Physical Vapor Deposition (PVD) is a widely used technique for creating protective coatings with anti-corrosion and wear-resistant properties. However, it comes with several challenges and limitations that can affect its efficiency, cost, and applicability. These include the high cost and complexity of equipment, slow production speeds, limitations in coating complex geometries, and the need for skilled operators and cooling systems. Additionally, PVD can aggressively alter material colors, leading to wastage, and requires high-temperature and vacuum conditions, which add to operational complexity and costs.
Key Points Explained:
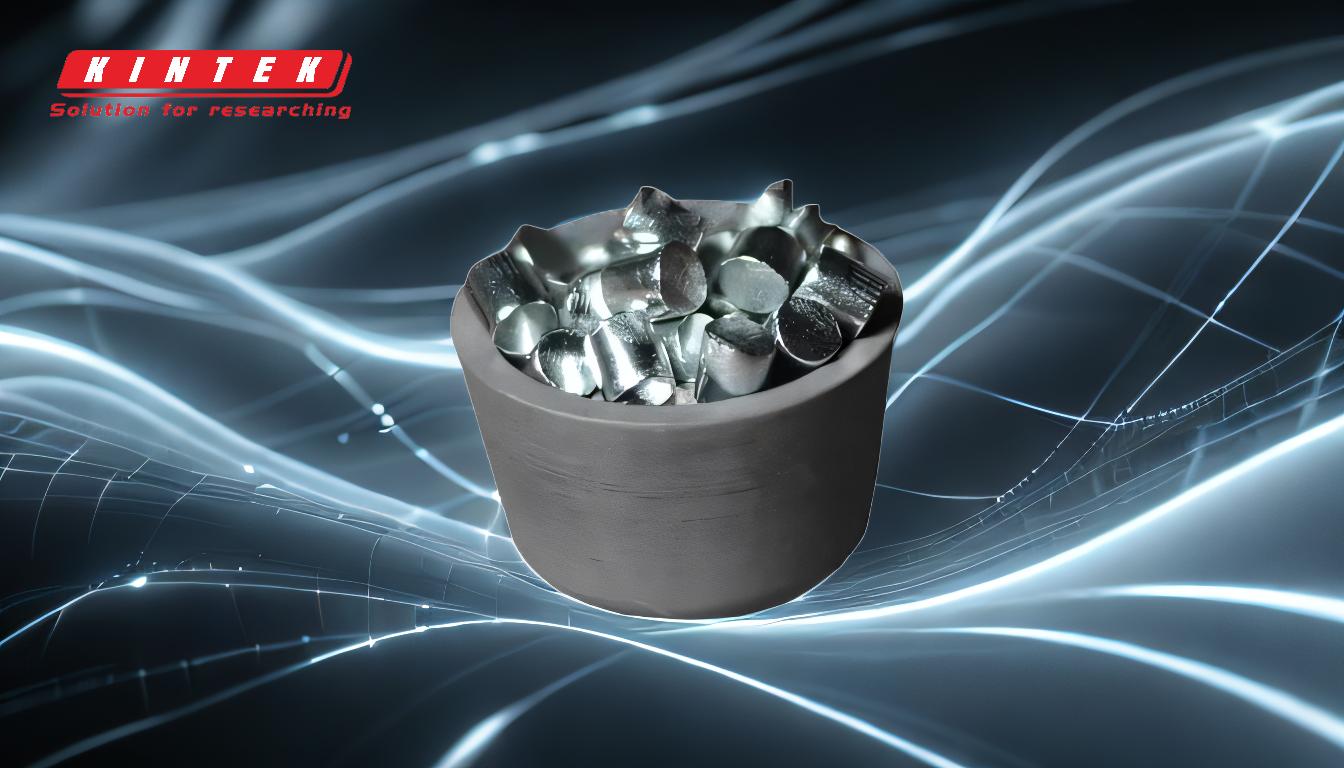
-
High Equipment Cost and Complexity:
- PVD requires specialized and expensive equipment, including large vacuum chambers and cooling systems.
- The process involves high-temperature settings and vacuum conditions, which necessitate sophisticated facilities and skilled operators.
- These factors contribute to higher capital and operational costs, making PVD less accessible for smaller-scale operations.
-
Slow Production Speed:
- Compared to other coating deposition processes, PVD has a relatively slow rate of coating deposition.
- This slower speed can be a significant drawback for industries requiring high-volume production, as it may lead to longer production times and reduced throughput.
-
Line-of-Sight Limitations:
- PVD is a line-of-sight technique, meaning it can only coat surfaces directly exposed to the vapor source.
- This limitation makes it difficult to coat undercuts, internal surfaces, and complex geometries, restricting its applicability for certain substrates.
-
High-Temperature and Vacuum Requirements:
- The process typically operates at high temperatures and in a vacuum, which can be challenging to maintain and control.
- High temperatures can also limit the types of substrates that can be coated, as some materials may not withstand the heat.
- The need for a cooling water system to dissipate heat adds to the complexity and cost of the process.
-
Skilled Operator Requirement:
- Due to the high-temperature and vacuum conditions, PVD requires skilled operators to ensure safe and effective operation.
- The need for specialized training and expertise can be a barrier to entry for some organizations and may increase labor costs.
-
Color Alteration and Material Wastage:
- PVD can aggressively alter the colors of materials, which may not be desirable for certain applications.
- This color change can result in material wastage, as the altered materials may no longer meet the required specifications or aesthetic standards.
-
Environmental and Safety Considerations:
- While PVD does not involve the use of toxic chemicals like CVD, the high-temperature and vacuum conditions still require careful handling to ensure operator safety.
- The process also necessitates the use of cooling systems, which can have environmental implications in terms of energy consumption and water usage.
In summary, while PVD offers significant advantages in terms of coating quality and durability, its high cost, slow production speed, and limitations in coating complex geometries present notable challenges. Additionally, the need for skilled operators, high-temperature and vacuum conditions, and potential material wastage further complicate its use. These factors must be carefully considered when deciding whether PVD is the appropriate coating technique for a given application.
Summary Table:
Challenge | Description |
---|---|
High Equipment Cost | Requires expensive, specialized equipment like vacuum chambers and cooling systems. |
Slow Production Speed | Slower deposition rates compared to other coating methods. |
Line-of-Sight Limitations | Cannot coat undercuts, internal surfaces, or complex geometries effectively. |
High-Temperature & Vacuum | Requires high temperatures and vacuum conditions, limiting substrate compatibility. |
Skilled Operator Requirement | Needs trained operators to handle complex processes safely. |
Color Alteration & Wastage | Aggressively alters material colors, leading to potential wastage. |
Environmental & Safety Issues | High energy and water usage, with safety concerns due to extreme conditions. |
Need help deciding if PVD is right for your application? Contact our experts today for tailored advice!