Physical vapor deposition (PVD) is a widely used technique for applying thin-film coatings, offering benefits such as enhanced durability, corrosion resistance, and environmental friendliness. However, it also has several limitations that can affect its suitability for certain applications. These limitations include higher costs compared to other deposition methods, slower operating rates, and constraints related to its "line of sight" nature, which limits its ability to coat complex geometries. Additionally, PVD requires specialized equipment and skilled operators, further increasing costs and complexity. While PVD offers many advantages, these drawbacks must be carefully considered when selecting a coating method for specific applications.
Key Points Explained:
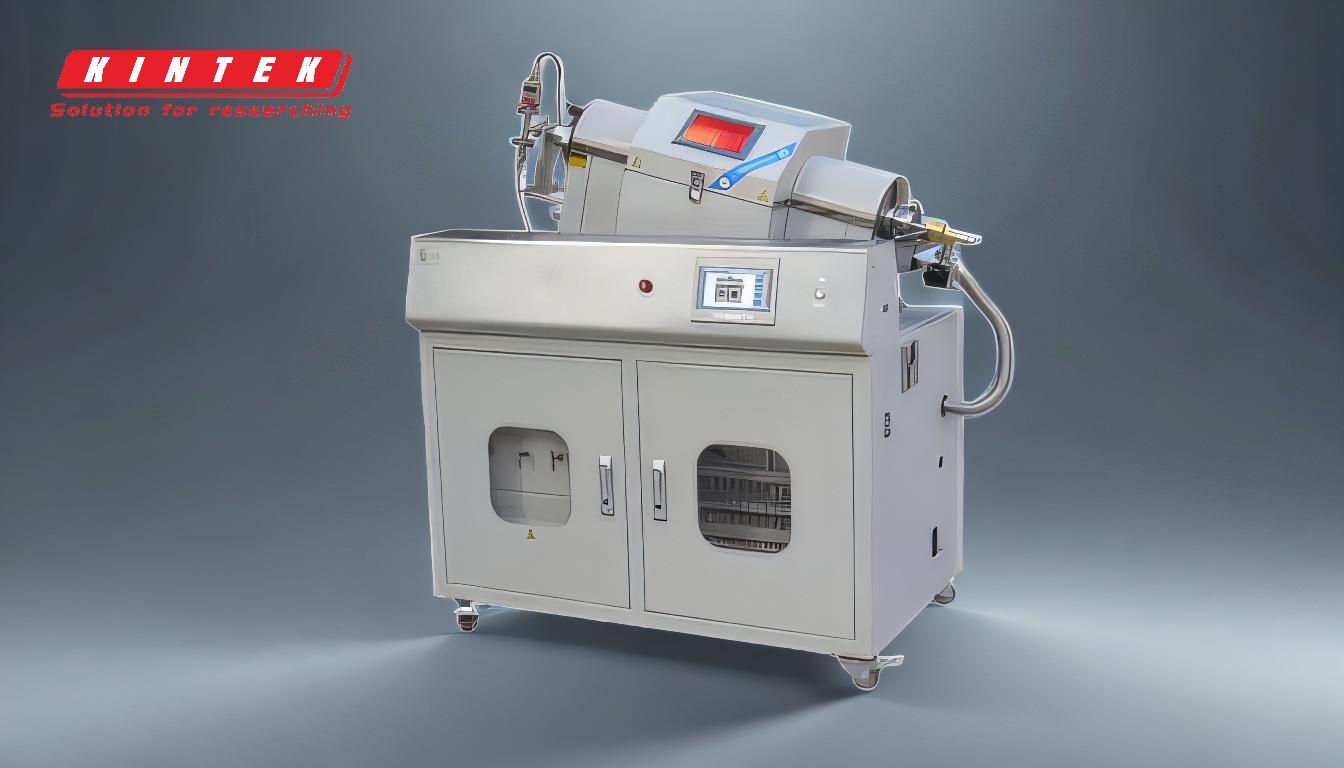
-
Higher Costs:
- PVD is generally more expensive than other thin-film deposition techniques due to the need for complex machinery and skilled operators. The cost varies depending on the specific PVD method used. For example, evaporation is a lower-cost option, while ion beam sputtering and magnetron sputtering are more expensive. Magnetron sputtering, though costly, offers better scalability, which can offset some of the initial investment for large-scale production.
-
Slower Operating Rates:
- PVD processes are relatively slow compared to other coating methods. This slower rate can be a significant limitation in high-volume production environments where speed and efficiency are critical. The need for intense heating and cooling cycles further contributes to the slower operating rate, making PVD less suitable for applications requiring rapid turnaround times.
-
"Line of Sight" Limitation:
- PVD is a "line of sight" technique, meaning it can only coat surfaces that are directly exposed to the vapor source. This limitation makes it unsuitable for coating complex geometries or non-visible surfaces, such as the interiors of deep holes or intricate components. As a result, alternative coating methods may be required for applications involving complex shapes.
-
Equipment and Operator Requirements:
- The PVD process requires specialized equipment, including vacuum chambers, high-power sources, and precise control systems. Additionally, skilled operators are needed to manage the process effectively, further increasing the overall cost and complexity. These requirements can be a barrier for smaller operations or those with limited technical expertise.
-
Comparison with Chemical Vapor Deposition (CVD):
- While PVD has its limitations, it is important to note that CVD, another common thin-film deposition method, also has significant drawbacks. CVD typically operates at high temperatures, which can cause thermal instability in many substrates. Additionally, CVD requires chemical precursors with high vapor pressure, which can be toxic and hazardous. The by-products of CVD are often toxic and corrosive, requiring costly neutralization processes. In contrast, PVD is generally more environmentally friendly and does not involve the same level of chemical hazards.
-
Environmental and Durability Advantages:
- Despite its limitations, PVD offers several environmental and durability advantages. PVD coatings are known for their corrosion resistance, enhanced wear resistance, and longer lifespan. The process is also environmentally sound, as it does not involve harmful chemicals or produce toxic by-products. These benefits make PVD a preferred choice for applications where durability and environmental considerations are paramount.
In summary, while PVD is a versatile and effective coating method, its higher costs, slower operating rates, and "line of sight" limitations must be carefully weighed against its benefits. Understanding these constraints is essential for selecting the most appropriate coating method for specific applications.
Summary Table:
Limitation | Details |
---|---|
Higher Costs | Complex machinery and skilled operators increase expenses. |
Slower Operating Rates | Slower than other methods, unsuitable for high-volume production. |
Line-of-Sight Limitation | Cannot coat complex geometries or non-visible surfaces. |
Equipment & Operator Needs | Requires specialized equipment and skilled personnel, adding complexity. |
Environmental Advantages | Eco-friendly, no harmful chemicals or toxic by-products. |
Need help choosing the right coating method? Contact our experts today for tailored solutions!