A rotary kiln is a critical piece of equipment used in various industrial processes, such as cement production, lime calcination, and chemical processing. Its primary function is to heat materials to high temperatures in a continuous process. The main components of a rotary kiln include the shell, refractory lining, support tyres (riding rings) and rollers, drive gear, and internal heat exchangers. Each component plays a vital role in ensuring the kiln operates efficiently and withstands the harsh conditions of high-temperature processing. Understanding these components is essential for equipment purchasers to make informed decisions about customization, maintenance, and operational efficiency.
Key Points Explained:
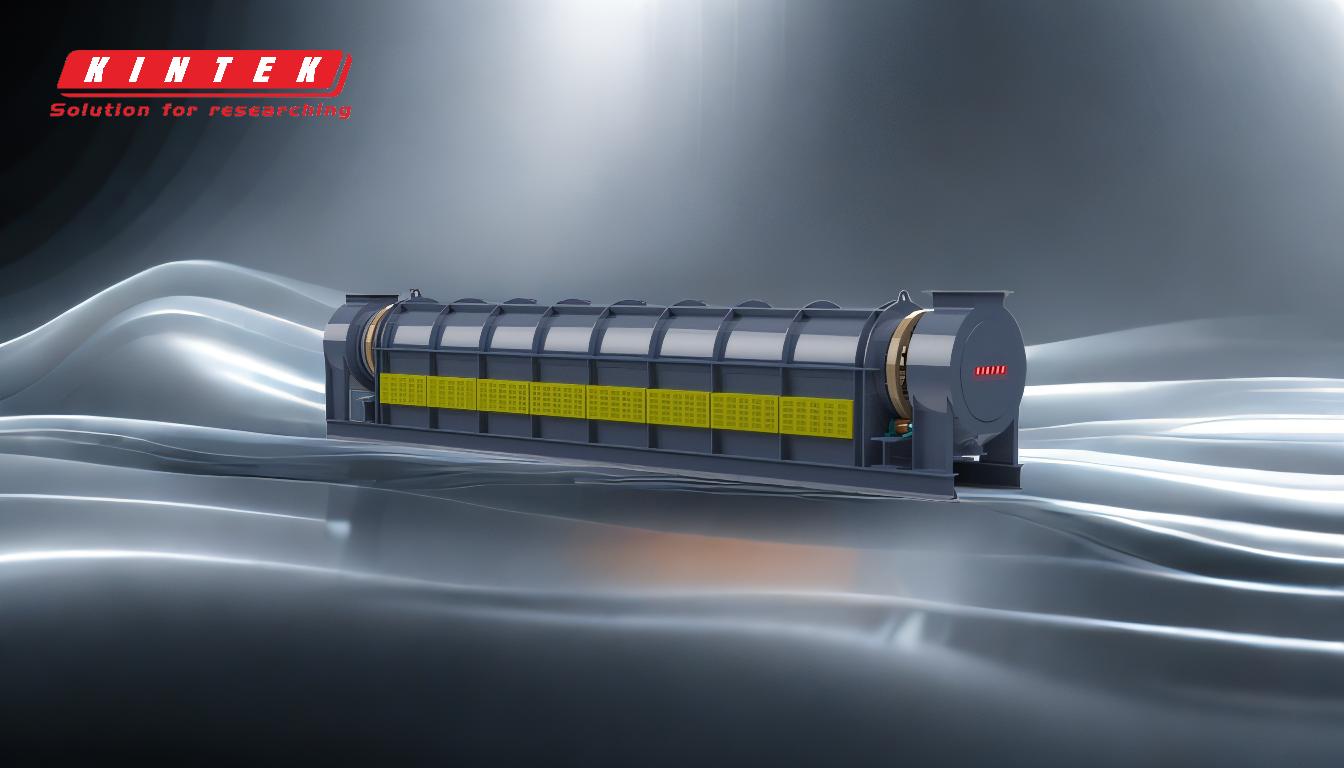
-
Kiln Shell:
- The kiln shell is the outermost structural component of the rotary kiln, typically made of high-strength steel to withstand extreme temperatures and mechanical stresses.
- It is conically tapered at the ends to facilitate the movement of materials through the kiln.
- The shell experiences significant torsion and flexural stress due to the rotational forces and the weight of the materials inside.
- For purchasers, the material and thickness of the shell are critical considerations, as they directly impact the kiln's durability and ability to handle specific processing requirements.
-
Refractory Lining:
- The refractory lining is an inner layer of heat-resistant material that protects the kiln shell from the extreme temperatures inside the kiln.
- It also helps retain heat, improving the thermal efficiency of the kiln.
- The choice of refractory material depends on the type of material being processed and the operating temperature. Common materials include alumina, silica, and magnesia-based refractories.
- Purchasers should evaluate the refractory lining's thermal conductivity, abrasion resistance, and chemical compatibility with the processed materials.
-
Support Tyres (Riding Rings) and Rollers:
- Support tyres, also known as riding rings, are large steel rings mounted on the kiln shell. They rest on rollers, which support the weight of the kiln and allow it to rotate smoothly.
- The rollers are typically equipped with bearings to reduce friction and ensure consistent rotation.
- Proper alignment and maintenance of the support tyres and rollers are crucial to prevent uneven wear and operational issues.
- For purchasers, the quality of these components is essential to minimize downtime and maintenance costs.
-
Drive Gear:
- The drive gear is responsible for rotating the kiln at a controlled speed. It can be powered by various drive systems, such as chain and sprocket drives, gear drives, friction drives, or direct drive assemblies.
- The choice of drive system depends on the kiln's size, load, and operational requirements.
- A reliable drive gear ensures consistent rotation, which is critical for uniform heating and processing of materials.
- Purchasers should consider the drive system's efficiency, maintenance requirements, and compatibility with their operational setup.
-
Internal Heat Exchangers:
- Internal heat exchangers are components within the kiln that facilitate heat transfer between the hot gases and the material being processed.
- They enhance the kiln's thermal efficiency by recovering heat from the exhaust gases and transferring it to the incoming material.
- The design and placement of heat exchangers depend on the specific application and the material being processed.
- Purchasers should evaluate the heat exchanger's design, material, and heat transfer efficiency to optimize energy consumption and processing performance.
-
Additional Components:
- Discharge Breeching: This component is located at the discharge end of the kiln and facilitates the removal of processed materials. It must be designed to handle the specific characteristics of the material, such as temperature and abrasiveness.
- Trunnion Wheels: These are support wheels that help stabilize the kiln and ensure smooth rotation. They are particularly important in larger kilns.
- Product Discharge Area: This area is customized based on the material being processed and the desired output. It may include cooling systems or additional processing equipment.
Understanding these components and their functions is essential for equipment purchasers to select a rotary kiln that meets their specific processing needs. Customization, material selection, and maintenance considerations are key factors that influence the kiln's performance, longevity, and operational costs.
Summary Table:
Component | Function | Key Considerations |
---|---|---|
Kiln Shell | Outer structural layer; withstands extreme temperatures and mechanical stress | Material, thickness, and durability for specific processing needs |
Refractory Lining | Protects shell from heat; improves thermal efficiency | Thermal conductivity, abrasion resistance, and chemical compatibility |
**Support Tyres & Rollers | Supports kiln weight; ensures smooth rotation | Alignment, maintenance, and quality to minimize downtime |
Drive Gear | Rotates kiln at controlled speed | Efficiency, maintenance requirements, and compatibility with operational setup |
**Internal Heat Exchangers | Enhances heat transfer and thermal efficiency | Design, material, and heat transfer efficiency for optimized energy consumption |
Additional Components | Includes discharge breeching, trunnion wheels, and product discharge area | Customization based on material characteristics and output requirements |
Ready to optimize your industrial process? Contact us today to find the perfect rotary kiln for your needs!