Zirconia sintering is a critical process in the production of high-performance ceramic materials, but it comes with several challenges. These include issues related to thermal shock, material properties, and the design of sintering equipment. Understanding these problems is essential for optimizing the sintering process and ensuring the quality and durability of the final product.
Key Points Explained:
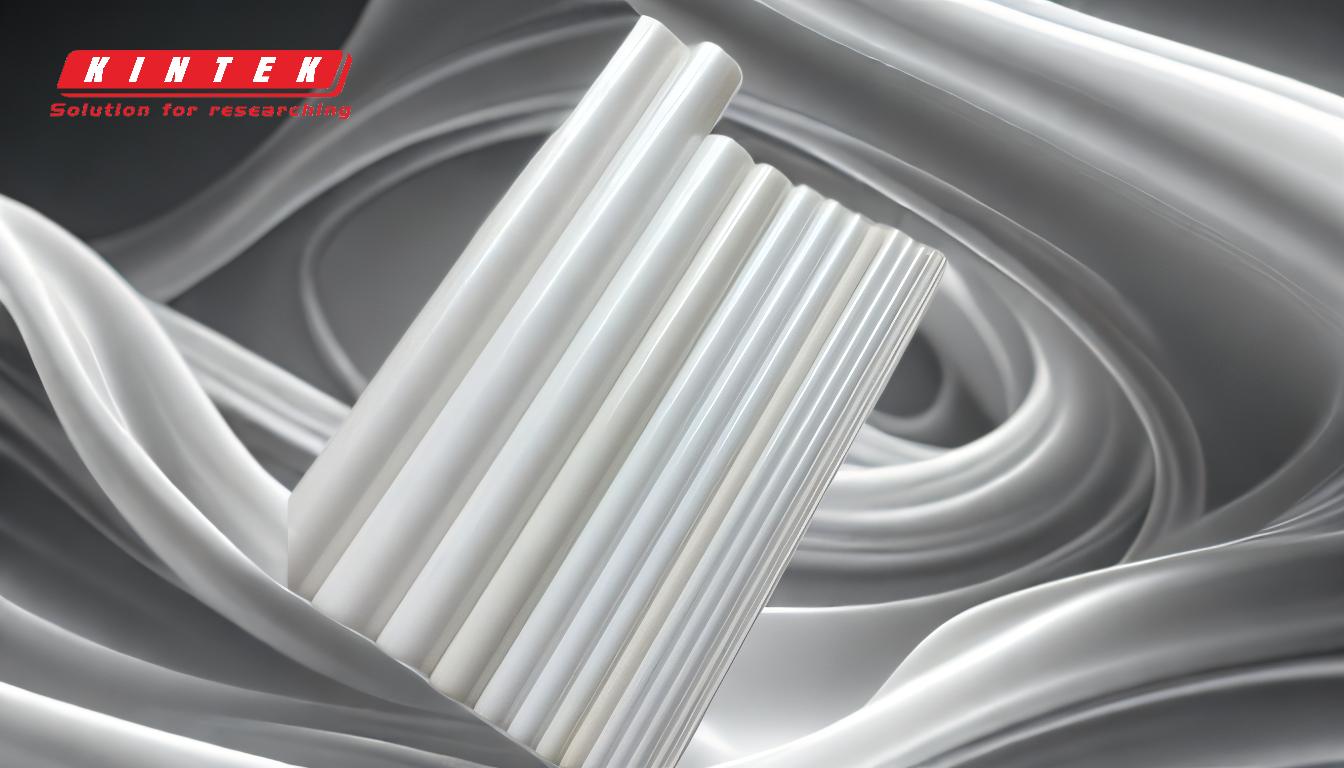
-
Thermal Shock Resistance:
- Problem: During the sintering process, zirconia parts are subjected to rapid temperature changes, especially when quenched immediately after sintering. This can lead to thermal shock, causing cracks or failures in the material.
- Solution: To mitigate this, it's crucial to use materials and designs that can withstand severe thermal-shock loads. For instance, pusher plates in zirconia sintering furnace should be made from materials with a balanced combination of thermal, mechanical, and chemical properties. High-purity alumina without silica is often used, but it must be carefully selected to avoid failures during thermal cycling.
-
Material Properties:
- Problem: The properties of the zirconia material itself, such as its purity and composition, can significantly affect the sintering process. Impurities or incorrect compositions can lead to defects in the final product.
- Solution: Ensuring the use of high-purity zirconia powders and maintaining strict control over the material composition can help in achieving a uniform and defect-free sintered product. This includes careful selection of raw materials and rigorous quality control measures.
-
Sintering Furnace Design:
- Problem: The design of the sintering furnace plays a crucial role in the success of the sintering process. Inadequate furnace design can lead to uneven heating, poor temperature control, and inefficient sintering.
- Solution: Investing in well-designed sintering furnaces that offer precise temperature control and uniform heating is essential. Modern furnaces often come with advanced features like programmable temperature profiles and real-time monitoring to ensure optimal sintering conditions.
-
Process Parameters:
- Problem: Incorrect sintering parameters, such as temperature, heating rate, and holding time, can result in incomplete sintering or over-sintering, leading to poor material properties.
- Solution: Optimizing the sintering parameters based on the specific requirements of the zirconia material is crucial. This involves conducting thorough testing and experimentation to determine the best settings for achieving the desired material properties.
-
Post-Sintering Treatment:
- Problem: The treatment of zirconia parts after sintering, such as cooling rates and quenching, can impact the final material properties. Rapid cooling can introduce stresses and defects.
- Solution: Implementing controlled cooling processes and avoiding rapid quenching can help in reducing thermal stresses and improving the overall quality of the sintered parts. Gradual cooling and annealing processes are often recommended.
By addressing these key points, manufacturers can overcome the challenges associated with zirconia sintering and produce high-quality, durable ceramic materials. Understanding the intricacies of the sintering process and the role of equipment like the zirconia sintering furnace is essential for achieving optimal results.
Summary Table:
Challenge | Problem | Solution |
---|---|---|
Thermal Shock Resistance | Rapid temperature changes cause cracks or failures. | Use materials and designs resistant to thermal shock, like high-purity alumina. |
Material Properties | Impurities or incorrect compositions lead to defects. | Use high-purity zirconia powders and maintain strict composition control. |
Sintering Furnace Design | Poor furnace design causes uneven heating and inefficient sintering. | Invest in furnaces with precise temperature control and uniform heating. |
Process Parameters | Incorrect settings result in incomplete or over-sintering. | Optimize temperature, heating rate, and holding time through testing. |
Post-Sintering Treatment | Rapid cooling introduces stresses and defects. | Implement controlled cooling and avoid rapid quenching. |
Struggling with zirconia sintering challenges? Contact our experts today to optimize your process and achieve superior results!