Induction furnaces, while highly efficient for melting metals, have several limitations that can impact their usability in certain industrial applications. The primary drawback is their inability to refine materials, meaning the charge materials must already be free of oxides and have a known composition. Additionally, some alloying elements may be lost due to oxidation, necessitating their re-addition to the melt. These factors can increase operational complexity and costs, particularly in processes requiring precise alloy compositions.
Key Points Explained:
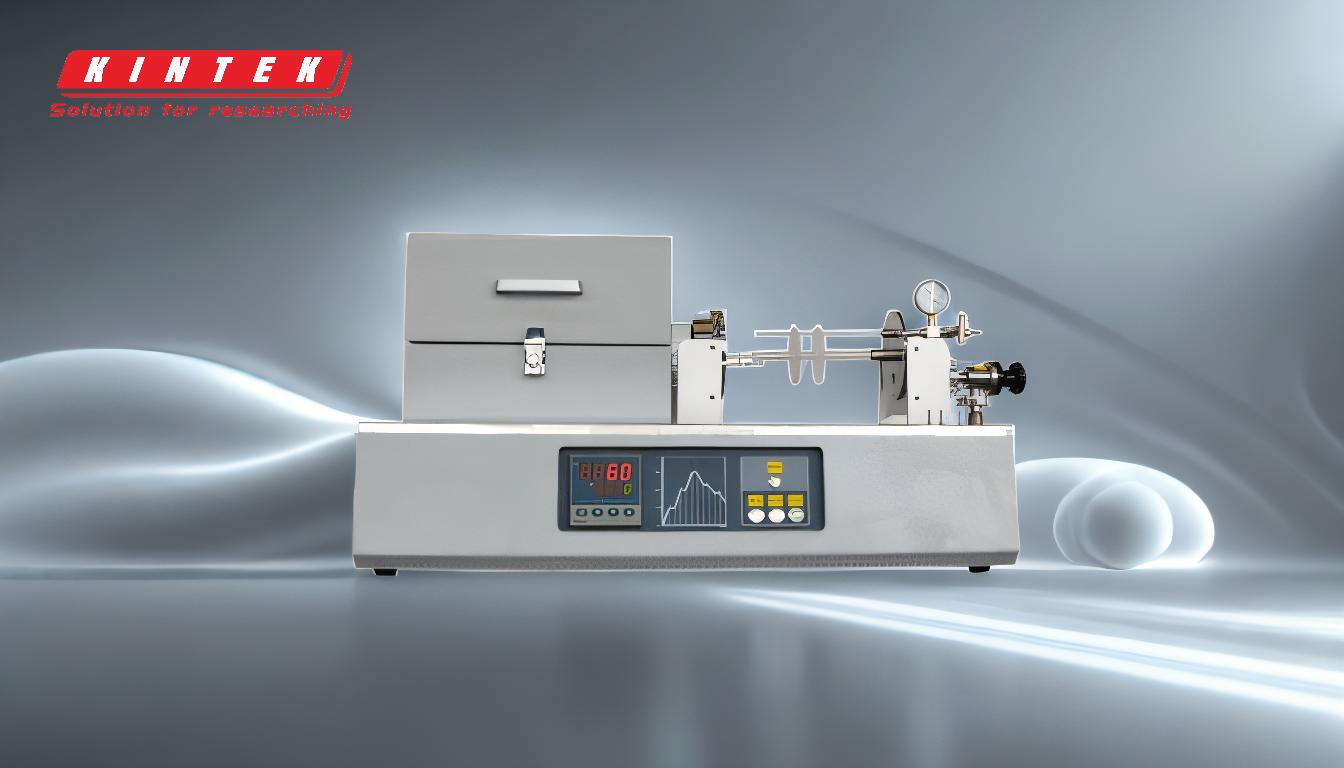
-
Lack of Refining Capacity:
- Induction furnaces cannot refine the metal during the melting process. This means that the raw materials used must already be of high purity and free from oxides. Any impurities present in the charge materials will remain in the final product, which can be a significant limitation for applications requiring high-purity metals.
-
Requirement for Known Composition:
- The composition of the charge materials must be precisely known before melting. This is because the induction furnace does not have the capability to adjust the composition during the melting process. Any deviation in the composition can lead to inconsistencies in the final product, which can be problematic for industries that require strict adherence to material specifications.
-
Loss of Alloying Elements:
- During the melting process, some alloying elements can be lost due to oxidation. This is particularly true for elements that are more reactive and prone to oxidation. The loss of these elements can alter the desired properties of the alloy, requiring them to be re-added to the melt. This not only increases the complexity of the process but also adds to the overall cost.
-
Operational Complexity and Costs:
- The need for high-purity charge materials and the potential loss of alloying elements can lead to increased operational complexity and costs. Industries may need to invest in additional processes or materials to ensure the quality and consistency of the final product. This can make induction furnaces less attractive for certain applications where cost and simplicity are critical factors.
-
Energy Efficiency and Environmental Considerations:
- While induction furnaces are generally energy-efficient, the need for high-purity materials and the potential for material loss can offset some of these benefits. Additionally, the re-addition of lost alloying elements can have environmental implications, particularly if these elements are hazardous or difficult to source.
-
Comparison with Other Furnace Types:
- When compared to other types of furnaces, such as igbt induction furnace, the limitations of induction furnaces become more apparent. For example, IGBT induction furnaces offer better control over the melting process and can handle a wider range of materials, making them more versatile in certain industrial applications.
In summary, while induction furnaces offer several advantages, such as energy efficiency and precise temperature control, their limitations in refining capacity, material composition requirements, and potential loss of alloying elements can pose significant challenges. These factors must be carefully considered when selecting a furnace type for specific industrial applications.
Summary Table:
Limitation | Description |
---|---|
Lack of Refining Capacity | Cannot refine metals; requires high-purity, oxide-free charge materials. |
Known Composition Requirement | Charge material composition must be precisely known before melting. |
Loss of Alloying Elements | Reactive elements may oxidize and require re-addition, increasing costs. |
Operational Complexity & Costs | High-purity materials and re-addition processes increase operational complexity. |
Energy & Environmental Impact | Material loss and re-addition can offset energy efficiency and raise costs. |
Need help choosing the right furnace for your industrial needs? Contact our experts today!