Diamond-like carbon (DLC) is a versatile material known for its unique combination of properties, making it highly suitable for wear-protective and sliding applications. It is an amorphous carbon material, often hydrogenated, with a mix of sp3 (diamond-like) and sp2 (graphite-like) carbon bonds. The proportion of these bonds determines the material's characteristics, such as high hardness, low coefficient of friction, chemical inertness, and excellent wear and corrosion resistance. These properties make DLC coatings ideal for use in industries like automotive and machinery, where they enhance the performance of components such as bearings, camshafts, and power trains.
Key Points Explained:
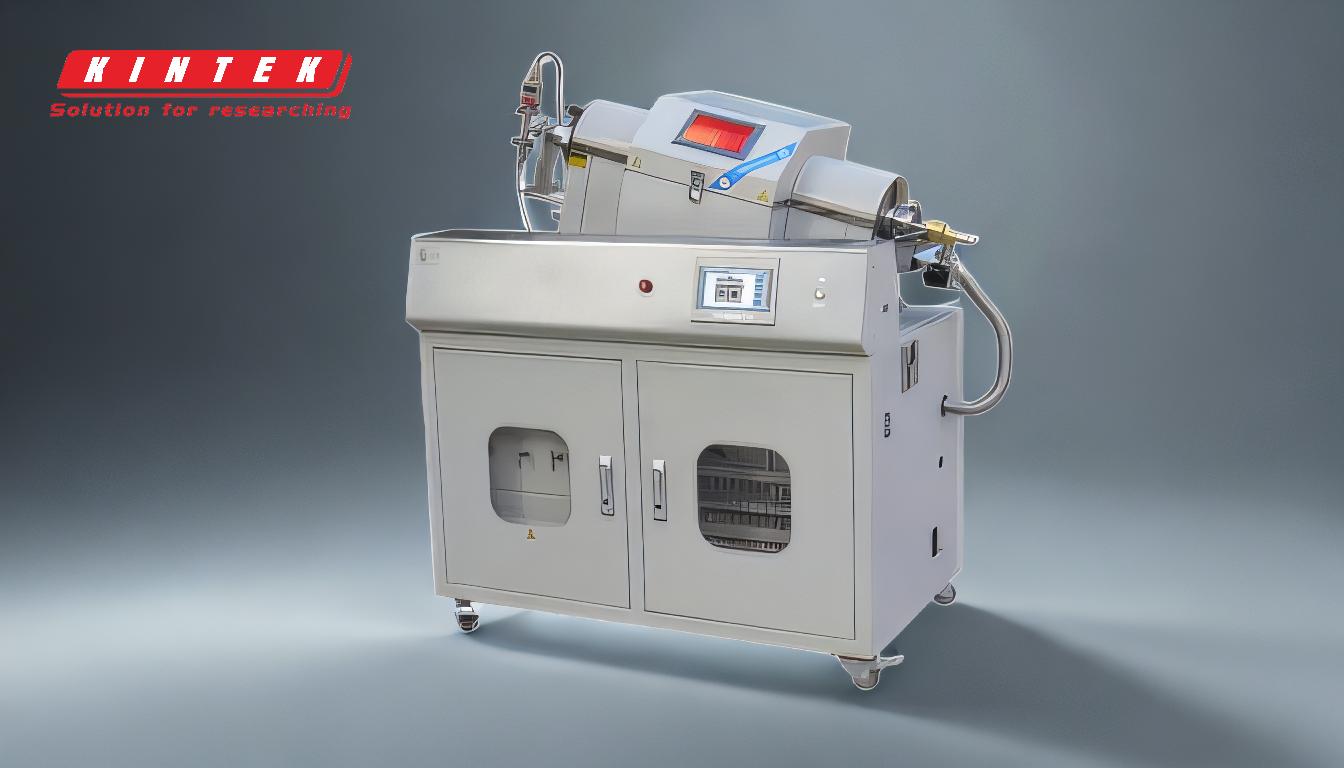
-
Amorphous Structure and Bonding
- DLC is an amorphous material, meaning it lacks a long-range crystalline structure.
- It contains a mix of sp3 (diamond-like) and sp2 (graphite-like) carbon bonds.
- The ratio of sp3 to sp2 bonds influences the material's properties, such as hardness and friction.
-
High Hardness
- DLC coatings exhibit high hardness, typically ranging from 1500 to 3000 HV (Vickers hardness).
- This hardness makes DLC suitable for wear-protective applications, as it resists deformation and damage under mechanical stress.
-
Low Coefficient of Friction
- DLC has a low coefficient of friction, which enhances sliding properties and reduces energy loss in moving parts.
- This property is particularly beneficial in automotive and machinery applications, such as bearings and camshafts.
-
Chemical Inertness and Corrosion Resistance
- DLC is chemically inert, meaning it does not react easily with other substances.
- It performs well in corrosive environments, making it ideal for applications where exposure to harsh chemicals or conditions is a concern.
-
High Surface Smoothness
- DLC coatings provide a high degree of surface smoothness, which contributes to their low friction and wear resistance.
- This smoothness also reduces the likelihood of surface defects that could lead to premature failure.
-
Wear and Chemical Resistance
- DLC films are characterized by excellent wear resistance, making them durable in high-stress applications.
- Their chemical resistance further enhances their longevity in challenging environments.
-
Applications in Automotive and Machinery Industries
- DLC coatings are widely used in the automotive and machinery sectors to improve the performance and efficiency of components.
- Examples include power trains, bearings, and camshafts, where DLC's properties contribute to energy savings and extended component life.
-
Variants of DLC
- DLC exists in various forms, such as ta-C (tetrahedral amorphous carbon), a-C (amorphous carbon), and H-terminated DLC.
- Each variant has specific properties tailored to different applications, ensuring versatility across industries.
In summary, DLC's unique combination of high hardness, low friction, chemical inertness, and wear resistance makes it an exceptional material for protective coatings and sliding applications. Its adaptability to different industrial needs, particularly in automotive and machinery, underscores its importance as a high-performance material.
Summary Table:
Property | Description |
---|---|
Amorphous Structure | Mix of sp3 (diamond-like) and sp2 (graphite-like) bonds. |
High Hardness | 1500–3000 HV, ideal for wear protection. |
Low Coefficient of Friction | Enhances sliding properties, reduces energy loss. |
Chemical Inertness | Resists reactions with harsh chemicals, suitable for corrosive environments. |
Wear and Corrosion Resistance | Durable in high-stress applications, extends component life. |
Applications | Automotive (bearings, camshafts) and machinery (power trains). |
Learn how DLC coatings can improve your industrial applications—contact us today!