Rubber compounding involves a variety of ingredients that work together to achieve desired properties in the final rubber product. These ingredients include curing agents, accelerators, vulcanization activators, antioxidants, plasticizers, fillers, and special additives like blowing agents and dyes. Each component plays a specific role in enhancing the physical, chemical, and mechanical properties of rubber, such as elasticity, durability, and resistance to environmental factors. Understanding these ingredients is crucial for optimizing rubber formulations for specific applications.
Key Points Explained:
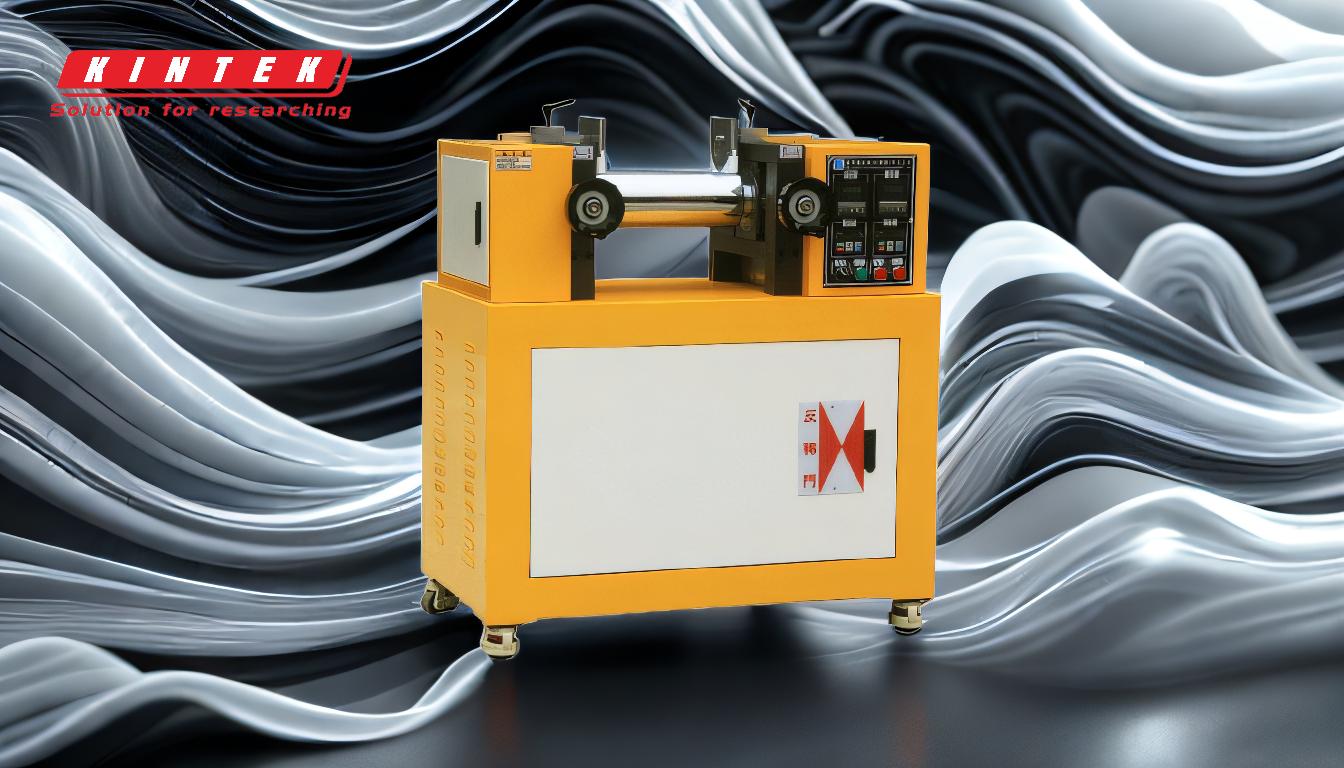
-
Curing Agents:
- Role: Curing agents, also known as vulcanizing agents, are essential for the vulcanization process, which transforms raw rubber into a durable, elastic material.
- Common Types: Sulfur is the most widely used curing agent, but peroxides and metal oxides are also used depending on the type of rubber and desired properties.
- Function: They create cross-links between polymer chains, improving the rubber's strength, elasticity, and resistance to heat and chemicals.
-
Accelerators and Vulcanization Activators:
- Role: Accelerators speed up the vulcanization process, making it more efficient, while activators enhance the effectiveness of accelerators.
- Common Types: Thiazoles, sulfenamides, and guanidines are common accelerators. Zinc oxide and stearic acid are typical activators.
- Function: They reduce the time and temperature required for vulcanization, ensuring a more uniform and controlled curing process.
-
Antioxidants:
- Role: Antioxidants protect rubber from degradation caused by oxidation, which can lead to cracking, hardening, and loss of elasticity.
- Common Types: Amines, phenols, and phosphites are commonly used antioxidants.
- Function: They inhibit the oxidation process, extending the lifespan of rubber products, especially those exposed to heat, light, and oxygen.
-
Plasticizers:
- Role: Plasticizers are added to improve the flexibility, workability, and processability of rubber.
- Common Types: Oils, esters, and phthalates are typical plasticizers.
- Function: They reduce the viscosity of the rubber compound, making it easier to mix and mold, and also enhance the rubber's low-temperature flexibility.
-
Fillers:
- Role: Fillers are used to reinforce rubber, improve its mechanical properties, and reduce costs.
- Common Types: Carbon black and silica are the most common fillers. Other fillers include clay, calcium carbonate, and talc.
- Function: They increase the tensile strength, abrasion resistance, and hardness of rubber, while also reducing material costs by replacing more expensive rubber polymers.
-
Special Additives:
-
Blowing Agents:
- Role: Blowing agents are used to create foam or cellular structures in rubber products.
- Common Types: Chemical blowing agents like azodicarbonamide and physical blowing agents like nitrogen or carbon dioxide.
- Function: They generate gas during the vulcanization process, creating a lightweight, porous structure in the rubber.
-
Dyes and Pigments:
- Role: Dyes and pigments are used to color rubber products.
- Common Types: Organic and inorganic pigments, as well as dyes, are used depending on the desired color and application.
- Function: They provide aesthetic appeal and can also serve functional purposes, such as UV protection or identification.
-
Blowing Agents:
-
Other Additives:
- Role: Various other additives may be included to achieve specific properties or meet regulatory requirements.
- Common Types: Flame retardants, antiozonants, and processing aids are examples.
- Function: They enhance specific properties like fire resistance, ozone resistance, or ease of processing, depending on the application.
Understanding the role and interaction of these ingredients is crucial for formulating rubber compounds that meet specific performance criteria. Each ingredient must be carefully selected and balanced to achieve the desired properties in the final product, whether it's for automotive tires, industrial seals, or consumer goods.
Summary Table:
Ingredient | Role | Common Types | Function |
---|---|---|---|
Curing Agents | Essential for vulcanization, transforming raw rubber into durable material | Sulfur, peroxides, metal oxides | Create cross-links, improving strength, elasticity, and heat/chemical resistance |
Accelerators/Activators | Speed up vulcanization and enhance accelerator effectiveness | Thiazoles, sulfenamides, guanidines; zinc oxide, stearic acid | Reduce time and temperature for uniform curing |
Antioxidants | Protect rubber from oxidation-induced degradation | Amines, phenols, phosphites | Extend rubber lifespan by inhibiting oxidation |
Plasticizers | Improve flexibility, workability, and processability | Oils, esters, phthalates | Reduce viscosity, enhance low-temperature flexibility |
Fillers | Reinforce rubber, improve mechanical properties, reduce costs | Carbon black, silica, clay, calcium carbonate, talc | Increase tensile strength, abrasion resistance, and hardness |
Special Additives | Create foam or color rubber products | Blowing agents (azodicarbonamide, nitrogen); dyes/pigments (organic, inorganic) | Generate gas for lightweight structures or add aesthetic/functional colors |
Other Additives | Enhance specific properties or meet regulatory requirements | Flame retardants, antiozonants, processing aids | Improve fire resistance, ozone resistance, or ease of processing |
Need help optimizing your rubber formulations? Contact our experts today for tailored solutions!