Pyrolysis is a complex thermal decomposition process influenced by multiple parameters that determine the efficiency, quality, and type of end products. Key factors include the composition of the feedstock, temperature, residence time, particle size, moisture content, heating rate, pressure, atmosphere, and feed rate. These parameters interact to influence the thermal decomposition of organic materials, the composition of gas, liquid, and solid products, and the overall efficiency of the process. Understanding and controlling these factors is crucial for optimizing pyrolysis outcomes, whether the goal is to maximize gas, liquid, or solid yields.
Key Points Explained:
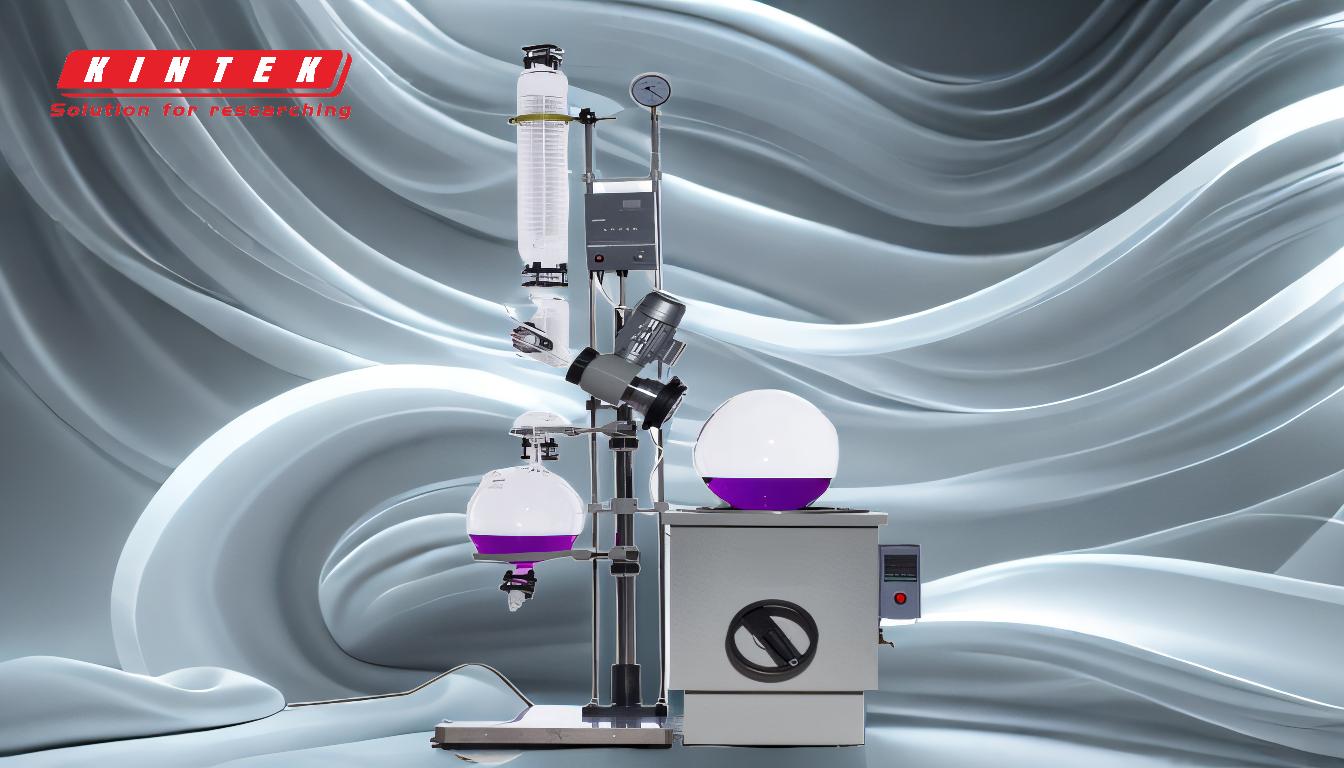
-
Feedstock Composition
- The type and composition of the feedstock significantly impact pyrolysis outcomes. Biomass, waste, or other organic materials have varying chemical compositions, leading to different decomposition temperatures and product distributions.
- For example, biomass with high cellulose content decomposes differently compared to lignin-rich materials. Similarly, waste materials like tires contain fibers and steel, which alter the pyrolysis process and product composition.
- Feedstock composition also determines the energy content and the types of gases, liquids, or solids produced.
-
Temperature
- Temperature is one of the most critical parameters in pyrolysis. It directly influences the thermal decomposition rate and the distribution of end products.
- Higher temperatures (typically above 500°C) favor the production of non-condensable gases like hydrogen, methane, and carbon monoxide.
- Lower temperatures (typically between 300°C and 500°C) are more conducive to producing high-quality solid products like biochar and liquid products like pyrolysis oil.
- Each component of the feedstock decomposes at specific temperature ranges, so temperature control is essential for targeting desired products.
-
Residence Time
- Residence time refers to the duration the feedstock remains in the pyrolysis chamber. It affects the degree of thermal conversion and the composition of vapors and gases.
- Longer residence times allow for more complete decomposition of organic materials, leading to higher gas yields and reduced solid residues.
- Shorter residence times may result in incomplete decomposition, favoring the production of liquid and solid products.
- Optimal residence time depends on the feedstock and desired product distribution.
-
Particle Size and Physical Structure
- The size and physical structure of the feedstock particles influence heat transfer and reaction rates during pyrolysis.
- Smaller particle sizes have a larger surface area-to-volume ratio, enabling faster heat transfer and quicker thermal decomposition. This often leads to higher yields of pyrolysis oil and gases.
- Larger particles may result in uneven heating and slower decomposition, affecting the quality and quantity of end products.
- Uniform particle sizes are preferred for consistent pyrolysis outcomes.
-
Moisture Content
- Moisture content in the feedstock affects the energy efficiency and product quality of pyrolysis.
- High moisture content requires additional energy to evaporate water, reducing the overall thermal efficiency of the process.
- Excess moisture can also dilute pyrolysis vapors, lowering the quality of liquid products like bio-oil.
- Ideally, feedstock should be dried to minimize moisture content before pyrolysis.
-
Heating Rate
- The rate at which the feedstock is heated influences the pyrolysis mechanism and product distribution.
- Fast heating rates (flash pyrolysis) favor the production of liquid products like bio-oil, as rapid heating minimizes secondary reactions.
- Slow heating rates promote the formation of solid products like biochar and non-condensable gases.
- The heating rate must be optimized based on the desired end products and feedstock characteristics.
-
Pressure
- Pressure conditions within the pyrolysis reactor affect the decomposition process and product composition.
- Higher pressures can increase the yield of gases and alter the composition of liquid products.
- Lower pressures are often used to enhance the production of bio-oil by reducing secondary reactions.
- Pressure control is particularly important in high-temperature pyrolysis processes.
-
Atmosphere
- The atmosphere in which pyrolysis occurs (e.g., inert, oxidative, or reducing) influences the chemical reactions and product yields.
- An inert atmosphere (e.g., nitrogen or argon) is commonly used to prevent oxidation and promote thermal decomposition.
- Oxidative atmospheres can lead to partial combustion, altering the product distribution and reducing the quality of bio-oil and biochar.
- The choice of atmosphere depends on the desired products and process conditions.
-
Feed Rate
- The rate at which feedstock is introduced into the pyrolysis reactor affects the residence time and heat distribution.
- A high feed rate may lead to incomplete decomposition and uneven heating, reducing process efficiency.
- A low feed rate ensures sufficient residence time and heat transfer but may lower overall throughput.
- Balancing feed rate with other parameters is essential for optimal pyrolysis performance.
-
Reactor Design and Configuration
- The design of the pyrolysis reactor (e.g., fixed bed, fluidized bed, or rotary kiln) influences heat transfer, residence time, and product distribution.
- Different reactor types are suited for specific feedstocks and desired products. For example, fluidized bed reactors are effective for fast pyrolysis to produce bio-oil.
- Reactor configuration also affects temperature uniformity and the ability to control process parameters.
By carefully controlling these parameters, pyrolysis processes can be optimized to produce desired products efficiently. Understanding the interplay between these factors is essential for tailoring pyrolysis to specific feedstocks and applications.
Summary Table:
Parameter | Impact on Pyrolysis |
---|---|
Feedstock Composition | Determines decomposition temperature, product distribution, and energy content. |
Temperature | Influences thermal decomposition rate and product distribution (gas, liquid, solid). |
Residence Time | Affects degree of conversion and product composition. |
Particle Size | Influences heat transfer and reaction rates; smaller particles yield more oil/gas. |
Moisture Content | High moisture reduces energy efficiency and product quality. |
Heating Rate | Fast heating favors liquid products; slow heating favors solids and gases. |
Pressure | Higher pressures increase gas yields; lower pressures enhance bio-oil production. |
Atmosphere | Inert atmospheres prevent oxidation; oxidative atmospheres alter product quality. |
Feed Rate | Affects residence time and heat distribution; must balance with other parameters. |
Reactor Design | Influences heat transfer, residence time, and product distribution. |
Optimize your pyrolysis process today—contact our experts for tailored solutions!