Powder metallurgy is a versatile manufacturing process used to produce sintered parts with intricate shapes and precise dimensions. The process typically involves three main steps: powder selection, compaction, and sintering. However, advanced techniques like metal injection molding (MIM), hot isostatic pressing (HIP), additive manufacturing, and Spark Plasma Sintering (SPS) have expanded the capabilities of powder metallurgy. These methods enable the production of complex components for industries such as automotive, aerospace, and cutting tools. The choice of method depends on the desired properties of the final product, including strength, hardness, and dimensional accuracy.
Key Points Explained:
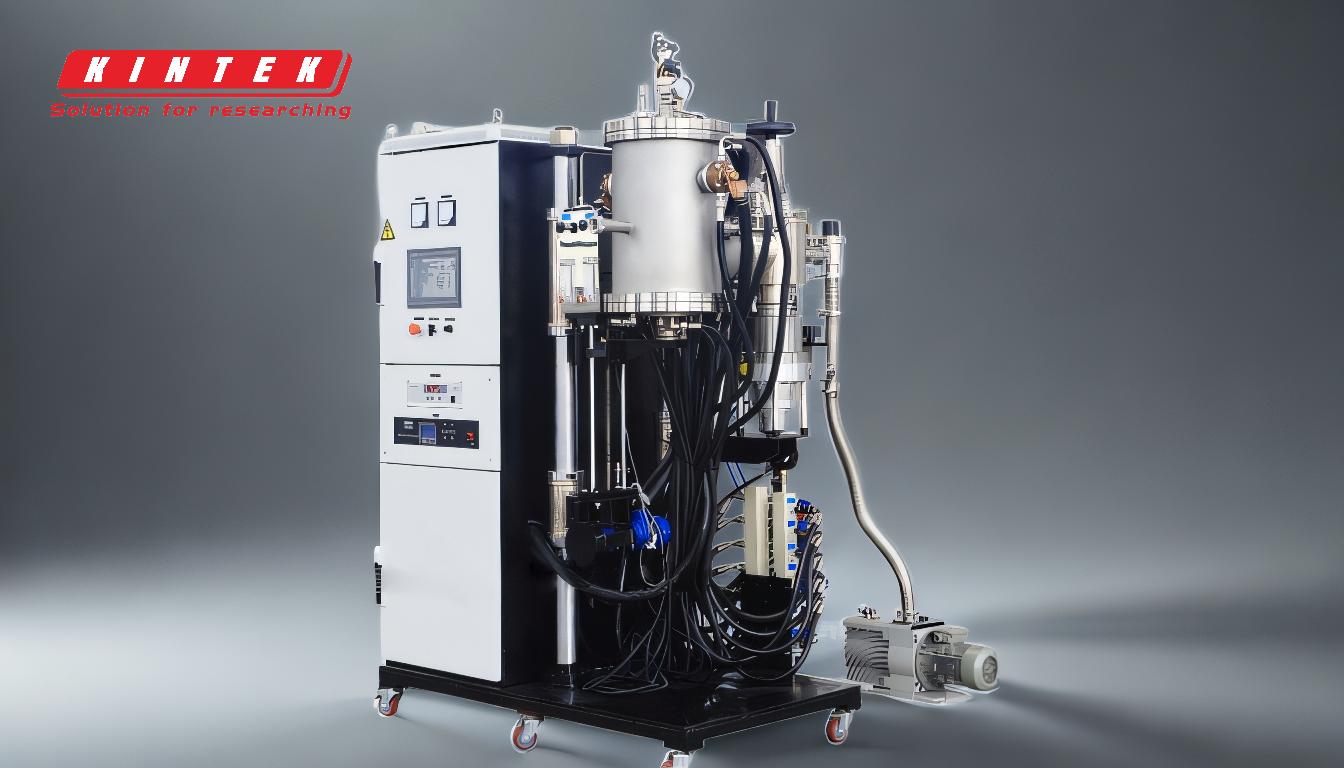
-
Traditional Powder Metallurgy (Press and Sinter)
- Powder Selection: The process begins with selecting metal powders, such as iron, nickel, molybdenum, or copper, often mixed with lubricants to improve flow and compaction.
- Compaction: The powder is pressed into a die at room temperature to form a "green" part with initial strength. This step determines the shape and density of the part.
- Sintering: The green part is heated in a furnace at temperatures just below the melting point of the metal. This bonds the particles together, enhancing strength and hardness without liquefying the material. Controlled atmospheric conditions are often used to prevent oxidation.
-
Metal Injection Molding (MIM)
- Powder Mixing: Fine metal powders are mixed with a thermoplastic binder to create a feedstock.
- Injection Molding: The feedstock is injected into a mold under high pressure to form a green part.
- Debinding: The binder is removed through thermal or chemical processes.
- Sintering: The part is sintered to achieve full density and mechanical properties. MIM is ideal for producing small, complex parts with high precision.
-
Hot Isostatic Pressing (HIP)
- Powder Compaction: Metal powders are placed in a mold and subjected to high pressure and temperature simultaneously.
- Sintering: The combination of heat and pressure densifies the powder, resulting in a near-net-shape part with minimal porosity. HIP is used for high-performance components requiring superior mechanical properties.
-
Additive Manufacturing (3D Printing)
- Powder Bed Fusion: Metal powders are selectively melted using a laser or electron beam to build parts layer by layer.
- Binder Jetting: A liquid binder is selectively deposited onto a powder bed to create a green part, which is later sintered.
- Direct Energy Deposition: Metal powder is fed into a melt pool created by a laser or electron beam, allowing for the repair or addition of material to existing parts. Additive manufacturing is ideal for prototyping and producing complex geometries.
-
Spark Plasma Sintering (SPS)
- Powder Preparation: Metal powders are placed in a graphite die.
- Sintering: A pulsed electric current is applied, generating plasma that heats the powder rapidly. Simultaneous application of pressure results in fast densification. SPS is used for advanced materials, including ceramics and composites, due to its ability to achieve high densities at lower temperatures.
-
Post-Treatment Processes
- Machining: Sintered parts may require additional machining to achieve precise dimensions or surface finishes. Diamond tools or ultrasonic machining are often used for hard materials like ceramics.
- Assembly: For ceramic parts, metallization and brazing are used to join components. This is common in applications requiring electrical conductivity or hermetic sealing.
- Heat Treatment: Additional heat treatments, such as tempering or case hardening, may be applied to enhance mechanical properties.
-
Applications of Sintered Parts
- Automotive Industry: Sintered parts are widely used in gears, camshafts, and valve seats due to their strength and wear resistance.
- Cutting Tools: Sintered carbide tools are known for their hardness and durability.
- Filters: Sintered metal filters are used in applications requiring precise filtration, such as in the chemical and pharmaceutical industries.
By understanding these methods, manufacturers can select the most appropriate technique for producing sintered parts that meet specific performance requirements and cost considerations.
Summary Table:
Method | Key Steps | Applications |
---|---|---|
Traditional Powder Metallurgy | Powder selection, compaction, sintering | Automotive gears, camshafts, valve seats |
Metal Injection Molding (MIM) | Powder mixing, injection molding, debinding, sintering | Small, complex parts with high precision |
Hot Isostatic Pressing (HIP) | Powder compaction, sintering under high pressure and temperature | High-performance components with minimal porosity |
Additive Manufacturing | Powder bed fusion, binder jetting, direct energy deposition | Prototyping, complex geometries |
Spark Plasma Sintering (SPS) | Powder preparation, rapid sintering with pulsed electric current and pressure | Advanced materials like ceramics and composites |
Post-Treatment Processes | Machining, assembly, heat treatment | Enhancing mechanical properties and surface finishes |
Discover the best powder metallurgy solution for your needs—contact our experts today!