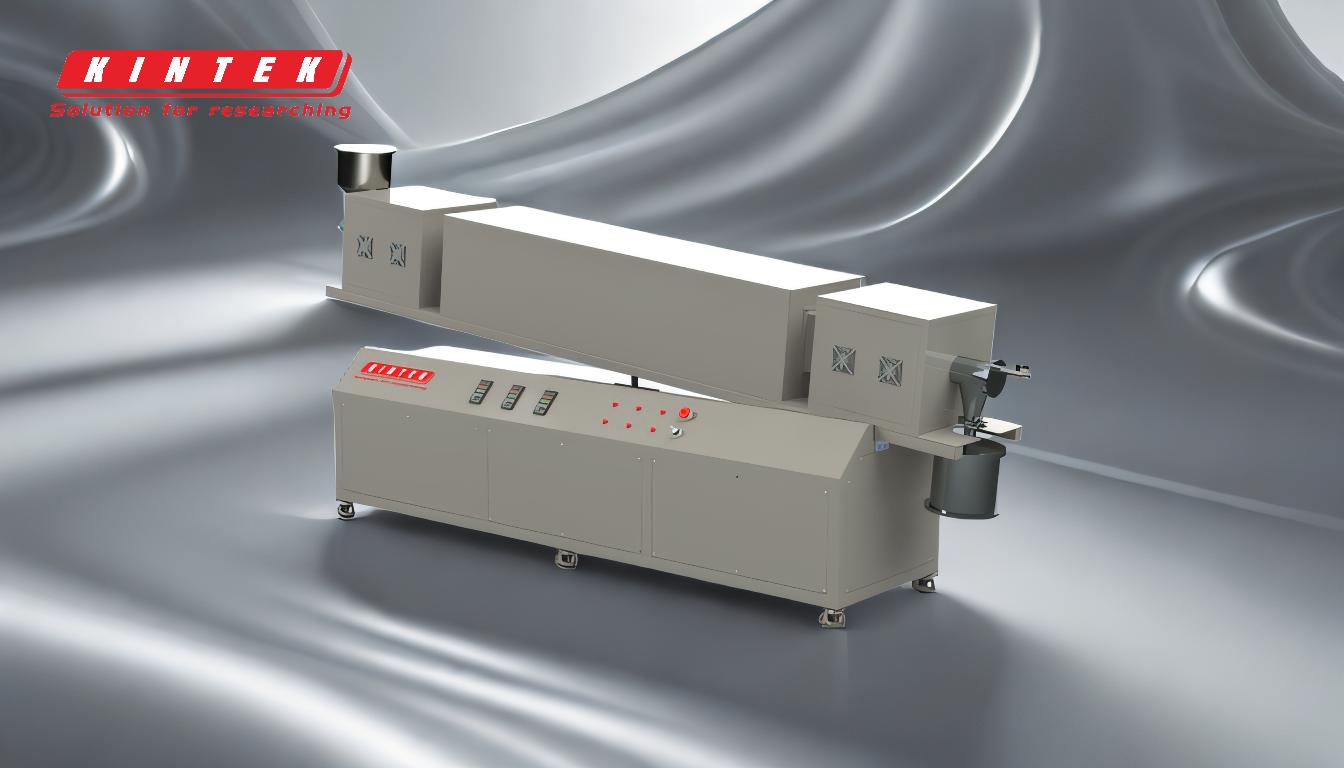
-
Hot Flue Gas as a Heat Source
- Hot flue gas is a widely used heat source in pyrolysis processes. It is primarily utilized to dry the feedstock before pyrolysis begins.
- Flue gas often contains combustible components, which can be partially combusted to generate additional heat. This dual-purpose use of flue gas enhances energy efficiency and reduces waste.
- The use of flue gas is particularly common in industrial-scale pyrolysis systems, where continuous heat supply is essential for maintaining process stability.
-
Combustible Gases and Partial Combustion
- Combustible gases, such as those produced during pyrolysis (e.g., syngas), can be partially combusted to provide heat for the process.
- This method is advantageous because it utilizes byproducts of the pyrolysis reaction, reducing the need for external energy sources and improving overall process sustainability.
- Partial combustion is often integrated into the pyrolysis reactor design, allowing for precise control over temperature and reaction conditions.
-
Leftover Char and Biomass as Heat Sources
- Leftover char, a solid residue from pyrolysis, can be burned to generate heat. This is particularly useful in batch processes or smaller-scale operations.
- Biomass itself can also serve as a heat source. In some systems, a portion of the biomass feedstock is burned to provide the necessary thermal energy for pyrolysis.
- This approach is commonly seen in traditional charcoal kilns, where part of the biomass is combusted with controlled air admission to sustain the pyrolysis reaction.
-
Direct and Indirect Heat Exchange Methods
- Direct Heat Exchange: This method involves transferring heat directly to the feedstock using a solid heat carrier (e.g., sand) or a hot gas stream. Direct heat exchange is ideal for fast pyrolysis processes, where rapid heating is required to maximize gas or liquid yields.
- Indirect Heat Exchange: Heat is transferred indirectly through the reactor wall or built-in tubes/plates. This method is suitable for processes requiring precise temperature control and is often used in industrial-scale pyrolysis systems.
- Both methods have their advantages, with direct heat exchange being more efficient for fast heating and indirect heat exchange offering better control over reaction conditions.
-
Industrial Heat Supply Methods
- Batchwise Treatment: In batch processes, heat is generated by burning part of the biomass with controlled air admission. This method is commonly used in traditional charcoal production.
- Inert Combustion Gases: Industrial processes often use inert combustion gases in the absence of oxygen to achieve continuous and efficient heat supply. This method is highly efficient and suitable for large-scale operations.
- Inert Solid Materials: Processes using inert solid materials (e.g., sand) as energy carriers are ideal for fast pyrolysis, where rapid heating is necessary to produce high yields of gas or liquid products.
-
Partial Combustion Inside the Reactor
- Partial combustion within the reactor is another method for supplying heat. This involves burning a small portion of the feedstock or pyrolysis byproducts inside the reactor to maintain the required temperature.
- This method is particularly useful in systems where external heat sources are limited or impractical, as it leverages the internal energy of the process itself.
By carefully selecting and optimizing heat sources, pyrolysis processes can be tailored to meet specific production goals, whether for biochar, bio-oil, or syngas. The choice of heat source depends on factors such as feedstock type, desired product yields, and process scale, making it a critical consideration for pyrolysis system design and operation.
Summary Table:
Heat Source | Key Features | Applications |
---|---|---|
Hot Flue Gas | Dries feedstock, contains combustible components, enhances energy efficiency | Industrial-scale pyrolysis, continuous heat supply |
Combustible Gases | Utilizes pyrolysis byproducts, reduces external energy needs, precise control | Integrated reactor designs, sustainable pyrolysis processes |
Leftover Char & Biomass | Burns char/biomass for heat, useful in batch/small-scale operations | Traditional charcoal kilns, batch pyrolysis systems |
Direct Heat Exchange | Rapid heating, uses solid heat carriers or hot gas streams | Fast pyrolysis, maximizes gas/liquid yields |
Indirect Heat Exchange | Precise temperature control, heat transfer through reactor walls/tubes/plates | Industrial-scale pyrolysis, controlled reaction conditions |
Partial Combustion | Burns feedstock/byproducts inside reactor, leverages internal energy | Systems with limited external heat sources, self-sustaining pyrolysis processes |
Ready to optimize your pyrolysis process? Contact us today for expert guidance and tailored solutions!