Thin wall molding machines are specialized equipment used in the manufacturing of thin-walled plastic parts, which are commonly found in industries like packaging, electronics, and automotive. Selecting the right machine involves evaluating several critical parameters to ensure optimal performance, efficiency, and cost-effectiveness. These parameters include the machine's clamping force, injection speed, shot size, mold design compatibility, energy efficiency, and control systems. Additionally, factors like material compatibility, cycle time, and maintenance requirements play a significant role in the decision-making process. By carefully considering these factors, manufacturers can choose a machine that meets their specific production needs and ensures high-quality output.
Key Points Explained:
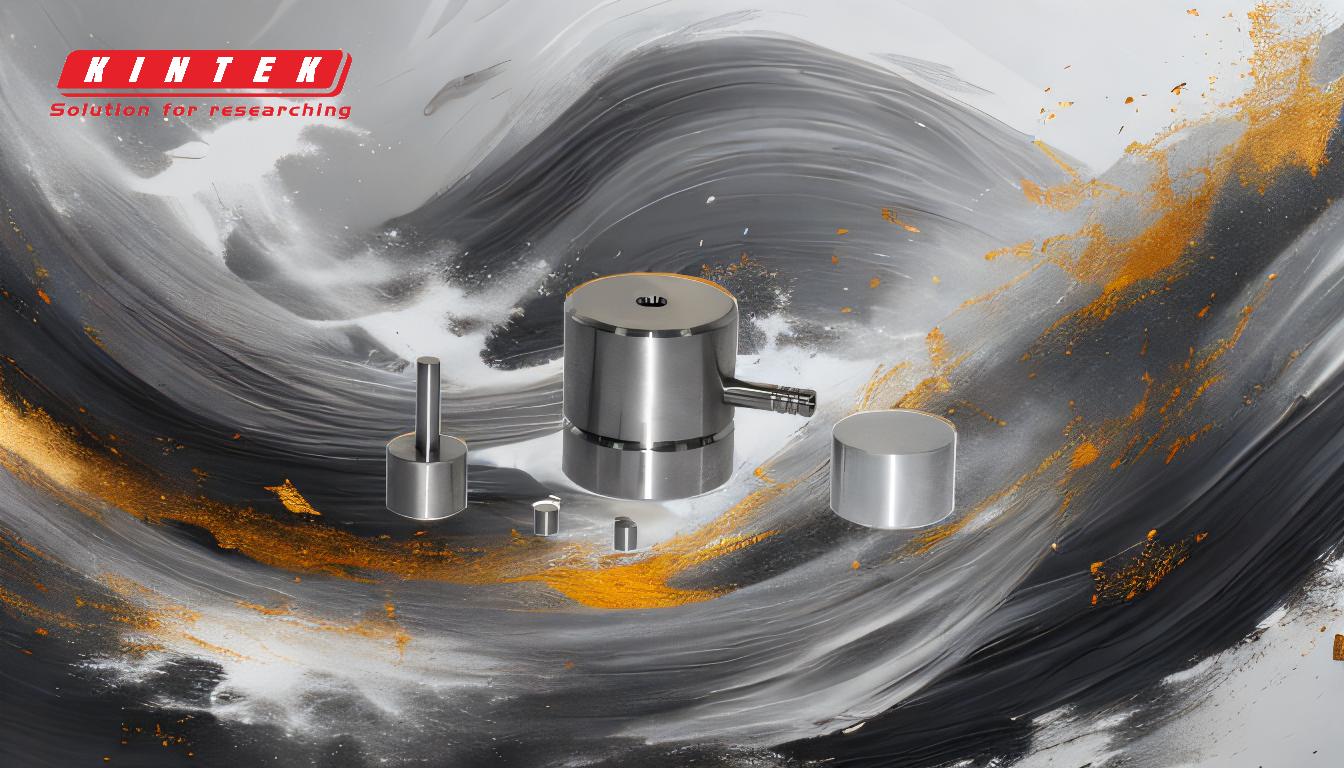
-
Clamping Force:
- The clamping force is the pressure applied to keep the mold closed during the injection process. For thin wall molding, high clamping force is often required due to the high injection pressures needed to fill thin-walled cavities quickly.
- Importance: Insufficient clamping force can lead to flash (excess material escaping from the mold), while excessive force can damage the mold or machine. The force should be calculated based on the projected area of the part and the injection pressure.
-
Injection Speed:
- Thin wall molding requires extremely high injection speeds to ensure the molten plastic fills the mold before it cools and solidifies.
- Importance: High-speed injection reduces cycle time and improves part quality by preventing premature cooling. Machines with advanced hydraulic or electric systems are often preferred for their ability to achieve consistent high speeds.
-
Shot Size:
- The shot size refers to the maximum volume of material that can be injected in a single cycle. For thin wall molding, the shot size must be sufficient to fill the mold completely without over-packing.
- Importance: A machine with an appropriate shot size ensures efficient material usage and prevents defects like short shots (incomplete filling) or excessive material waste.
-
Mold Design Compatibility:
- Thin wall molds are designed with specific features like thin cavities, high cooling rates, and precise gate designs. The molding machine must be compatible with these design elements.
- Importance: Compatibility ensures that the mold can be effectively used with the machine, leading to consistent part quality and reduced downtime.
-
Energy Efficiency:
- Energy consumption is a significant factor in the overall cost of operation. Machines with energy-efficient systems, such as servo-driven hydraulics or all-electric systems, can reduce power usage.
- Importance: Lower energy consumption translates to cost savings and a smaller environmental footprint, making energy-efficient machines a preferred choice for long-term operations.
-
Control Systems:
- Advanced control systems allow for precise regulation of injection speed, pressure, temperature, and other parameters. These systems often include features like real-time monitoring and automated adjustments.
- Importance: Precise control ensures consistent part quality and reduces the likelihood of defects. It also allows for easier troubleshooting and optimization of the molding process.
-
Material Compatibility:
- Thin wall molding often involves specialized materials with specific flow and cooling characteristics. The machine must be capable of handling these materials effectively.
- Importance: Material compatibility ensures that the machine can process the required materials without issues like degradation or inconsistent flow, leading to better part quality.
-
Cycle Time:
- Cycle time is the total time required to complete one molding cycle, including injection, cooling, and ejection. For thin wall molding, shorter cycle times are often desirable to increase production rates.
- Importance: Reducing cycle time improves productivity and lowers production costs. Machines with fast injection and cooling systems are ideal for achieving shorter cycle times.
-
Maintenance Requirements:
- Regular maintenance is essential to keep the machine operating efficiently. Machines with easy-to-access components and robust construction require less frequent maintenance.
- Importance: Lower maintenance requirements reduce downtime and maintenance costs, ensuring continuous production and longer machine lifespan.
-
Cost Considerations:
- The initial cost of the machine, along with operational and maintenance costs, should be evaluated. While advanced machines may have a higher upfront cost, their efficiency and durability can lead to long-term savings.
- Importance: A cost-benefit analysis helps in selecting a machine that offers the best value for money, balancing performance and affordability.
By considering these parameters, manufacturers can select a thin wall molding machine that aligns with their production goals, ensuring high-quality output, efficiency, and cost-effectiveness.
Summary Table:
Parameter | Importance |
---|---|
Clamping Force | Ensures mold stays closed; prevents flash or mold damage. |
Injection Speed | High speeds reduce cycle time and improve part quality. |
Shot Size | Ensures complete mold filling without waste or defects. |
Mold Design Compatibility | Compatibility ensures consistent quality and reduced downtime. |
Energy Efficiency | Reduces operational costs and environmental impact. |
Control Systems | Precise control improves part quality and process optimization. |
Material Compatibility | Ensures effective processing of specialized materials. |
Cycle Time | Shorter cycle times boost productivity and lower costs. |
Maintenance Requirements | Lower maintenance reduces downtime and extends machine lifespan. |
Cost Considerations | Balances performance and affordability for long-term savings. |
Ready to choose the perfect thin wall molding machine? Contact our experts today for personalized guidance!