Rotary kilns are complex industrial equipment used for high-temperature processing of materials. Their design and operation are governed by a variety of parameters that ensure efficient and effective performance. These parameters can be broadly categorized into design, structural, and operational factors. Design parameters include material characteristics like particle size, bulk density, and thermal properties, which influence the kiln's construction. Structural parameters involve components such as the kiln shell, refractory lining, and drive assembly. Operational parameters, such as inclination angle, rotation speed, and temperature profiles, dictate the kiln's performance during use. Understanding these parameters is crucial for optimizing the kiln's efficiency and achieving desired process outcomes.
Key Points Explained:
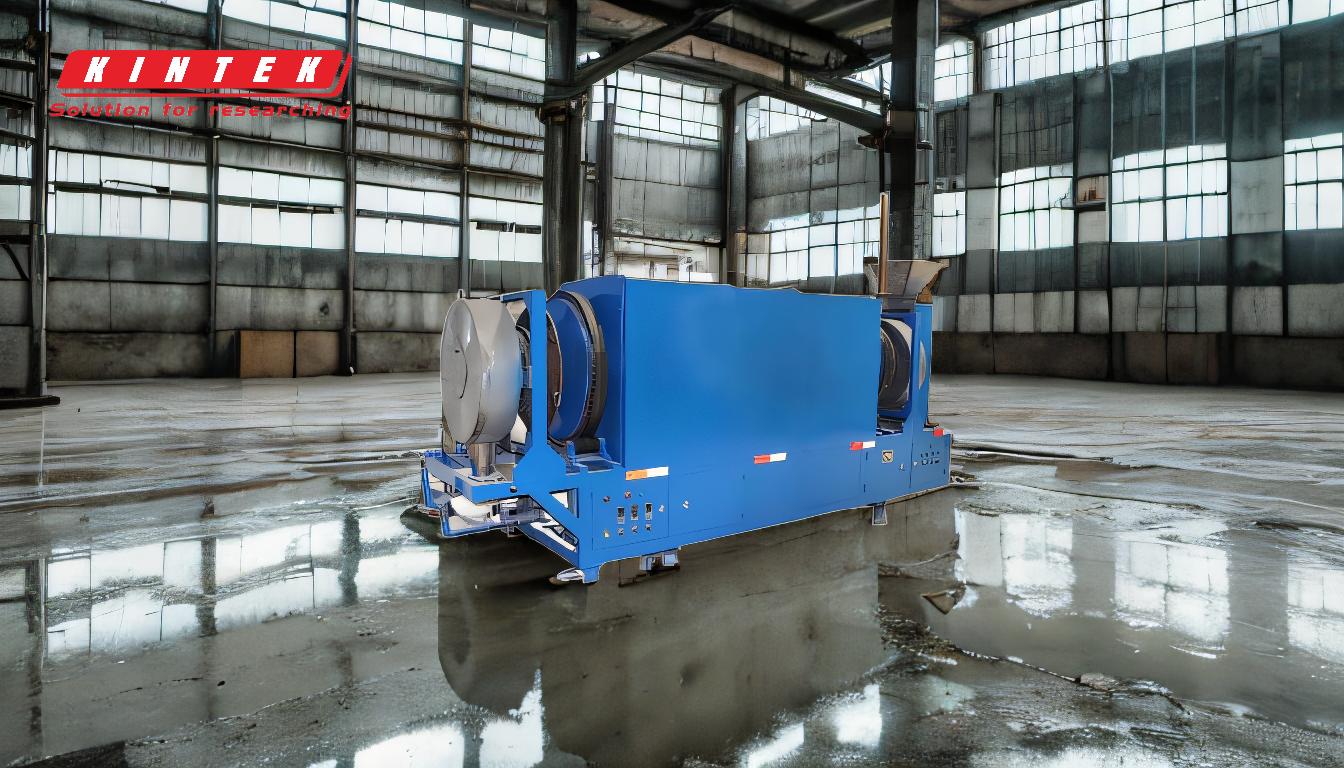
-
Design Parameters:
-
Material Characteristics: The design of a rotary kiln is heavily influenced by the properties of the material being processed. These include:
- Particle Size Distribution: Determines how the material flows and reacts within the kiln.
- Bulk Density: Affects the volume of material that can be processed at a given time.
- Abrasiveness and Corrosiveness: Influences the choice of materials for the kiln's construction to ensure durability.
- Specific Heat and Heat of Reaction: Dictates the energy requirements for processing.
- Thermal Conductivity: Affects heat transfer efficiency within the kiln.
- Chemical Composition: Determines the kiln's resistance to chemical reactions and corrosion.
-
Material Characteristics: The design of a rotary kiln is heavily influenced by the properties of the material being processed. These include:
-
Structural Parameters:
- Kiln Shell: The main body of the kiln, often conically tapered at the ends, designed to withstand torsion and flexural stress.
- Refractory Lining: Protects the shell from high temperatures and chemical reactions, ensuring longevity.
- Support Tyres and Rollers: Provide structural support and allow the kiln to rotate smoothly.
- Drive Assembly: Includes mechanisms like chain and sprocket drives, gear drives, friction drives, or direct drives, which cause the kiln to rotate.
- Internal Heat Exchangers: Enhance heat transfer efficiency within the kiln.
-
Operational Parameters:
- Inclination Angle: The tilt of the kiln affects the flow rate of the material through the kiln.
- Rotation Speed: Determines the rate at which the material is mixed and exposed to heat.
- Retention Time: The duration that solid particles remain in the kiln, influencing the extent of reaction or processing.
- Temperature Profiles: The kiln operates with multiple heating zones (drying, heating, reaction, and soaking) to achieve the desired thermal processing.
- Material Flow Rate and Discharge Rate: Control the throughput and ensure consistent processing.
- Bed Depth: Controlled using a ring dam, affecting the material's exposure to heat and reaction conditions.
-
Heating Zones:
- Drying Zone: Removes moisture from the material.
- Heating Zone: Raises the material to the required temperature for processing.
- Reaction Zone: Where the primary chemical or physical transformations occur.
- Soaking Zone: Ensures uniform temperature distribution and completes any remaining reactions.
-
Control Mechanisms:
- Ring Dam: Used to control the bed depth, ensuring optimal exposure of the material to heat and reaction conditions.
- Drive Systems: Various drive mechanisms (chain and sprocket, gear, friction, or direct) are chosen based on the kiln's size and operational requirements.
By carefully considering these parameters, rotary kilns can be designed and operated to maximize efficiency, durability, and process effectiveness. Each parameter plays a critical role in ensuring that the kiln meets the specific needs of the material being processed, whether it involves drying, heating, or chemical reactions.
Summary Table:
Parameter Type | Key Factors |
---|---|
Design Parameters | Particle size, bulk density, thermal properties, chemical composition |
Structural Parameters | Kiln shell, refractory lining, support tyres, drive assembly, heat exchangers |
Operational Parameters | Inclination angle, rotation speed, temperature profiles, retention time |
Heating Zones | Drying, heating, reaction, soaking |
Control Mechanisms | Ring dam, drive systems |
Ready to optimize your rotary kiln performance? Contact our experts today for tailored solutions!