Chemical Vapor Deposition (CVD) is a widely used technique in materials science and semiconductor manufacturing for depositing thin films. However, it comes with several challenges, including high costs, complex equipment requirements, and potential issues with film quality and uniformity. Additionally, the process often involves high temperatures and toxic gases, posing safety and environmental concerns. Despite its advantages, these problems can limit its applicability and efficiency in certain scenarios.
Key Points Explained:
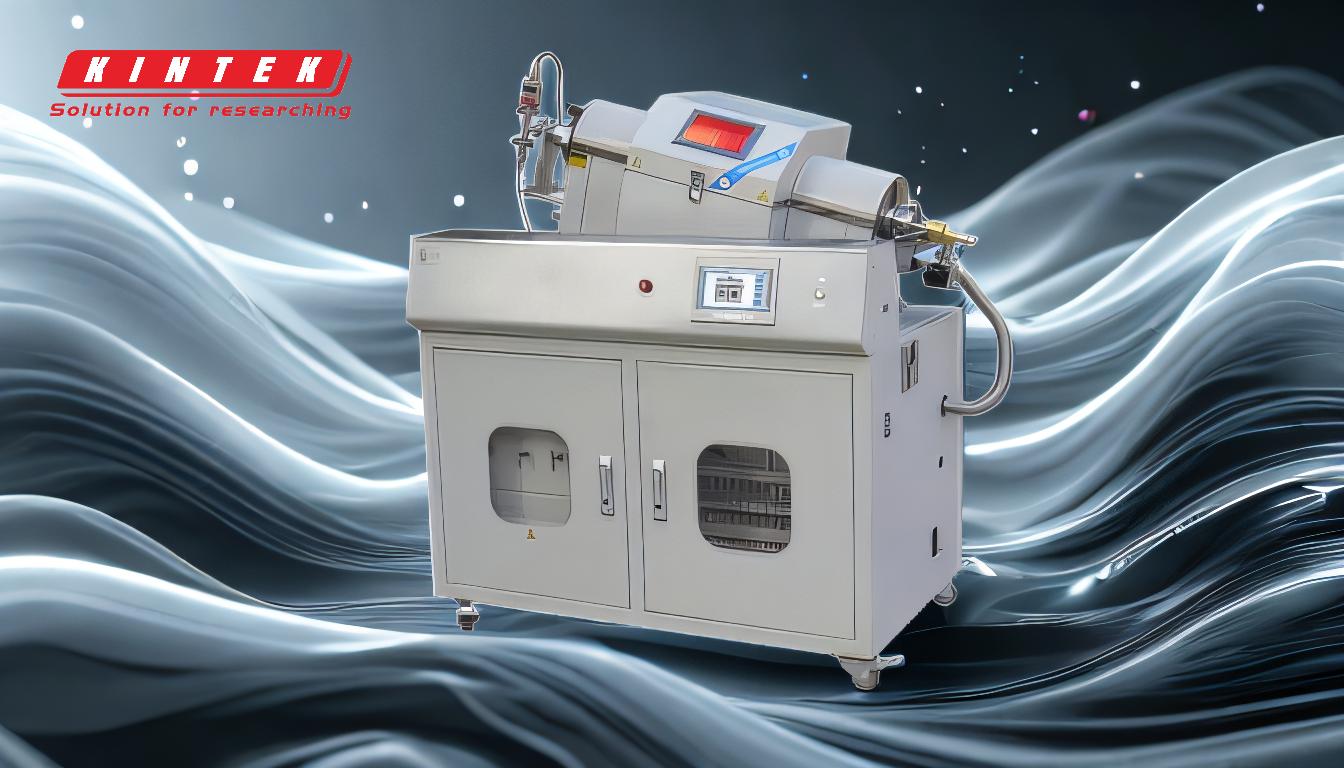
-
High Costs and Complex Equipment:
- CVD requires sophisticated equipment, including vacuum systems, gas delivery systems, and high-temperature furnaces. These components are expensive to purchase and maintain.
- The process often involves multiple steps and precise control of parameters such as temperature, pressure, and gas flow rates, which increases operational complexity and costs.
-
Film Quality and Uniformity:
- Achieving uniform film thickness and composition across large substrates can be challenging. Variations in temperature and gas flow can lead to defects or inconsistencies in the deposited film.
- Impurities in the precursor gases or contamination in the chamber can also affect film quality, leading to defects or poor performance of the final product.
-
High-Temperature Requirements:
- CVD typically operates at high temperatures, which can limit the types of substrates that can be used. For example, materials with low melting points or those that degrade at high temperatures may not be suitable for CVD.
- High temperatures can also lead to thermal stress in the deposited films, potentially causing cracks or delamination.
-
Toxic and Hazardous Gases:
- Many CVD processes involve the use of toxic, flammable, or corrosive gases, such as silane, ammonia, or hydrogen. Handling these gases requires strict safety protocols and specialized equipment to prevent accidents.
- The release of these gases into the environment can pose significant environmental and health risks, necessitating effective waste management and emission control systems.
-
Slow Deposition Rates:
- CVD can have relatively slow deposition rates compared to other thin-film deposition techniques. This can be a disadvantage when high throughput is required, such as in large-scale manufacturing.
- The slow deposition rate can also increase the overall process time, leading to higher production costs.
-
Limited Scalability:
- Scaling up CVD processes for large-area substrates or high-volume production can be challenging. Maintaining uniform conditions across larger areas becomes increasingly difficult, potentially leading to variations in film properties.
- The complexity and cost of scaling up CVD equipment can also be prohibitive for some applications.
-
Alternative Techniques:
- Given the limitations of CVD, alternative techniques such as short path vacuum distillation are sometimes considered for specific applications. Short path vacuum distillation, for example, is used for separating heat-sensitive compounds at lower temperatures, reducing the risk of thermal degradation.
- Techniques like atomic layer deposition (ALD) or physical vapor deposition (PVD) may also be used depending on the specific requirements of the application.
In summary, while CVD is a powerful tool for thin-film deposition, it comes with significant challenges that need to be carefully managed. High costs, complex equipment, and issues with film quality and uniformity are some of the primary concerns. Additionally, the use of toxic gases and high temperatures poses safety and environmental risks. Alternative techniques like short path vacuum distillation may offer advantages in certain scenarios, particularly for heat-sensitive materials.
Summary Table:
Challenge | Description |
---|---|
High Costs and Complex Equipment | Expensive equipment and precise control of parameters increase operational costs. |
Film Quality and Uniformity | Variations in temperature and gas flow can lead to defects or inconsistencies. |
High-Temperature Requirements | Limits substrate options and can cause thermal stress in films. |
Toxic and Hazardous Gases | Requires strict safety protocols and emission control systems. |
Slow Deposition Rates | Low throughput can increase production time and costs. |
Limited Scalability | Difficult to maintain uniform conditions for large-scale production. |
Alternative Techniques | Techniques like ALD or PVD may be better suited for specific applications. |
Struggling with CVD challenges? Contact our experts today to explore better solutions for your thin-film deposition needs!